Inkjet & Digital Printing
Cefla at Ligna
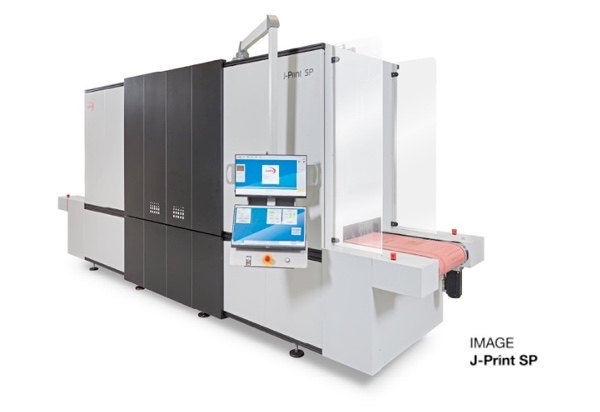
Monday 15. May 2023 - After a long hiatus imposed by the pandemic, Cefla Finishing returns to Hanover to take part in the 2023 edition of Ligna - the woodworking and wood processing industrys most important international trade fair - which will be held from 15 to 19 May 2023. These include the J-Press.
At Ligna 2023 Cefla Finishing will be showcasing the technological innovation that is the hallmark of its surface finishing solutions. On a LAB stand covering over 800 square metres, visitors will be able to observe the transformation from raw materials to finished products, see the results first-hand and discuss the various technologies with our experts.
There will be an area dedicated to Industry 4.0; moreover, five production lines featuring high-efficiency machines will run continuously for the duration of the fair:
AutoCut
Automatic reel slitting equipment designed to process paper, plastic films, sandwich films, lightweight laminates, some textiles and metal foils. Speeds up to 150 metres/min.
AutoCut combines superior disc knife cutting performance with rapid set-up procedures and a hazard-free concept.
Extensive machine automation avoids need for qualified operators and ensures quality is consistent and reproducible.
Narrow friction winding shafts guarantee constant web tension for different widths.
Prints QR code including data which can be read by the downstream profile wrapping machine (MultiWrap Wood) to establish suitability of reel for profile.
Exydry
In line with a hybrid line (spray and roller coating technologies), Exydry is an excimer matting oven for flat and slightly raised panels using significantly reduced quantities of nitrogen.
? Achieves a deep matt value of less than 5 on a 0/100 gloss scale and a fingerprint-proof surface, even on raised panels thanks to a patented innovation.
? Special lamps using a wavelength of 172nm bring about a partially cross-linked micro-structure on the surface, followed by final curing for a deep matt finish with superior resistance and soft-touch effect.
? Nitrogen consumption is reduced by up to 65% thanks also to a patent pending solution which limits the amount of oxygen entering the oven on the conveyed pieces.
? Oven design enables a continuous flow of panels, taking care of full oxygen removal without stopping production.
Easy
Oscillating spray coater with 2 arms which implements a brand new fast colour switch solution.
Managed by a special software and a system which involves the equipments mixing valves, Easy is the platform for the launch of the new FCS system enabling companies to implement colour changeovers without stopping production.
? Colour changeover requires less than 10 seconds compared to the standard 2 to 3 minutes needed today.
? Considering standard shifts and colour changeovers, this new time-saving technology reduces downtime by approx. 45-60 minutes/day.
? Significant reduction of wasted lacquer at each colour switch; approximately one tenth of the amount lost each time.
? Reduced consumption of water or solvent used to flush out lacquer of the unwanted colour.
iBotic
Interpolated axis Cartesian spraying robot for high quality finishes and high production volumes.
With two arms operating independently, different pieces can move in a constant flow while being sprayed.
Can be equipped with TIMESKIP for colour changeovers that do not require the machine to be stopped.
? TIMESKIP enables zero downtime, allowing you to maintain production with one arm while you switch lacquer colour on the other.
? Interpolated axis means you can use the two arms on iBotic without ever risking them colliding in the spraying area.
? Arms travel along 5 axes including the horizontal position achieved to spray panel edges.
? Easy to program and use even for complex trajectories, latest-generation software enables total control.
UV-I
An inert curing oven developed to complete a roller coating line using 100% UV lacquers, UV-I minimises the need for photoinitiators and reduces the unwelcomed yellowing effect that photoinitiators provoke.
? Reduction of photoinitiators can vary between 40 and 70% with relative reduction of lacquer costs.
? Greatly improves sustainability of the process by minimising presence of photoinitiators which are harmful to the environment.
? With the same amount of photoinitiators in the lacquer, one benefit is acceleration of the curing process, therefore lower operating costs and better productivity.
? Simple, seamless integration into an existing roller coating line using 100% UV lacquers.
Smartvacuum
Cost-efficient, sustainable solution for edge finishing using vacuum technologies for 100% UV Acrylic paints.
Used together with Smartedge, it enables companies to match the edge and surface finish perfectly.
? Deposits 100/140g per sqm of 100% UV lacquer in a single step, thereby reducing coating stages, processing times and handling operations.
? Absence of solvents lead to a more sustainable process and eliminates related costs.
? Combined with Smartedge, using the same vacuum technology, the result is a perfect match achieved in a streamlined process.
Smartedge
A highly flexible integrated solution for painting and sanding straight and shaped panel edges.
Used together with Smartvacuum, it enables companies to match the edge and surface finish perfectly.
? All-in-one edge processing solution for an uninterrupted flow of sanding and coating operations on one single machine incorporated into a vacuum coating line.
? Faster time to market with fewer processing stages and fewer handling operations, all with a smaller overall footprint.
? Same application technique, same lacquer used for surface and edge, same top-quality matching finish.
Smartcoater PRO
Latest-generation roller coating machine featuring exclusive innovations for flat or slightly raised panels.
Equipped with a soft rubber application roller and special pneumatic floating system to process poorly calibrated flat panels or panels with an up to 10 mm groove.
? Able to apply a base coat to raised panels allows you to install hybrid finishing lines made up of two roller coating stations and a spray coating machine for the top coat.
? Fewer handling operations, no intermediate sanding between base coats, fewer abrasives, all leads to lower costs, less manual labour and reduced factory floorspace.
? Transfer efficiency on roller coaters significantly reduces lacquer consumption and consequent solvent consumption.
? Fewer rejects thanks to a built-in system using screw jacks and a pneumatic device to compensate poorly calibrated panels and maximise productivity.
MultiWrap Wood
Processes profiles made of wood as well as MDF, HDF; door frames, picture frames, skirting boards, plinth panels and furniture parts. Ease-of-use, efficiency and minimal downtime.
Each single machine can be specifically configured according to individual customer requirements thanks to modular concept.
High-speed profile changeover, double unwinders, improved tooling replacement for easier operator intervention.
User-friendly control panel displays images for intuitive, language-free interaction with the machine.
Reads QR code printed on reel from upstream slitting machine (AutoCut) to check suitability for each process.
Lamination equipment
Easily integrated into complete panel lamination and wrapping lines, they process reels up to 1400 mm in width and ensure high-quality gluing and work for a broad spectrum of substrate types and profile types.
? Suitable for standard, high-gloss and ultrathin lamination materials, it can be used for furniture panels, caravan or boat interior surfaces.
? Processes U-shaped and L-shaped profiles, as well as J-Pull handles, combining lamination and wrapping operations.
? High-quality hot glue application system doses glue carefully and ensures energy efficiency.
? Reel (both upper and lower) changeover mechanism is simple to use and operators also benefit from an auxiliary system to facilitate reel feed.
J-Print
Range of industrial digital printers enabling highly customised decorations and minimum time to market.
A solution for parquet flooring enabling beautiful natural patterns and superior foot traffic resistance at a reasonable cost.
? Special inks guarantee excellent wear resistance and production speeds reach 50 m/min.
? Tactile effects are obtained using integrated printing and texturing lines handling substrate
preparation, digital printing and finishing.
? The J-PRINT TD model performs embossing in register and printing with 400 dpi resolution.
? Our digital print specialists provide a series of useful guidelines to support companies achieve their goals, ensuring top quality at affordable process costs.
iGiotto
Integrated spray coating system using anthropomorphic robots for large products on overhead lines.
Ideal for doors, window frames or objects with a complex shape, especially when preceded by a 3D reading barrier such as cVision.
? Constant speed and constant distance between the spray guns and the product optimise lacquer consumption and ensure coating consistency.
? Optimised lacquer consumption leads to less water for flushing, less lacquer wasted during colour changes, less filter consumption, disposal costs and maintenance.
? The 3-gun wrist, especially for coating doors, enables companies to enhance their production efficiency compared to the conventional 2-gun wrist.
? While spraying the front of the door, just one pass is necessary reducing spraying time by approx. 40% and there is no need to have crossover trajectories.