Consumables
Embossing for strong-selling packaging at the POS. Marbach offers extensive embossing portfolio
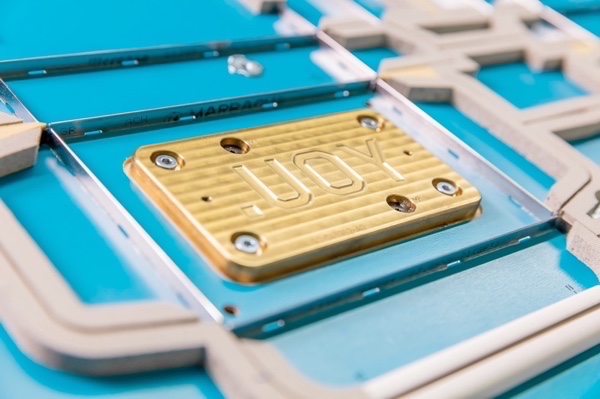
Friday 18. February 2022 - The globally active diemaker Marbach holds an extensive portfolio of different embossing technologies available for its customers. This enables them to meet the constantly increasing demands for strong-selling packaging at the point of sale.
Bernhard Reisser, industry manager folding carton at Marbach: “In recent years, we have observed the trend that the packaging designs requested by our customers are becoming more and more complex. As a die manufacturer, we of course keep up-to-date with this trend. We have therefore, various embossing solutions on hand for our customers for ensuring sales-boosting packaging at the POS.”
Embossing as a finishing technique is mainly used for high-end consumer goods, confectionery and cosmetics packaging. There are many different factors to consider when embossing paperboard. Their selection and combination depends primarily on the material to be embossed, the packaging layout, and the visual requirements of the packaging.
In addition to the two types of embossing, embossing and debossing, a distinction is made between 2D and 3D embossing. With embossing, the cardboard surface is raised, with debossing it is recessed. 2D embossing is embossing on an embossing plane. Its edges appear angular, and can be used with many embossing patterns. Sharply defined edges make it very suitable for embossing small texts and details. 3D embossing, on the other hand, is carried out in several stages, so that the embossing takes place on several levels. This makes it appear more three-dimensional, and its edges appear rounder than those of 2D embossing. For this reason, it is less suitable for small texts and details, but is mainly used for larger embossing areas. 3D embossing optimally enhances the effect of the printed image. It ensures unique embossing results and is used above all for high-quality luxury goods.
Hotfoiling is another option for packaging finishing. Heat is involved in this type of embossing: a heated hot foil tool transfers foil onto a paperboard sheet under high pressure. This form of finishing ensures matchless results.
A combination of embossing and hotfoiling is often used, especially for high-end packaging where there are particularly high demands on packaging finishing.
Reisser: “We have the advantage of being a full-range supplier: We supply embossing and cutting-die tools from a single source. This means we can offer our customers the right embossing solution for every requirement. Of course, it is always important with embossing that the embossing perfectly matches the print image. Here we have special solutions for our customers -for both embossing and hotfoiling -which not only ensure that the register is perfect, but also that make-ready times are as short as possible. For flawless packaging at the point of sale and maximum performance in embossing.”