Finishing & Screen Printing
Polar-Mohr: Two innovations for the anniversary
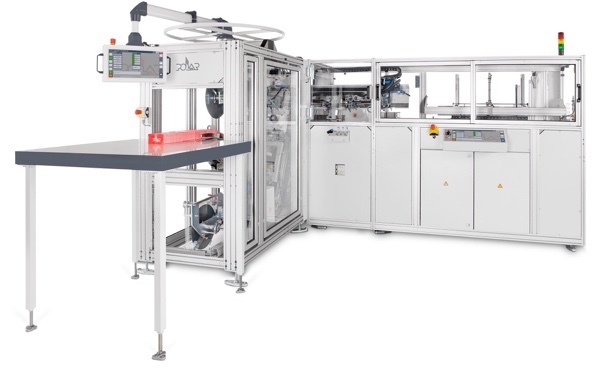
Tuesday 29. June 2021 - POLAR has been the supplier of automation solutions in the post-press sector for decades. In 1985, POLAR introduced Compucut, the first software for the automated creation of cutting programs, which reduced set-up times and waste to almost zero.
During the Showtime Event of Heidelberger Druckmaschinen AG, POLAR presents two new systems as part of its automation strategy. An already established system receives a performance upgrade.
These first auto- mation efforts as early as the 1980s increased in 2003 when the first PACE (POLAR Automa- tion for Cutting Efficiency) system was introduced. PACE is a system that allows 4-times higher productivity compared to standard high-speed cutters.
Just in time for the anniversary, two autonomously operating systems follow, AirGo Jog and DC-12 RAPID. AirGo Jog for preparing the material to be cut without manual intervention and DC-12 RAPID, which produces die-cut label bundles and packs them in trays ready for dispatch. The latter is a joint development of POLAR and its subsidiary DIENST Packsys- tems, a manufacturer of packaging solutions for the food and non-food industries.
AirGo Jog: Operator-free ream preparation
Fastest system on the market
By jogging the complete cutting layer, an extremely short cycle time of approx. 60-90 sec- onds per 16 cm cutting layer is possible. All existing automatic jogging systems on the mar- ket process partial layers and therefore need at least twice the time to prepare the layer.
Maximum flexibility
AirGo Jog is highly flexible with format ranges from 50 x 70 cm to 78 x 106 cm.
Critical materials such as glued sheets, protruding or folded corners, difficult grammages and small formats can be jogged at any time in manual mode, which is available at the touch of a button. Switching between manual and automatic is therefore possible immedi- ately.
Different ream heights can be processed without changeover. This is a major advantage, especially in the Web2Print sector, where each layer can be a different job.
Best ergonomics
In the material preparation process, the physical strain must not be disregarded. The high degree of automation of the system promises the best possible physical relief for the oper- ator and reduces downtime.
Manual interventions for material transport, separation and fanning of the sheets are elimi- nated. After all, up to 40 tons of paper otherwise have to be lifted in one shift during this work step.
With AirGo Jog, only one operator is required for the entire cutting process.
Job changeover at the push of a button
AirGo Jog is operated via an HMI based on the latest industry standards, which is character- ized by simple and intuitive handling.
Job changes are largely automated, with the exception of the actual pallet change, so there is hardly any set-up time when changing jobs. Job management is available for reoccurring jobs.
Wide range of applications
Reliable runtimes are ensured by the use of standard components.
The POLAR modular system allows easy retrofitting to existing cutting systems or PACE sys- tems. In addition, AirGo Jog can also be used as a stand-alone solution for feeding several cutting systems.
State-of-the-art control technology
The future-proof new industrial control system allows data exchange and integration into the workflow, as well as the remote service function, which further improves machine avail- ability. The system is even prepared for predictive maintenance with the new control plat- form.
DC-12 RAPID
Fully automatic from the sheet to the tray
A combination of modern robotic packaging equipment and proven POLAR Label technol- ogy for autonomous die-cutting of labels.
Synergies in the development between POLAR and the packaging specialist DIENST, made a fully automated, operator-free process possible: from the cutting layer to the shipping package. RAPID – this stands for Robotics for Autonomous Processing of Industrial Die-Cut labels.
Most efficient system on the market
The highly efficient POLAR LabelSystem DC-12 PLUS, which at 1440 bundles per hour is the fastest system on the market, was the basis for the new development. Further, sophisti- cated automation components help the proven system for processing die-cut labels to new top performances. These components consist of a system for automatic loading of cutting layers, an automatic cutter for fully automatic cutting of strips and, at the end of the work- flow, a sorting and packing station that picks up individual bundles by robot, turns them and places them sorted in the tray.
In the LabelSystem DC-12 RAPID, the robot takes over what is otherwise usually a manual process of packing 24 label bundles per minute.
High ergonomics
In addition to the efficiency aspect, this also eliminates the physical strain of manual pack- aging. In general, the high degree of automation of the system promises the best possible ergonomics, as manual interventions during production are eliminated.
Job change at the push of a button
New components are operated via an HMI that meets the latest industry standards. Inputs and format settings are intuitive and easy to handle.
Setup times are minimized. Job management is available for repeated jobs. A format change takes only 15 minutes thanks to the menu-guided job change, the format memory and POLAR OptiChange – the patented change frame system. OptiChange reduces make- ready times by allowing large parts of the job change to be prepared outside the machine.
Future-proof technology
The future-proof new industrial control system enables remote service for further im- proved machine availability and integration into the digital workflow. In addition, the sys- tem is prepared for predictive maintenance.
DCC-12
Best performance due to new control system
In the area of counter pressure die-cutting, the introduction of a new control platform also helps to achieve new levels of performance. The new DCC-12 LabelSystem operates, as be- fore, on the counter-pressure principle and is therefore ideally suited for compressible ma- terials. However, the system has received a significant performance upgrade. The new con- trol system has enabled improvements to various parts of the system, resulting in a 25% increase in productivity. The new DCC-12 achieves an output of 10 bundles per minute.