Offset Printing
Ready by Day and Night
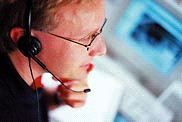
Tuesday 29. April 2008 - Competent customer service via telephone, online and on-site
Even the best product is not immune to trouble. Therefore, printservices offers its customers troubleshooting via TelePresence. Because emergencies call for expertise accompanied by flexible, fast, and individual solutions. More than 70 service bases then take action, round the clock, worldwide.
In a case of urgent need for service, TelePresence enables fast remote and fault diagnosis. This service from printservices offers live support via telephone or signals the local technician to help. In 70 percent of all cases, predominantly electronic faults can be remedied by the press operator himself according to instructions from the specialist, saving complete technician services. In the other cases, troubleshooting by the printservices technicians ensures that production can be resumed within a short time.
Instantly alerted and faster on site
But even if the mechanical system causes a problem and necessitates the presence of a technician, the message system speeds up the action. The Koopmann printing company in Leverkusen, Germany works with ROLAND 700 presses. The last trouble occurred one day at 2:31 a.m., which triggered an automatic emergency call to the service partner. Since no
24-hour service agreement existed, the early service promptly responded at 7:03 a.m. No later than 8:45 a.m., the technician was on the scene with the spare parts. “Without TelePresence we would not have reported the damage before start of operations at 8:00 a.m., and it would have been repaired accordingly later,” summarizes Jens Fischer, Koopmann Operations Director. “The quick support is not only a financial advantage but, above all, it also produces a quality improvement for us.”
Flexible solutions
When an emergency call is received by the service manager responsible for the customer in question, the managers professional competence and quick initiative is called for. He must analyze the situation and if necessary organize parts, technicians and tools – in the fastest way possible. Often, the need is for creative, flexible solutions. When, in July 2007, the presses at a newspaper printing company broke down due to defective drives, committed teamwork was required. At about 1,000 Euros loss per hour of downtime, the waiting time for producing and installing a new drive system would have been unacceptable. It was possible to resume production right after it was briefly outsourced and, 48 hours later, after installation of a temporary solution, adapted to the existing machinery. Concurrently, a subcontractor produced the auxiliary drive required specifically for this purpose in an expensive process within merely three weeks.
Far-sighted maintenance and upgrading
The portfolio of modularly structured ProServ service programs is aimed at proactive and condition-oriented maintenance of the presses in order to avoid major failures from the very beginning. Preventive individual consultancy by the service managers optimizes maintenance of the press and, thus, its availability. For another thing, upgrades and process analyses help to even increase its productivity over the machines life cycle, and to improve overall processes.