Packaging
SACMI – Mould making for customisable (and flexible) packaging
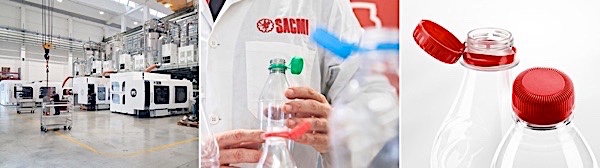
Saturday 30. March 2024 - Versatile. efficient and sustainable size changeover. These are the three main drivers of the rigid packaging market. From mould design to machines, SACMI offers an all-round service, providing the latest technology and support, from product conception to after-sales.
Versatility in packaging production is one of the key market requirements. SACMI offers a full range of mould making and machine engineering services with technological advantages, as well as comprehensive customer support services, from the initial product design to after-sales service
The main market drivers
The customisation of food and beverage packaging is driven by the need to segment the offer according to different criteria: cost, sustainability and market target. With over 60% of the market, SACMI is the leading supplier of machines for the production of flat-top caps.
One of the main drivers is the strong need for versatility, while maintaining a high level of plant efficiency and availability. Regulatory developments – such as the introduction of the tethered standard in Europe – have an impact on consumer experience, further accelerating the trend towards the segmentation of the offer.
In the flat-top plastic cap market in particular, there is an increasing demand for customisation by embossing or engraving the underside of the closure, rather than printing it.
With this in mind, SACMI’s value proposition includes the enormous inherent advantage of compression machines, where the bottom plate can be changed extremely quickly and easily. This increases machine uptime and reduces the complexity / skills required for mould changeovers. In addition, SACMI has a department dedicated to the production, testing and inspection of moulds, with advanced instrumentation and a specialised team.
The moulds
In SACMI’s light machine tools department – an area of about 4,000 square metres, within the 270,000 square metre production area at the Group’s headquarters in Imola – moulds are produced and inspected in a controlled environment (constant temperature and humidity), using state-of-the-art machine tools and top quality raw materials purchased by SACMI from the world’s most prestigious suppliers.
Heat and thermo-chemical treatments play a crucial role in mould production, which is why SACMI integrates them in-home into its own mould production process.
In 2023 alone, SACMI’s mould making department tested more than 65,000 components that were produced. The extremely high precision machining and the expertise of over 100 skilled workers, together with R&D design and assembly, have enabled us to achieve a compliance rate of over 99%.
SACMI’s “unique selling proposal”. The 26/22 mm neck transition
SACMI develops complete production solutions specifically for the 26/22 mm neck range, including machines, moulds and technology for the production of both preforms and caps. Comprehensive support ensures that customers can migrate successfully to new standards that deliver benefits both in terms of the environment and consumer experience.
When it comes to caps, SACMI offers the widest range on the market for this new type of neck, which has been developed, tested and certified by the laboratory, including extensive tests on the performance, tightness, and ease of opening of the cap-preform system. In addition to the CCM, the downstream technology offer includes the IPS and the supply of complete bottling lines, with Computer Vision systems for each stage of the process and a complete packaging design service.
For more than a century, SACMI’s “Unique Selling Proposal” has been a partnership that goes beyond the sales-purchase concept to include the ability to interpret the needs of the customer:
Assistance in the technological definition of packaging, thanks to our Technological Laboratory accredited and certified by the world’s leading brand owners
Providing state-of-the-art production solutions designed and manufactured in-house, including machinery, moulds and quality and process control.
Providing support throughout the life cycle of the plant through digital (SACMI Smart Care) and on-site services, thanks to a network of more than 70 companies in 26 countries worldwide.