Offset Printing
How BOBST is supporting converters demands in corrugated packaging
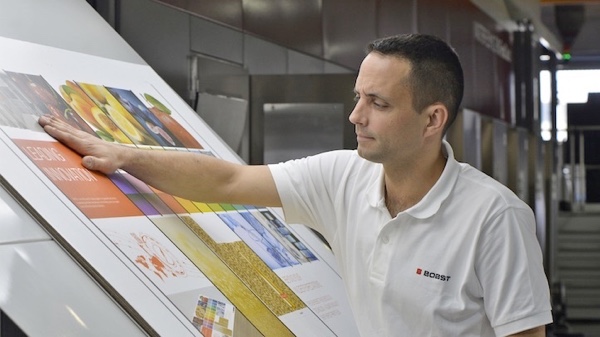
Thursday 21. January 2021 - Key trends in the packaging sector put many demands on converters and brand owners alike. New customer preferences and shopping behaviors, along with a surge of regulatory sustainability targets, are changing the market. The need for shorter time to market and faster delivery are additional factors putting increasing pressure on costs.
In order to respond to and survive these challenges, the corrugated sector must produce high-quality packaging with short lead times.
As a leading equipment manufacturer, BOBST works hand-in-hand with converters to enable them to produce fault-free packaging and satisfy the needs of their clients. The company has been spearheading innovation in the flexo post-print arena for more than four decades, developing sheet-fed printing and processing equipment for the production of high-quality printed corrugated board.
To continue this process, BOBST is building its future vision of the packaging industry on four pillars, digitalization, connectivity, automation and sustainability to offer unrivalled productivity, sustainable production and predictable results.
Giving converters the tools for success
“In order to produce the highest quality graphics when printing flexo onto corrugated board, there are three crucial elements to consider: the printing press itself, the consumables and the production team. Those elements must work together in harmony to overcome the specific challenges of this process and meet the needs of the customers in the post-print flexo sector,” stated Guillaume Martin-Bastenaire, Printing Process Expert at Bobst Lyon.
BOBST has a comprehensive portfolio of flexo presses for the production of unmatched print quality at lower cost, all in one pass. At the high end of the spectrum is the BOBST MASTERFLEX HD, which is a benchmark for all 2,100 x 1,300 mm format flexo presses. With a host of advanced control technologies and automatic adjustment features, it offers a credible alternative to offset printing, with exceptional print quality and significant savings across the process.
BOBST offers two levels of print quality for its inline solutions, which can be fitted with either High Graphics or THQ (Très Haute Qualité) FlexoCloud technology to give converters the tools to produce exceptional flexo post-print jobs and increase their market share.
High Graphics mode offers super sharp images and high-density colors in one pass to meet brand owners demands for outstanding visual appeal and match color targets. Meanwhile BOBST unique oneECG THQ technology takes print quality to the next level while also meeting sustainability targets through its use of extended color gamut printing.
The oneECG THQ technology uses a fixed set of colors, which drastically reduces production costs by saving on ink and other consumables, and also minimizes the number of changeovers and downtime. Printing in CMYK will cover 65% of the color gamut. This can be increased to 90% with an expanded ink set where three colors, typically orange, green and violet, are added to CMYK.
Automating for higher precision
BOBSTs technology innovations are improving quality and productivity across the process, giving the converter a competitive edge. Higher automation on press means faster setups, excellent registration, highest color accuracy, and perfect sheet handling and positioning, resulting in savings in waste and time for more sustainable production.
Take registration as an example. BOBST has developed REGISTRON S6500, a user-friendly, high-quality sheet-positioning system with easy set-up. Accuracy of the sheet transportation through the machine also guarantees the registration value color to color to achieve a better printing quality with clearer images. This can be combined with the pioneering BOBST Start&Go system, which offers fast automatic set-up at the start of each job in just a few sheets.
Olivier Robin, Bobst Lyon Sales Director, explained, “Thanks to our control management and corrective systems, BOBST can guarantee perfect sheet positioning in each printing unit. At the start of the job, REGISTRON S6500 automatically sets up cross and longitudinal register values for each color to guarantee the best printing quality from the first sheet. Thanks to the Start&Go system and REGISTRON S6500, it also adjusts skewing and printing length for each unit to save on production time and provide support for multi-color jobs.”
Every little detail count, and all elements of the printing process must be monitored. For instance, the precision and repeatability of cylinder calibration is vital – an anilox roller in the wrong position or excessive pressure on the printing plate will adversely affect quality. Therefore, BOBST manufactures its own cylinders to guarantee perfect geometry both along and around the cylinder. Cylinder positioning in the machine is precise and repeatable to within 0.01 mm to help the operator achieve best machine setup.
Partnerships for the benefit of all
Exceptional technology and innovative solutions are only part of the equation. Customer sales support and service is equally important to ensure converters optimizes the potential of their machinery. BOBST has a team of training and printing process specialists available for sharing skills and expertise in flexographic printing. Its Competence Center in Lyon has a special focus on flexographic corrugated post-print and offers specific process training on press and in converting, including printing, die-cutting and more, all adapted to customers needs and demands.
Customer can also access training and support remotely through the MyBOBST dedicated online portal, where they can also monitor real-time machine data, access technical information and order spare parts. This online interface offers significant time savings and is available 24/7.
Helping to further cooperation in the industry for the benefit of all parts of the supply chain, the Lyon Competence Center works closely with a number of ink, printing plate and other consumables suppliers to improve the process, validate new technical solutions, exchange knowledge and participate in customer training.
Olivier Robin concluded, “As a machine manufacturer, BOBST works hard every day to guarantee the best quality of its printing machines, support its customers and enable them to stay ahead of the competition, as well as capitalizing on industry knowledge and sharing it in order to enrich the printing process for all parties involved. We work in partnership with converters and other suppliers, and together we are shaping the future of packaging.”