Packaging
Drink Japan, four good (technological) reasons to choose SACMI
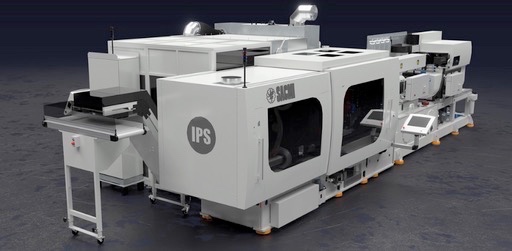
Monday 11. December 2023 - Innovation by SACMI Rigid Packaging Technologies to play a pivotal role from 6 to 8 December 2023. An ever-wider range - from caps, preforms and containers to post-processing - with an ever-sharper focus on sustainability
While, on 11th December 1997, world leaders were in Kyoto to sign the first global climate protocol, SACMI was working on the technologies of the future: technologies that would lead to the establishment of a new international standard, reducing plastic cap weight by more than 50% and providing benefits for both the environment and companies’ competitiveness.
From 6 to 8 December 2023, the main innovations developed by SACMI’s Rigid Packaging Technologies Division – for caps and preforms, yet also containers and post-processing – will be on show at Drink Japan (Tokyo Big Sight, Japan), on a stand co-organized with Correns, SACMI’s in-country agent.
Continuous Compression Molding, SACMI leads the closures sector towards a 4.0 future
Over 2,000 caps per minute, comprehensive quality control of every single cap, the ability to produce lighter, higher-performance caps that can meet future market needs: this is the CCM range with which SACMI has set a new benchmark in the Plastic closure manufacturing sector. Following the addition of new features and controls, the CCM range is leading the closures sector into the Industry 4.0 era by letting manufacturers manage machines and processes proactively and predictively.
Injection Preform System (IPS), the 3Rs approach
SACMI is unique in that it acts as a sole provider, covering every stage of the process. That’s why the company developed a complete range of machines – the IPS series – to meet all the production needs of both bottlers and converters. Two innovations have been applied in the field: firstly, intense development work on the machine means it can now handle up to 100% rPET and up to 50% PET in flake form; secondly, process control has been incorporated directly into the press – the first solution of its kind on the market – with the PVS156, the exclusive system developed by SACMI Computer Vision Systems to complete its in-line and stand-alone PVS range for preform quality control.
Post Processing Solutions – An easy way towards tethered
With the Group now strengthened by the arrival of Velomat, SACMI has expanded its post-processing range. On the one hand it has developed complex cap assembly solutions – of great interest to the home & personal care sector and, on the other, invested in the machines that slit and fold the anti-tamper band, resulting in an efficient, economical solution that lets producers adapt to the new tethered standard.
SACMI Lab, an integrated approach to cap-closure design
At SACMI, what makes the difference is not just the outstanding technology but the close teamwork with the Laboratory, where new standards are co-developed with customers in a way that focuses on integrated cap-container design.
SACMI has also succeeded in transferring the advantages of its world-beating compression molding technology to other sectors, such as container manufacturing (SACMI Compression Blow Forming). Moreover, each solution is accompanied by the development of dedicated vision systems (SACMI Control Vision Systems) that use cutting-edge AI algorithms.
Alongside the Laboratory, SACMI provides outstanding assistance and service through synergies with its Global Network. What’s more, it has a network of local agents and technicians ready to provide customers with assistance 24/7 so that they always get the very best from SACMI technology.