Finishing & Screen Printing
BOBST VISIONCUT 106 and High Performance Tooling boost Kroonpresss packaging offer
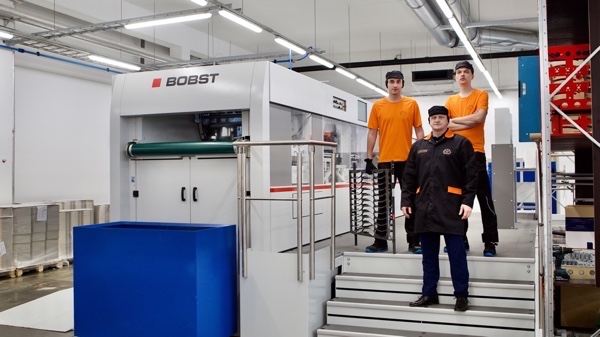
Tuesday 13. July 2021 - Kroonpress knew they were entering a highly competitive industry and to succeed, they would have to stand out from the crowd. We decided from the start to differentiate ourselves through quality and versatility, said Mr Margus ürike, Packaging Division Manager at Kroonpress.
In a rapidly changing world, the ability of companies to adapt and evolve has never been more important. Kroonpress is a great example of doing it very well.
Since 1990, the company has established itself as the leading offset print plant in Estonia, focusing on newspaper and magazine printing. But with demand for paper newspapers on the decline, the company knew it had to evolve, and in 2020 it established its own packaging division, which trades under the name of Box & Bag.
“We could see that our customers requirements, both domestically and across the rest of the Baltic countries and Scandinavia, would be quite varied, but with quality as a consistent requirement. To achieve the flexibility and exceptional quality that we needed, we had to be willing to invest in the best equipment available. And for that, we knew we had to go BOBST.”
A high-performance die-cutter
Kroonpress needed a die-cutter and selected the VISIONCUT 106 LER 3.0 AUTOPLATEN PRESS from BOBST. VISIONCUT 106 is associated with high levels of automation for more uptime, increased precision and reduced workload, while job repetitions are simple, quick and accurate. Installation was straightforward and the operators received training from BOBST on its HMI and software capabilities. Importantly for Kroonpress, customization, versioning and personalization are all made easy with the machine. Normally, as die-cutter versatility increases, so productivity drops off, but with VISIONCUT 106 there is no compromise. “When your clients need you to meet very specific product challenges at short notice, having the right equipment to get the job done is very important,” said ?ürike. “Not only do we now have the VISIONCUT 106, but we know we now also have access to High Performance Tooling, and we have already discovered the competitive advantage it provides.”
and High Performance Tooling
To ensure an optimal and consistent production performance of their die-cutters, converters need high-quality, premium cutting tools. Without high-quality tools, production losses of up to 20 percent may sometimes be taken into account. BOBST has recognized this potential for process optimization and has pioneered High Performance Tooling. With High Performance Tooling, BOBST aims to create a standard for certified die-makers to produce dies in accordance with the highest expectations, based on best practices and proven know-how. BOBST has even pioneered a special certification program for die-makers, which allows them to provide optimal cutting, stripping and blanking tools to their customers.
As part of the BOBST commitment to High Performance Tooling, every BOBST blanking machine is now delivered with a set of tooling specifically made for one of the converters most common layouts. This was the case for Kroonpress. A set of High Performance Tooling was offered with the purchase of the VISIONCUT 106. The tooling was made for a very complex layout, and was made by one of the leading certified die-makers, Karel Ka?àk s.r.o in the Czech Republic.
The results for Kroonpress were impressive. “Despite the very difficult layout of the tooling, the machine could still run at excellent speeds,” said ?ürike. “Our hope was that it could run at 6,000 sheets per hour with this complicated tooling setup, but the results surpassed our expectations and the machine ran at 7,000 sheets per hour. This was a big positive surprise to us all, not least to the customer, who received a high-quality product earlier than expected.” Now Kroonpress has packaging clients across several varied sectors, including food, consumer products, pharmaceuticals and cosmetics, and is well established for the future. “We feel that we have established ourselves in the packaging industry and already have a reputation for high quality,” said ?ürike. “The VISIONCUT 106 has been central in helping us to achieve this.”