Inkjet & Digital Printing
A brilliant idea for batch size 1
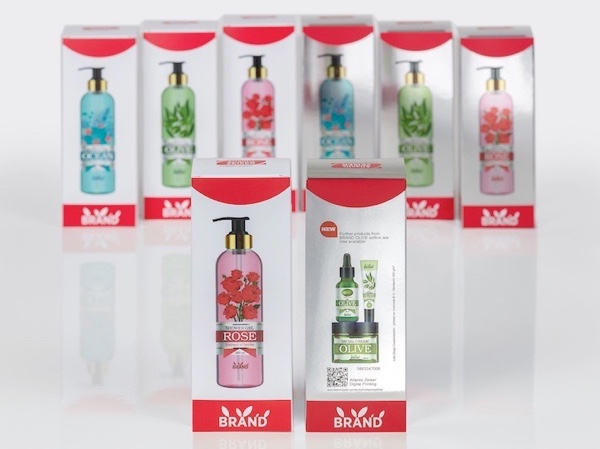
Tuesday 04. February 2020 - It is another important milestone on the way to making batch size 1 efficient in the packaging of consumer goods: In a joint development project, Atlantic Zeiser, ink specialist Tritron and Actega, a company specialising in overprint varnishes, have demonstrated that an analogue clear varnish applied to folding boxes can be subsequently combined with brilliant UV LED inkjet printing.
Complex solutions with corona or plasma systems for pre-treating the surfaces become just as superfluous as special coating cut-outs. The three companies have succeeded in coordinating ink and offset coating formulations in such a way that they harmonize perfectly with each other, printing companies and brand manufacturers alike no longer have any restrictions in Late Stage Customization and any further surface pretreatment of the folding box board is no longer necessary. The usual protective coating over the ink printed in offset thus additionally serves as a primer for subsequent UV LED inkjet printing. The gloss level of the new coding varnish corresponds to that of conventional dispersion varnishes, as does the processing in the coating unit. The result is a closed and protected cartonboard surface with no haptic difference. With the UV LED-curable ink developed by Atlantic Zeiser and Tritron, a pin-sharp print quality (Barcode Grading A), excellent adhesion according to the TESA test and outstanding scratch resistance (Erichsen) are achieved on this coding varnish. Two well-known pharmaceutical companies and a cosmetics manufacturer are now using this solution from Atlantic Zeiser, Tritron and Actega.
Optimal solution for large surfaces
Up to now, dispersion coatings available on the market have shown two deficits when it comes to the use of subsequent UV LED inkjet printing:
Adhesion and scratch resistance were not given and the print quality was insufficient depending on the coating properties. However, coating cut-outs were only a proven remedy for small coding areas. But if – as intended – whole pages of a package are individualized during Late Stage Customization, this was not possible for visual reasons alone. The gloss and brilliance would then simply be missing on a large surface, and the carton would also be unprotected on this side.
However, the alternative use of corona or plasma systems for pretreating coated surfaces meant not only additional investment but also cuts in terms of flexibility, process reliability and efficiency. After all, setting up these systems was always time-consuming and often error-prone.
The solution developed by Atlantic Zeiser, Tritron and Actega is an important milestone in efficiently exploiting the advantages of digital printing. Brand manufacturers and printers now have an economically very interesting solution package at hand. It delivers superior print quality, both monochrome and in four-colour printing, at speeds of up to 60 metres per minute. Personalized packaging thus becomes a brilliant idea in the truest sense of the word.