Finishing & Screen Printing
With the new BOBST EXPERTCUT 106-LER die-cutter, we can produce even more
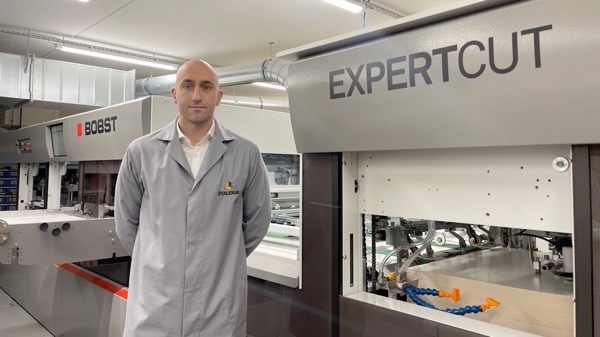
Friday 23. December 2022 - The company has been successfully operating for 32 years, developing its expertise in cardboard packaging for the pharmaceutical industry. Today, the company is home to 127 employees, producing around 350 million boxes - or about 11 thousand orders - annually.
The talekar printing house from Slovenia needs no introduction. A graphic packaging company, it is most recognisable for its cardboard packaging products and services. It has been successfully operating for 32 years, developing its expertise in cardboard packaging for the pharmaceutical industry. Today, the company is home to 127 employees, producing around 350 million boxes – or about 11 thousand orders – annually.
The company responds quickly to market trends, focusing on using production equipment and raw materials from top manufacturers. One such manufacturer is BOBST. Following talekars investment in a new EXPERTCUT 106 LER, CEO Mr Matic talekar welcomed us to his office for a discussion about his companys long-standing relationship with BOBST.
As he told us, his companys collaboration with BOBST has been ongoing for more than 20 years. He started with several B2 format machines, before adding the BOBST VISIONFOIL 104 hot foil stamper, and a number of folder-gluers. Today, it has four BOBST folder-gluers in operation; one MISTRAL and three EXPERTFOLD series, that boast all the features and technology the pharmaceutical industry requires.
What was the main reason for investing in the new die-cutter?
We felt that the die-cutters we owned were no longer able to meet our production requirements in terms of speed and productivity. Also, as we saw a significant increase in print runs, we were looking for a high productivity machine that can meet all the needs of our clients, even on short print runs. The new machine gives us much-improved productivity thanks to fast, uninterrupted production and short set-up times. This has opened up many new opportunities for us. For example, until now, hot foil was not our focus at all. It made up about 7-8% of our volume, but with our newly increased capacity, we can strengthen this part of our product offer.
What characteristics did you look for in a machine and what made you choose BOBST EXPERTCUT 106 LER?
High productivity, short start-up time, and the machine format were most important to us. All in all, it was important for us to have a fast machine that we can rely on, to provide us with safety, quality, and consistency, which is very important for the pharmaceutical industry. This is a machine fully prepared to work in Industry 4.0 and you can tell BOBST worked hard on it. For example, it has a tooling option, which means that it is possible to use a smart tool that will communicate with the machine, providing operators with all the necessary data and remembering settings. All technology is moving in that direction.
Of course, we also considered the fact that the machines we already had were from BOBST. Service, spare parts, and BOBSTs record of great customer service were also important to us, and our operators are already used to working with this technology.
Lateral register working in accordance to printing marks makes the biggest difference. It uses a lateral camera to identify the printing marks and automatically aligns each sheet. We choose an elevated machine, which means that we stock up pallets for clients with larger runs. The speed of the model we took goes up to 9000 sheets/h and can run for sustained periods at that speed comfortably.
How long does start-up of the machine take? How many jobs can you do on average in a day?
The time required for start-up depends on whether a job requires a completely fresh setup, whether it needs blanking, or whether it is a repeated order. If it is a completely new order, it takes about an hour, if blanking is used it is about 1 hour and 40 minutes, and in the case of a repeated order, about 15 minutes.
Regarding the number of jobs that can be done in one day, our planning service looks to combine jobs whenever possible. We can combine jobs if they are printing with the same colors, the same dimensions, or the same tools. If everything goes well, it is possible to make five to six work orders in eight hours.
How did the installation go? How long did it take you to get the machine up and running?
I should point out that this was a full pandemic-era installation. Everything was arranged online. At the beginning of 2021, we signed the contract, and in five months the machine was delivered. It was a time when delivery times were still short.
The installation went great. It took us about two weeks before it was ready to be put it into production. Training for operators took 10 days. Considering that we have been working with BOBST technology for a long time, our operators know the principles of how operate the machines. The new die-cutter comes with even more automation features, which only makes it even easier to use, even though the machine itself is already extremely user friendly. Today, we have one person working on the machine per shift, and we have a total of five operators trained to work on the machine.
What are your plans in terms of new investments and developments?
Next year we plan to invest in a new offset printing machine. In recent years, we have been closely monitoring digital printing technology and with a view to moving in that direction as well. This technology would open a lot of new possibilities for us, and we have already carried out tests to see how feasible it would be for us.
We plan to focus more strongly on exports, which take up about 55% of our production volume. Today, in addition to the Slovenian market, we also have a presence in an increasing number of foreign markets, and we plan to further strengthen that. We are still competitive on flexibility and quality.