Finishing & Screen Printing
Cameron Balloons digitises and automates textile cutting
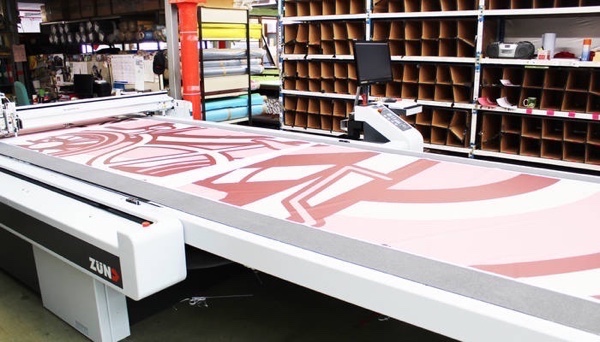
Thursday 09. September 2021 - The Bristol, UK-based company, founded by Don Cameron in 1971, manufactures hot air balloons. In the early days of the companys history, Cameron started the production of hot air balloons in the basement of his house.
Cameron Balloons has revolutionised its manufacturing process by investing in a Zünd Cutter G3 L-2500.
In 1983, Cameron Balloons moved to its current location. The business is spread over three floors. Most of the factory space is used to lay out huge sheets of colourful fabric, which are then cut and sewn together by skilled staff. In 1989, the company received royal recognition with the Queen’s Award for Export. In 2000, it was awarded the Prince Philip’s Designers Prize for excellence in design for business and society.
The company manufactures hot air balloons in all materials, sizes, shapes and types. Most of the special shape balloons are produced for commercial advertising, but some are also purchased by private individuals, for example by the now late publisher Malcolm Forbes. His order included about a dozen balloons in special shapes such as Harley Davidson motorbike, sphinx, Beethoven bust, French chateau, pagoda and minaret. The company also produces airships or helium balloons. It has been involved in national and international world records for balloon flight, including the fastest round-the-world flight, as well as the highest and the longest flight in the world.
Nick Purvis, Sales Director at Cameron Balloons explains, “Every one of our hot air balloons is manufactured to the strict standards of the UK Civil Aviation Authority and we have to adhere to the same rigorous procedures as any other aviation company.” Cameron Balloons is one of the world’s leading suppliers in the market with more than 9,500 hot air balloons delivered internationally. Nick Purvis reports, “The company has grown tremendously. We started with just a few employees who cut and sewed the balloon fabric together by hand back then. Today we employ around 50 people who operate innovative machines for production. We have invested more in technology over the years to make our manufacturing processes efficient.”
The hot air balloons are made from a very finely woven nylon that weighs 35 to 100g/m2. The lightweight material is usually cut into symmetrical pieces in the shape of boats. The many kilometres of fabric required to make a balloon are then sewn together by skilled personnel. Nick Purvis explains, “Each hot air balloon is made to our customers’ exact requirements, with an average turnaround time of 10 to 30 weeks, depending on how complex the graphic elements and shape of the balloon are.”
Cameron Balloons has relied on Zünd digital cutting technology for more than 20 years to cut the different fabrics for each panel. Nick Purvis adds, “We do most of the cutting work with Zünd’s Driven Rotary Tool DRT. The Zünd Cutter is also perfect for cutting graphic elements or letters for the hot air balloon branding.” On the versatile Zünd Cutter, Cameron Balloons also uses the MAM marking module to label the individual panels.
This is now the third time the company has invested in digital cutting technology from Zünd. The company purchased its first Zünd cutter in the early nineties to plot patterns and cut fabric panels. Nick Purvis: “Our latest acquisition is the Zünd G3 L-2500 cutter, which has revolutionised our manufacturing process. When selecting accessories, we chose the Integrated Compact Colour camera (ICC) to automate the process with our Durst printer. The benefits that have resulted have exceeded our expectations. Previously, after printing with the Durst printer, we had to manually cut the material before it could be transferred to the Zünd cutter. Thanks to the ICC camera, the cutter can now detect registration marks and material edges and cut the material precisely. The Zünd technology and the Durst printer work perfectly together.” The printed material is now transferred directly to the cutter. Nick concludes, “Since adding the ICC camera to the Zünd G3 cutter, we have been able to achieve maximum efficiency and precision. We now save around 4% material every year.”