Consumables
Nazdar aims to make transition to UV-LED ink easy
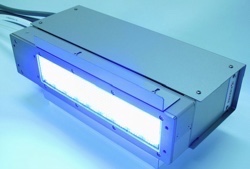
Tuesday 28. April 2015 - On April 13th 2015, an EU ban came into force that prohibits the use of mercury in lighting, causing concern among some in the wide-format print industry that printers using mercury vapour for ink curing will also be affected. While it seems this is not on the cards just yet, the EU's focus on the metal suggests it may be worthwhile looking at the alternatives when choosing new equipment.
Luckily, other curing technology offers more benefits than just escaping the attention of Brussels. LED curing is less energy intensive than mercury vapour, as lamps not only need less power to run but also need much less warm-up and cool-down time and therefore can simply be switched on when needed, rather than left on stand-by throughout working hours. Most machines can be plugged into standard electrical sockets, making installation easier and cheaper, while the cooler LED light source does not produce ozone, a by-product of mercury lamps that required ventilation. LEDs last significantly longer than mercury lamps too – lifetimes can be ten times greater – again saving money, time and maintenance.
Additionally, print companies report shorter drying times for LED-cured output compared to prints completed on mercury vapour machines, and many are finding they can use thinner and more heat-sensitive substrates thanks to lower temperatures, thus reducing material costs. To businesses and customers looking for cheaper, more environmentally friendly products, there are plenty of advantages.
Nazdar has developed a wide range of inks for use with LED-curing technology for digital, screen and narrow web printers. Each are designed as plug-and-play, colour-matched alternatives to OEM inks for specific printer models or series, enabling users to convert to lower-priced, high-quality Nazdar ink with no flushing or other downtime.
For digital printers, Nazdar 260 Series inks are ideal for POS applications using substrates such as reinforced vinyl banner, pressure-sensitive vinyl, styrene, foamboard, coated paper, fluted polypropylene and digital-grade polycarbonate, thanks to excellent adhesion, flexibility and chipping resistance. Designed for use on LED-curing printers at normal conditioned room temperatures, the inks make for a more pleasant working environment while producing prints with consistent, high-intensity colours with low colour-fade.
UV-LED can also be used with screen printing, as Wisconsin’s Empire Screen Printing demonstrated in 2011 with the world’s first UV-LED curing screen press, utilising Phoseon and Kammann equipment and Nazdar inks. The process does not emit harmful ozone nor as much heat as mercury lamps, resulting in a cleaner, cooler environment and prints on thinner materials. According to Empire Screen Printing, it is also possible to retrofit UV-LED kit onto small-format screen presses.
Nazdar 2600 Series, 2300 Series, 2400 Series and UV-LED Air Texture Clear inks are designed to work with LED-curing printers to produce POS and graphics, packaging and textured items. There is an even wider range of UV-LED Flexo inks for narrow web printing, formulated for tag, label and packaging applications.
Nazdar is also happy to work alongside OEM manufacturers who are developing LED-equipped printing systems, taking complete responsibility for the ink aspect of the development to create top-quality ink formulations engineered precisely for the system and its complementary substrates and applications.
Print businesses considering a move to UV-LED inks can also be safe in the knowledge that they have the support of experts, through Nazdar’s Ink Answers support service.