Packaging
SACMI presents the Packaging of the future at Propak West Africa 2024
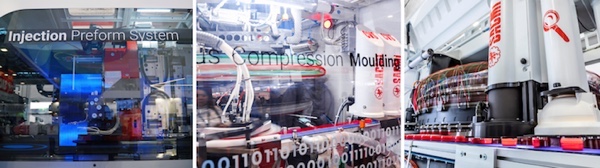
Tuesday 30. July 2024 - Besides its global technological leadership when it comes to offering caps and preforms machines, SACMIs strength lies in its ability to accompany its customers in the transition to new standards, in the direction of competitiveness, quality, and environmental protection.
Versatility, performance and new standards to support an environmentally friendly transition. With all the advantages of a unique interlocutor and the technical and technological support of the Laboratory, certified by the world’s leading brand owners. 10 to 12 September 2024, Landmark Centre, Lagos, Nigeria
SACMI confirms its long-standing presence at Propak West Africa 2024, a key appointment to connect with customers and stakeholders operating in the strategic West African market.
26/22 mm neck-cap transition
SACMI offers the broadest range of solutions for the 26/22 mm neck-cap on the market. Due to its variety of customisation options, this standard is becoming increasingly popular and widespread, while significantly reducing virgin raw material consumption.
Developed for water, CSD, and hot-fill in both tethered and traditional band versions, SACMI solutions meet every production requirement and are certified by leading international brand owners.
All solutions are tested in the SACMI Rigid Packaging Laboratory. This supports customers in identifying the most effective performing solution for specific needs, including design and new product development.
Simple, versatile, future proof
SACMI makes the transition to environmentally friendly packaging easy and profitable. One example is the new tethered standard, mandatory in Europe from 2024, which SACMI has addressed by offering the market an agile and versatile solution such as post-processing bandwidth cutting.
The result is maximum versatility for manufacturers who work with international brands and are therefore interested in exploring the potential of this solution, even where the tethered standard is not yet mandatory.
CCM+IPS: the winning combination
From the product idea to all the technology required to make it, a growing number of customers in Africa are choosing to invest in both the CCM compression moulding machine for caps and the IPS injection moulding machine for preforms.
Taking advantage of a single contact point with a reputation for reliability, such as SACMI (as well as the advantages of new-generation machines in terms of performance, ease of use, and process control) enables a partnership that has become increasingly recognised on international markets, particularly in Africa, with continued growth in existing plants as well as greenfield projects.
Quality control, from product to process
SACMI develops both on-machine and stand-alone integrated vision systems for each machine and process step. In particular, the solution integrated into the IPS preform press, with the PVS156 embedded inspection system, is unique on the market.
Furthermore, the availability of specific CVS systems for each stage evolves quality control from product to process, allowing these systems to be installed on existing plants as well.
Service excellence
SACMI has constantly invested in improving customer service. In fact, it features offices and branches spread across the continent, supported by the Italian parent company.
Customer support from the earliest stages of the job order and throughout the life of the machines as well as plants – together with the technical support of the Laboratory – are the trump cards of the SACMI product and service. All this guarantees top, worry-free production.