Consumables
Agfas new Energy Verve pre-heat printing plate combines cost efficiency with high performance
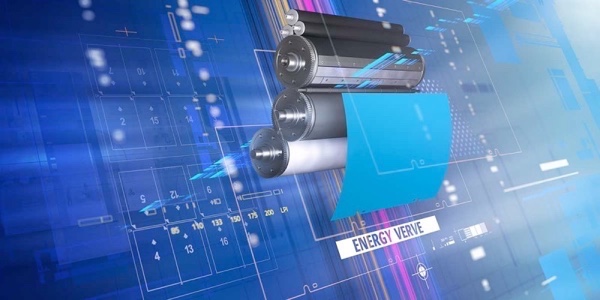
Monday 29. June 2020 - Energy Verve is a negative-working, pre-heat, photopolymer offset printing plate targeted at heat-set web (e.g. magazines and retail), cold-set web (e.g. newspapers and books), as well as packaging & commercial sheet-fed printers that typically deal with highly demanding and abrasive print conditions with oxidative and UV inks.
Thanks to its high chemical and mechanical resistance, Energy Verve can handle print runs up to 1 million copies. In addition, its high sensitivity and non-ablative photopolymer layer maximize plate throughput of the platesetter.
Cost reductions
Since Energy Verve replaces the post-bake oven with a pre-heat module requiring a lower temperature, it brings down printers energy consumption by up to 50%, and service costs by up to 65%. In addition, plate waviness or cracking issues will disappear. Also, the pre-heating modules footprint is smaller than that of a post-bake oven.
“Heatset printers are struggling with ways to increase efficiency and to decrease costs. In particular, they are torn between the wish to get rid of their baking oven, and the frustration that the run length of non-baked plates is not fulfilling their expectations” says Iris Bogunovic, Product Manager Plate & CTP Systems. “Energy Verve is the perfect middle ground between post-bake and non-bake, offering high run lengths in combination with both process- and cost-efficiency.”
High performance on press
One of the key cost drivers for heatset printers are paper web breaks, which especially occur in the case of lightweight paper or multiple format changes. Energy Verves specific design eliminates web breaks. “The main cause of web breaks is that the paper gets soaked by the excessive use of dampening solution used during printing to obtain a high-quality print,” explains Thomas Billiet, R&D Project Manager at Agfa. “The deeply grained aluminum substrate of Energy Verve provides an excellent ink/water balance and enables printers to use a minimum of water and achieve more stable print conditions, thus eliminating web breaks.”
Iris Bogunovic adds: “Web breaks can occur multiple times a day, with an average press downtime of at least half an hour per occurrence. Taking into account the cost of damaged blankets, washing, paper and ink waste too, a single paper break easily costs between EUR 500 and 1000 per interruption. Reducing web break frequency leads to enormous productivity gains as well as savings.”
Part of ECO³
Energy Verve is part of Agfas ECO³ approach, consisting of a wide range of hardware, software, consumables and services that make printing operations cleaner, more cost-effective and easier to manage and maintain.
Availability of Energy Verve depends on the region.