Packaging
Successful two-day Coating Technology event at Bobst Italia
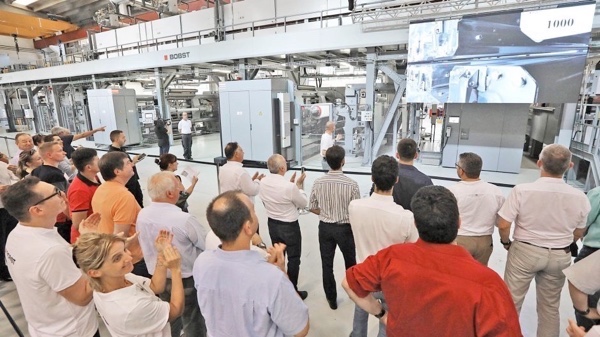
Thursday 06. September 2018 - Over 100 participants from Europe, Asia and the Middle East joined BOBST, and other leading experts from different facets of the silicone coating and barrier film industries, for a two-day Coating Technology event organized by Bobst Italia, in San Giorgio Monferrato Italy, on 25 and 26 July 2018.
Planned as two half day sessions aimed at increasing participants knowledge of the industry outlook and state-of-the-art technologies, the occasion also marked the presentation of two BOBST CO 8000 latest generation coating lines designed for the market segments.
“We are committed to deliver value in its broadest sense to our customers process, which is something that goes far beyond the engineering of high performance machines,” explained Detlef Merklinger, Head of the Coating Product Line, Bobst Italia. “This is why the aim of this event was not only to present two of our CO 8000 machines, but also to bring together the strengths of leading companies in these two segments of the coating market, which are projected for continuous growth and fast paced technological evolution.”
The deep-dive sessions took place at Villa Morneto, a stunning venue in the UNESCO World Heritage hills of the Monferrato. The event was opened by Detlef Merklinger who gave an overview of the impressive global growth of BOBST coating technology in a number of key specialty applications and highlighted the uniqueness of BOBST in being a single source supplier that delivers coating solutions 100% developed in-house. He concluded his presentation illustrating the layout of the dedicated coating technology center currently under construction, which will house an innovative coating pilot line equipped with several different process technologies and systems.
On the subject of silicone coating applications and processes, chemical company Evonik spoke about UV curing silicone release coatings; free radical UV curing and cationic curing, their respective advantages and fields of application, anchorage, stability, and food and skin contact legislation.
UV lamp manufacturer IST Metz highlighted the advantages of light curing and how inertisation with nitrogen enables better crosslinking and safety in terms of barrier to migration and its implementation on converting equipment for board and film.
Chemical company Dow Consumer Solutions gave an overview of the silicone-related coating market in terms of application technologies, thermal silicone applications and processes, and tackled industry challenges such as reduction of platinum dependency, down-gauging of materials and silicone migration.
Also attending as guest speaker was Olivier Lavaud, CEO of release paper and film manufacturing company ITASA, owner of the CO 8000 silicone liner machine on show. He gave an interesting perspective, from the point of view of a specialty converter, on the outlook for the future development of the global market. Headquartered in Spain, ITASA is a global player in its field with manufacturing facilities on three continents.
Gianni Zanatta, Product Manager Coating, Bobst Italia, presented BOBSTs silicone coating technology and equipment, as well as the configuration of ITASAs high performance CO 8000 silicone coating machine, specified for paper and film release liner applications, on show.
The exploration of new generation of barrier films and coatings, which are challenging more traditional barrier packaging structures, and the trends towards down-gauging and development of highly functional monolayer and composite barrier materials, also drew great interest and BOPP film manufacturer Treofan shared information relating to the evolution of coated films to fulfill evolving market demands and developments, as well as the functionality of coated films in preventing mineral oil contamination of packaged products.
On a broader outlook the presentation by water-based coating manufacturing company Michelman dwelled on the major market trends that the company has identified as driving the market in the next five years. The main focus was on a water-based coating formulation that enables fragile AlOx coatings to undergo further printing and converting processes without damage, which very much intertwined with the two BOBST presentations on the subject. The development was as a result of collaboration between BOBST product lines and Michelman to bring to market an industrial solution for AlOx barrier products.
The technicalities of manufacturing, and the physical properties of materials such as AlOx or SiOx that can be produced on BOBST metallizers, as well as other process developments aimed at increasing metallization adhesion and defect prevention, were explained by Pedro Bartolus from Bobst Manchester. With the presentation of the CO 8000 for AlOx top coating on show at the event, Mirco Zisa, Sales Manager Coating, Bobst Italia, closed the loop on the turnkey integrated solution that BOBST offers in the field of high barrier functional substrates. This market is also developing fast in light of major brand owners pledge to make their packaging material recyclable by 2025.
Mirko Rinco, R&D Coating Engineer, Bobst Italia, talked to the BOBST value proposition for different market segments and applications, while Christian Montanari, Service Director, Bobst Italia, presented the huge capabilities of BOBST at global level in terms of local presence and available services. In particular, he addressed the advanced level of connectivity featured in all installed BOBST machines since 2014.
After lunch the action moved to Bobst Italias production plant. Different systems and solutions to process challenges were illustrated in the course of the sessions and experienced up close by the visitors. Although the two lines on show addressed different types of applications, market sectors and process technologies, both stem from the CO 8000 platform, reflecting the BOBST strategy to have a basic platform which can be customized by adding specifically developed units for each customers specific application requirements.
The CO 8000 silicone liner machine, 1700 mm (67 ins) web width, was configured for solventless thermal silicone coating on paper and film and featured BOBST solutions for perfect process integration and seamless workflow. These included, in this instance, an inline flexo printing unit with a print repeat up to 1200 mm, a sleeve system for fast job changes on both anilox and print cylinder, integrated ink viscosity control and dedicated floatation dryer suitable for both water-based or solvent-based inks.
However, the key benefits of the machine demonstrating BOBST capabilities lay with the process critical issues, such as the quality of coating and drying at high speed, paper re-moisturizing and web handling capabilities, especially at the rewinding stage, which is quite complex with siliconized materials.
The coating unit comprised 5 rollers, whose temperature was individually controlled. Available as fixed unit or trolley type, as specified for this machine, it can apply coatings from 0.5 to 4 gr/m2 at very high speed. The 30m floatation dryer included 5 modular sections, with internal ventilation suitable for temperatures up to 250°C (482°F). Two stainless steel moisturizer units also featured 7 zones of adjustable steam flow on both sides of the web.
The line was specified for a production speed of 800 m/min (2625 ft/min) including automatic reel changes at full speed, and has a mechanical speed of 1000 m/min (3281 ft/min). During the machine dry run, visitors were very impressed by the automatic flying-splice at 1000 m/min (3281 ft/min).
The systems for energy recovery in the dryers ventilation and in the automation architecture, connectivity features and readiness for the future of Industry 4.0 were explained and demonstrated on both machines. The other CO 8000 at the show, to be delivered to a leading Chinese film manufacturer, was dedicated to top coating AlOx PET. With a web width of 2500 mm (98.5″), it has a mechanical speed of 400 m/min and production speed of approx. 350 m/min (1148 ft/min).
A BOBST pressurized chamber doctor blade was incorporated offering a wide coating range and, in combination with the metering system, ensures the quality and anchorage of the top coating by minimizing the foam and microbubbles that can form inside the doctor blade. Given the fragile nature of the AlOx, the surface of all the rollers of the machine were specially designed and treated to ensure smooth transportation with no damage to the web surface. The high efficiency floatation dryer, together with the modular fixed coating unit, round up the configuration features.
At the close of the event, satisfaction ran high at Bobst Italia. “We organized an event that could be inspirational for companies looking for solutions that help them make their manufacturing process more efficient, less costly, and increasingly closer to the implementation of the circular-economy concept,” commented Detlef Merklinger. “We look forward to holding other such events and above all to the opportunities provided by the pilot coating line that will be operational as of next year and the further impulse it will give to our technology, joint developments with industry suppliers and the even stronger all-round support to our customers for the development of their business” he concluded.