Consumables
Energy savings boost competitiveness of ABB plant in Italy
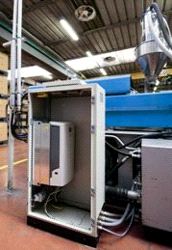
Tuesday 26. August 2008 - ABB is cutting energy consumption in its factories to reduce its environmental impact and save costs. In the second part in our series on the savings achieved at sites around the world, we journey to Italy to discover how a plastic processing plant has used ABB technology to cut the energy used by stamping machines.
The measures taken have cut the electricity bill by $80,000 per year at ABBs Marostica factory in the province of Vicenza, where plastic panels and ducts are made for low-voltage electrical distribution. Savings of 442,000 kilowatt-hours per year were achieved, equivalent to the power used by 116 average households in the European Union.
“Being a plastic processing factory that does not produce highly technological products, we are exposed to aggressive international competition,” said Giuseppe Morini, head of the enclosures business in Italy, “so cutting our energy costs not only helps the environment, but has a remarkable effect on the final cost of our products, improving our overall plant efficiency.”
ABB decided in 2007 to target the 34 presses used for thermoplastic injection, a technique developed in the 1940s that involves squeezing molten plastic into molds and cooling the parts until they solidify. The presses were operated by motors running at full speed that were throttled when output had to be reduced – similar to driving a car keeping one foot on the accelerator, the other stepping on the brake to control speed.
“Our presses were one of the most energy-consuming activities and all had different cycle times and clamping forces ranging from 50 to 2,300 tons,” said David Trombetta, operations manager at the plant. “Several of the presses were also not very modern, so although they worked perfectly well, they were not energy efficient.”
The site turned to ABB expertise, and installed drive technology to control the rotation speed of the motor pumps which activate the press. ABB is the worlds largest maker of electric motors and motor-control devices, technology that can cut the energy consumption of applications using electric motors by as much as 70 percent.
Measuring the savings
In the test phase at Marostica, the system was installed in a way that still enabled the presses to be used in the traditional way, making it easier to compare the data with and without the new technology. Savings of 31 to 51 percent were achieved in the tests, depending on the products produced, and it was decided to equip nine presses with the drives.
Savings of 31 to 51 percent were achieved in tests, depending on the products produced.
“Each press had one or two motors, and for each, an ACS550 drive was installed,” said Trombetta. “This required a total downtime of 1.5 days and the daily production lines were not affected. On top of this, no operators needed any specific training as it did not affect their tasks.”
The system installed comprises a frequency converter (which adapts the motor speed to match the required pressure or flow) as well as a keyboard and display to monitor the operation. The new system allows the needs of the work cycle to be met in real-time and resulted in savings of 35 to 50 percent on the plants press operations.
. “The payback time of the entire investment was only 16 months, and the work environment has improved due to noise reduction because the pumps dont have to work at maximum speed,” Trombetta added.
A number of indirect savings were also achieved, such as a reduction in service costs, in the power required for cooling press oil, and in the power needed to start the machines.
The success of the Marostica facility is now used as a case study at energy efficiency events and seminars around Italy, and has featured in a number of reviews and trade press publications.