Packaging
Allrounder More 2000: Two-component process combines LSR and thermoplastic
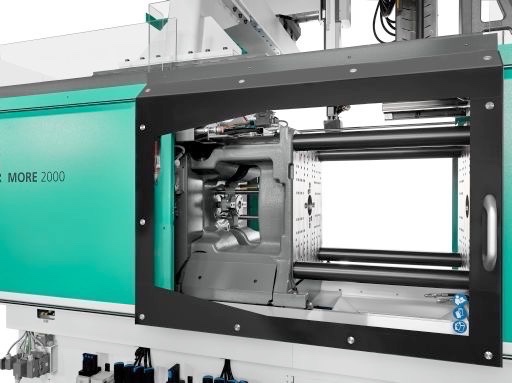
Thursday 19. October 2023 - The modular Allrounders from the More series offer increased space for moulds, more modularity in assembly, and many optimised features for greater ease of use and simple maintenance. Arburg developed this series especially for multi-component injection moulding.
Arburg will be present at Fakuma 2023 with nine exhibits on Stand 3101 in Hall A3, plus ten additional machines on partner stands. An Allrounder More 2000 with two electric injection units will demonstrate how functional integration can save time and money in multi-component injection moulding. The exhibit will produce a multifunctional box from liquid silicone (LSR) and thermoplastic in a reliable, reproducible and energy-efficient process.
The modular Allrounders from the More series offer increased space for moulds, more modularity in assembly, and many optimised features for greater ease of use and simple maintenance. Arburg developed this series especially for multi-component injection moulding.
Two-component machine in advantageous L-position
The Allrounder More machines are available with a horizontal and a vertical injection unit (V-position) as standard. A horizontal L-position will be used for the trade fair application. This makes the two injection units easily accessible. The result is easy maintenance and handling of the peripheral equipment, such as the LSR dosing unit’s mixing unit or the thermoplastic unit’s colouring device. The cylinder module can be installed and removed quickly and easily.
Component assembled directly in the mould
The exhibit, an Allrounder More 2000 with 2,000 kN clamping force in the Comfort performance variant and with two electric injection units in sizes 200 and 400, will produce a two-component multifunctional box made of thermoplastic (PBT with 30 per cent glass bead content) and self-adhesive liquid silicone (LSR, hardness 50 Shore A). The two components are injected directly via a cold or hot runner system, resulting in waste-free production. The associated LSR dosing unit from Reinhardt Technik is integrated via OPC UA and the Euromap interface 82.3 into the Gestica controller, from where settings can be made centrally, the dosing parameters called up and the data set saved. This is therefore always a 1:1 match for the mould. The cycle time is around 60 seconds. First to be produced is the PBT pre-moulded part, which is then converted in the Rico Group’s 1+1-cavity mould so that the LSR component can finally be injected. The complex 3D contour of the component and precise positioning of the pre-moulded part in the second mould station place high demands on the gripper and robotic system. The 164-gram box is finally removed by a Multilift V 30 linear robotic system and placed on a conveyor belt.
100 per cent traceability
As a fluorescent marker has been added to the thermoplastic component, the box – which is not identifiable by the end consumer – is clearly marked. Even a fraction is enough to clearly identify it with a laser detector through its characteristic fluorescence. This technology from Arburg’s partner Polysecure allows products to be clearly traced, distinguished from counterfeits and, if necessary, sorted by material.
Intelligent support: “EnergyAssist” controller function
The Gestica machine controller actively supports the operator with its built-in assistance packages – including when it comes to energy optimisation. The “aXw Control EnergyAssist” assistance function brings together all the essential functions of the plasticising cylinder and mould, for example, and ensures that all heating zones are switched on and off in an optimised manner. This significantly reduces the energy requirement in the heating phase and enables energy-efficient production. “aXw Control PressurePilot” ensures bionically optimised pressure control in the injection moulding process and so constant mould filling and part quality. In addition, “aXw Control ScrewPilot” enables precise screw movements and a constant injection process.
Allrounder More: More space, modularity and convenience
The Allrounder More machines offer more space for larger moulds, rotary units, media connections and a usable ejector stroke. Thanks to their highly modular design and many optimised features for greater ease of use and simple maintenance, they can be adapted very flexibly to the respective customer and market requirements. This means that with the More series, different types of processes can be combined with little effort and all common two-component applications can be realised.
As standard, the Allrounder More machines feature a highly dynamic electric toggle-type clamping unit with energy-efficient liquid-cooled servo motors, two electric injection units and a choice of 1,600 or 2,000 kN clamping force.