Prepress
Moquin Press Finds Early Success with Heidelbergs Prinect Business Manager
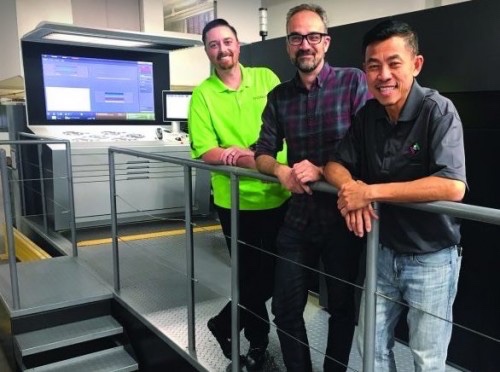
Monday 22. July 2019 - Only a few months after installation, Moquin Press, located in Belmont, California, is already seeing increased speed, higher employee satisfaction, and better client communication thanks to Heidelbergs Prinect Business Manager. The MIS system integrates Moquins entire business process, production, analytic and customer information into a smart print shop workflow.
Prinect Business Manager: The Capabilities to Take Moquin Press to the Next Level
“We faced a lot of challenges with our old software, but one of the challenges that really stood out was that we needed several people in several different departments tracking a job. There was too much manual notetaking and human intervention that it really impacted our efficiency, and we werent able to get as many jobs completed as we wanted,” said Greg Moquin, President of Moquin Press.
With Prinect Business Manager, Moquin is able to reshape the workflows in their print shop. With processes no longer controlled manually, Moquin Press is able to reduce touchpoints while also using its time, machines, and material more efficiently with zero defects, less waste, and reduced warehousing. Whether dealing with price requests, orders or printing approvals, Prinect Business Manager assists Moquin Press in defining the optimal production method thanks to the close integration of costing and production. By taking their current utilization of production capacity into consideration, the company is also able to dynamically adjust customer prices.
According to Moquin, “The most beneficial aspect of Prinect Business Manager is the integration of the whole company. The estimate takes the most time, but we were able to cut that time tremendously with Prinect Business Manager. A small quote would usually take us about 5 minutes before, but now takes us about 1 minute. A large packaging job that would previously take us half-a-day to one day now only takes 30-45 minutes.”
With Prinect Business Manager, Moquin Press has all of the information they need recorded centrally and continuously whether its administration or production information. Prinect Business Manager also integrates Moquins customers directly into the system which allows them to order, upload documents, make changes or approvals, and check status updates.
“Were still just starting out with all the capabilities of Prinect Business Manager,” said Moquin. “But we are really excited to dive further into the capabilities and take our company to the next level.”
Increased Quality and Efficiency
One of the deciding factors in switching over to the Prinect Business Manager was Moquin Presss great success with the Speedmaster XL 105 and XL 106. The Speedmaster XL 106-6+L was the first machine installed in the U.S. with Push to Stop technology, which is still impressing Moquin two years after it was initially installed. “Push to Stop” technology enables all jobs to be autonomously changed over without operator intervention and will continue to print until the operator interrupts it. This software system reduces the number of operating steps during a job change and enables all operators to achieve uniform results.
“Thanks to Push to Stop technology, we have been way more competitive in the market and are more efficient jumping from job-to-job,” said Moquin. “Well schedule a job for 3 hours and often are finishing that job in an hour and a half. Its just amazing technology, and its paid off tremendously for us.”
In order to allow Moquin to expand even further into the packaging and pharmaceutical realm, the XL 106 is also equipped with Inpress Control 2 and Inspection Control 2 for exceptional quality control. With Prinect Inpress Control 2 on the press, the Speedmaster can handle even the most complex job changes at the fastest speeds possible. With this technology on the press, the Speedmaster XL 106 delivers the first measurable result in less than 60 sheets, and the run is ready to start in less than 1 minute.
At the same time, Inspection Control 2 compares the content of an entire printed sheet with the job PDF, and subsequently verifies it against an OK printed sheet. Any errors on the run are flagged in the delivery pile, and the printer is notified. According to Moquin, “Since weve installed this technology, weve gained new clients because we have the ability to report on every job we print to show them the issue, where the issue is, and how many sheets were affected by that issue. If there is a blemish, it will show it, and its taking our quality and efficiency to the next level.”