Finishing & Screen Printing
Grigeo Packaging builds great success on BOBST corrugated production lines
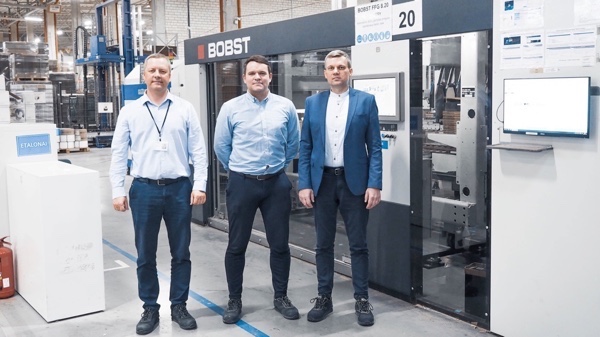
Wednesday 25. January 2023 - One of the Balticss largest paper and wood pulp manufacturers, Grigeo Group has relied on BOBST technology for over 45 years. The company continues to invest heavily with BOBST as part of its strategic plan for the long-term future of its corrugated packaging production operation.
A founding member of the Lithuanian paper industry tracing its roots back to 1823, the Grigeo AB Group of Companies manufactures a vast array of tissue paper, container- and honeycomb board, corrugated, and fibreboard products. The Group consists of Grigeo AB, Grigeo Packaging UAB, Grigeo Klaipèda AB, Grigeo Baltwood UAB, Grigeo Recycling UAB – all located in Lithuania, along with Mean Pak AT, in Ukraine.
Over the past 10-12 years, a sharp increase in investment has laid the foundation for advancing and expanding the corrugated specialist division, Grigeo Packaging. In 2012, a new industrial facility with new corrugated cardboard manufacturing and processing lines were put into production to accelerate output. Since 2016, four BOBST machines have been bought to ensure the high quality of the products and add value for customers. As a result of these investments, the company has grown significantly as witnessed by the huge increase in production volume, which went up by more than 15 times between 2009 and 2021.
“Our first BOBST machines, which have served us well for several decades, are still going strong, so when we embarked on this investment program, we knew where to turn. We always need top efficient machines with the highest productivity and quality, and we chose BOBST because they are a trusted supplier and their machinery is regarded as the best in the industry,” said Managing Director Otonas Valiuis, who joined the company in 2005.
Moving to inline box production
The first step in the ambitious plan was to invest in a BOBST FFG DISCOVERY 8.20 flexo folder gluer in 2016, which was installed to expand the application range. This was supported by a new automatic supply of sheets, carton binding, and semi-automated palletizing equipment to ensure maximum production efficiency. The user-friendly FFG is a high productivity machine that allows speeds of up to 18,000 boxes/hr and a very high consistency in production to reduce ownership costs.
“BOBST FFG DISCOVERY 8.20 has more than lived up to our expectation both by almost doubling our capacity and by allowing us to add new solutions to our product line to answer market demands,” stated Technical Director Modestas Skierus, who joined the company with a degree in mechanical engineering in 2012.
In 2018, Grigeo Packaging added a BOBST EXPERTCUT 1.6 PR Autoplaten die-cutter and a FLEXO 160-2 VISION In-line press to the production floor to further grow the business with high quality packaging. Then just last year, a BREAKER 2 Flat Track blank separator for automatically forming complex layers ready for palletization was added to the equation to secure the final product quality.
The EXPERTCUT 1.6 PR delivers optimum accuracy, consistency and high productivity with changeovers of less than eight minutes. Grigeo specified the machine with optional POWER REGISTER for integrated perfect print-to-cut sheet registration, a feature that ensures waste is kept very low. The die-cutter runs in line with the FLEXO 160-VISION press which is a cost-effective and versatile post-print press for producing multiple types of corrugated packaging very easily.
Together the two machines offer automated single pass box production, a set up that replaced two separate operations to save vast amounts of time in production, according to Mr Skierus, who said, “We exchanged two older pieces of equipment with this inline BOBST configuration, and as a result we have a highly efficient, high quality box production line in our factory. This has given us a whole new level of output which is supporting our growth strategy and it will help secure our position as one of the leading packaging producers in the country.”
Staying competitive with BOBST
As the corrugated market keeps growing with demands for shorter lead times, higher quality boxes and less waste increasing, packaging producers must weigh up their options and invest wisely to stay ahead of the game. BOBST is leading innovation for the industry to allow pioneers, such as Grigeo Packaging, to do just that.
To support the investments, the Lithuanian packaging company has signed up to a BOBST flexible Pick&Pay parts storage system for easy retrieval of spare and worn parts, which comes with regular refills, making parts available around the clock if needed. In addition, further training for operators and maintenance staff in the form of technical coaching days is ensuring operations remain at optimum level.
“We have spent more than 25mio since 2008 on the expansion of our production capacity, and on storage and office space,” concluded Director of Technology and Project Management Giedrius Valdemaras, who has been with Grigeo for nearly 18 years. “Our BOBST machines have enabled us to make a high increase in production capacity, so we can respond faster to our customers with just-in-time delivery of the best quality boxes. With BOBST we get the whole package so to speak – highly efficient machines and good quality, as well as excellent support, service and quality training.”
Marco Lideo, Head of the DSF-LLAM product line, commented, “The Grigeo success story is a great example of the many long-lasting partnerships that BOBST has forged, and of how BOBST machines are quietly working away, in so many cases for decades, all over the world. Longevity, coupled with high quality, is the differentiator for both our companies and it is the longevity of the BOBST machines that will ensure Grigeos future as the leader in their market.”