Consumables
Special requirements demand special solutions – Marbach supplies special tools for medical technology
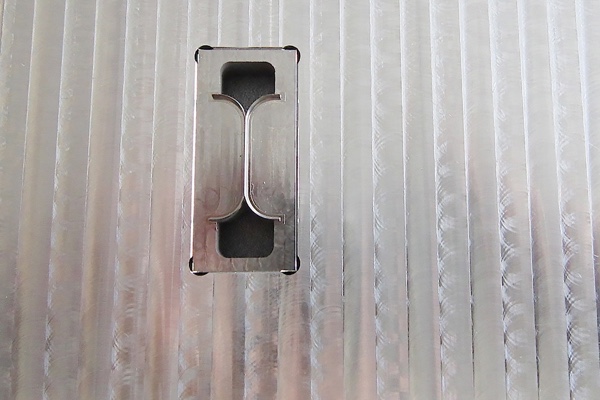
Thursday 07. April 2022 - The globally operating diemaker Marbach is known for its requirement-oriented solutions. For applications in medical technology, Marbach has special tools in its portfolio which have been designed specifically for this purpose.
The demands on cutting-dies for medical technology are very diverse: Not only precision plays a significant role. Topics such as hygiene and clean room also indicate how demanding the requirements in the medical sector are.
Michael Kiesel, Sales Manager at Marbach: “Our special tools for medical technology are used in many different applications, producing active substance patches, tablet blisters, surgical accessories, labels or outer packaging for moist plasters. These are all areas where hygiene and precision are essential.”
Marbach uses tools with solid steel parts, wire-eroded base plates or PMMA tools for medical technology. In some cases, several technologies are combined. This always depends on the specific customer requirements. As Marbach has an internal metalworking department with its own tool manufacturing, machining techniques such as milling, eroding, coordinate grinding and round machining can be carried out quickly and flexibly.
With decades of experience in the cutting-die production for medical technology, Marbach possesses extensive know-how. For example, special measuring methods are used to calculate the correct active substance area for active substance patches and to produce the tool in exactly the right size. Marbach measures the produced tools, optimizes them and, if required, makes sample die-cuts with the customer’s material. This ensures that customers receive their tool in the optimal design and ready-to-use. Speedy sampling is also possible at Marbach.
Kiesel continues: “Compared to conventional rotary or fully milled tools, our tools for medical technology can be delivered very quickly and meet the highest hygienic requirements. In terms of direct price comparison, our solutions are also unbeatable. An additional advantage of our tools is that they are very durable. Blades can be replaced several times, and revision can be carried out quickly and reliably. This is an optimal solution for our customers, because with a new tool, a complete validation is necessary, which is time-consuming and costly. With a reworked tool, this complete validation is not necessary and a short inspection is sufficient.”