Offset Printing
PS-PrintService relies on the latest printing technology from Koenig & Bauer
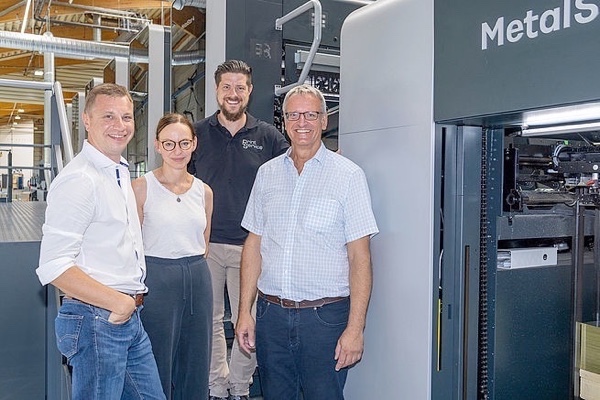
Wednesday 07. September 2022 - Te companyt mainly prints and finishes metal sheets for the production of crown caps and aluminium screw and twist caps. It also prints motifs for food packaging of all kinds as well as for jewellery and cosmetics boxes.
PS-PrintService has been working with Koenig & Bauer MetalPrint presses since the opening of its Neuhaus-Schierschnitz plant in 2004. PS-PrintService is a medium-sized company in the south of Thuringia. It mainly prints and finishes metal sheets for the production of crown caps and aluminium screw and twist caps. It also prints motifs for food packaging of all kinds as well as for jewellery and cosmetics boxes.
With the investment in the new six-colour printing line, PS-PrintService is expanding its capacities to meet the existing demands of the market. The combination of the new MetalStar 4 printing line together with the six-colour MetalStar 2 line installed since 2012 significantly increases productivity. The decision was made in favour of the MetalStar 4 because it is technologically and digitally forward-looking and was individually adapted to PS-PrintService’s requirements.
Project manager Thomas Meusel is convinced: “Installing a new press on this scale was an exciting project in itself. The decision in favour of the MetalStar 4 was exactly right. Koenig & Bauer has done a really good job both in terms of digitalisation and in terms of making things easier for our staff. The press enables “real” digital networking. The feedback from our printers was excellent from the first day of production.
The decision to install such a system during the pandemic was a courageous one. The challenges were enormous on both sides. Together with Koenig & Bauer we overcame all hurdles and found creative solutions to keep to our schedule.”
The latest generation of the MetalStar press series has a modern design and is a real eye-catcher. The production line at PS-PrintService consists of a six-colour MetalStar 4 press, an SMS for feeding metal sheets out and back in and a triple-box stacking system with vacuum overhead brake. It combines maximum flexibility with the highest production quality. The functions of the individual components are automated, enabling the shortest possible changeover times for the next job. This means that even very small job sizes can be produced economically.
The design of the press line was specially adapted to customer requirements. Operation of the MetalStar 4 has been relocated to the drive side, so that the control consoles of the existing MetalStar 2 and the new press line are installed on one side for ease of operation. The DensiTronic quality colour measurement and control system, which guarantees perfect compliance with colour values and automatically suggests any necessary adjustment corrections, was configured at PS-PrintService to be used for both lines. In addition, the MetalStar 4 was equipped with an efficient ink mist extraction system that extracts the resulting ink mist directly at the source, i.e. at the inking unit.
Another step towards digitalisation
Managing director Christel Rauh explains: “I’m thrilled! In principle it prints like our “old” press, offset of course, and hopefully that won’t change anytime soon. In offset you can still feel the pressure. But the latest technology also makes it possible to take the step towards Digitalisation 4.0. The complete link between job management – prepress – press and controlling is made possible by the new technology.”
“The MetalStar 4 makes printers’ work easier! Plate changing, roller washing, adjustments and response time – everything works much faster. Jobs can be prepared more quickly via the LogoTronic and are ready for immediate retrieval. Via the new control console I can operate and monitor everything completely intuitively. The leap from the old press to the new one is enormous,” adds print shop manager Daniel Suffner.
The MetalStar 4 at PS-PrintService is equipped with the following features:
ErgoTronic console
An intuitive user interface on all touchscreens and ergonomically designed control panels facilitate handling. Via the ErgoTronic console, the heart of the operation, all functions can be conveniently controlled on the 23″ touch screen. For example, the job changeover programmes can be set or new print jobs prepared. Measurement results are displayed on the 75″ wall screen.
LogoTronic job management
LogoTronic job and master data management ensures continuous documentation and automatic transfer of job data from prepress to press via CIP link. All data for repeat jobs are reliably stored.
SIS – Sensoric Infeed System
The MetalStar 4 is equipped with the DriveTronic SIS system, the pull-mark-free system. The sheet has more time to settle and align. The SIS system has proven itself for both thin and thick metal sheets, scroll sheets and aluminium.
Set-up time optimisation
The MetalStar 4 guarantees a further step towards shorter makeready times. Thanks to the optimised FAPC (Fully Automatic Plate Change) system, all six plates can be changed in just 2.5 minutes. The plates are changed in three cycles, regardless of the number of printing units. The press is conveniently operated from the ErgoTronic console. The CleanTronic Synchro washing system in combination with DriveTronic SRW (Simultaneous Roller Washing) washes all inking units, blankets and impression cylinders fully automatically and synchronously on request.
New in metal decorating – air-supported ink ducts
New are the air-supported ink fountains. These prevent the ink zones from “sticking” and thus increase the reliability and longevity of the actuators. The intervals for time-consuming cleaning and recalibration of the control elements are thus extended. This is a significant improvement, especially for highly reactive UV inks and UV LED inks.
Triple-box stacking
PS-PrintService has again opted for triple-box stacking with a dynamic vacuum overhead brake. The first pile shaft is used for discharging the infeed pallets. The full pallets are discharged laterally by means of a chain conveyor. The second stacking box was designed in such a way that both defectively detected sheets from the camera inspection systems and good sheets can be discharged. The third stacking box is designed as a good sheet box and, together with stacking box 2, can also be operated as non-stop stacking for good sheets. All stacking boxes are equipped with automatic format adjustment.