Offset Printing
SMG Group chooses Komori once again, with a new fleet of four presses
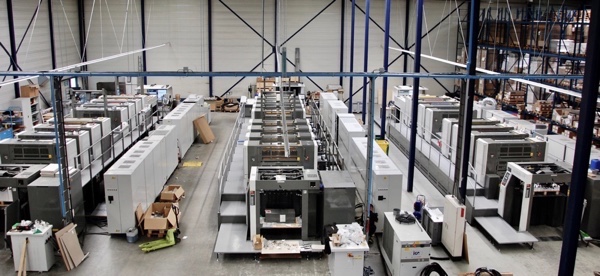
Tuesday 23. November 2021 - Fortunately we have been able to work fast and efficiently with Komori to reduce our downtime. With three Komori Lithrone G840P presses running in Hasselt, and a fourth Lithrone G540 advance with coater on its way to subsidiary company DrukwerkMAX, SMG is back on track.
The familiar sound of the Komori presses returns to the SMG-group in Hasselt, The Netherlands, with the installation of a new fleet of Komori presses. “We are back!”, says owner and director Pieter Brundel.
Just 6 months after the devastating fire at the SMG facilities in which the presses of the printing house were lost, we got back on our feet.
During the corona outbreak, Pieter and Barbara Brundel decided in June 2020 to continue the takeover of the SMG Group. This couple sees it as their challenge to unfold the potential of this group of graphic companies, who each carry their own set of specialities. The online business, making up one-third of the turnover, came to a complete standstill. Regardless of the unpredictable outlook, Pieter Brundel took a chance to move forward. With the cooperation of Bert Boxem, technical production manager at SMG Group, Brundel starts in late 2020 to make plans and asks “How is the company, the group and the production going to be restructured for the future? What do we outsource and what are our resources to produce these ourselves, and what machines are required for that?”
How to continue after the fire?
Early 2021, during a slow and quiet start, SMG is fortunate to receive plenty of jobs. The Komori presses in Hasselt produce lists and voting forms around the clock for the elections to the House of Representatives. In addition, a large job order is received for the Covid-19 test sites across the Netherlands.
But then, at the beginning of April, on Easter Monday, a hazardous fire breaks out in the printing facility. A 10-colour, two 8-colours and a 5-colour press are heavily damaged and beyond repair. The finishing equipment and part of the printed jobs could not be saved. Pieter Brundel “Our main concern was, how can we help our customers in the best way possible?” Bert Boxem: “Fortunately we could fall back on the plans we made earlier. We were already focused on the replacement of presses and were now forcefully able to realize and execute those plans.”
Komori once again
The management and approximately sixty employees jointly put their hands to work. The production of jobs is transferred to DrukwerkMAX in Duiven, which falls under the SMG Grafimedia umbrella. The capacity at DrukwerkMAX was scaled up to host the extra print jobs. “Luckily we could count on other printing houses and printers to help us where necessary. Barbara Brundel says “They made their presses and finishing equipment available so that we could continue to serve our customers” Various suppliers of equipment and material supported the company in their time of need. Pieter Brundel: ” The decision to choose for Komori once again quickly came to be. We were already satisfied with the quality and efficiency of their presses, and from a cost of ownership perspective, Komori is an attractive choice. The most important aspect was that Komori supported us and helped us with the difficult decisions to deliver new presses in a quick and timely manner”.
Presses equipped with LED- and H-UV
Six months later, SMG underwent a metamorphosis. The former factory is still being renovated, but three 8-colour Komori Lithrone 840P presses have now been built in the factory hall next door, where the inventory warehouse was located. Bert Boxem: “One of the presses uses conventional inks while the two other presses are using UV inks. Equipped with LED-UV, and H-UV drying. Moreover, those two presses are equipped with cameras that monitor and secure the print quality.”
Pieter Brundel explains: “The presses equipped with LED- and H-UV curing system are ideal for internet printing, which requires a short turnaround. Because the printing jobs are immediately dry, you have more flexibility in your sheet layout and can cut your prints immediately. The cost price of these special inks is higher than conventional inks, hence why we use this on our third press so that we have an alternative.”
Confidence in the future
At the moment new CTP equipment, folding machines, an automated cutting machine and a perfect binding line have been installed in Hasselt. The printer is now operating in three shifts, five days a week, and Pieter Brundel and his team are getting back on track.