Finishing & Screen Printing
Bobst Group reflects on a transformative 2018 and reveals its key focuses for the year ahead
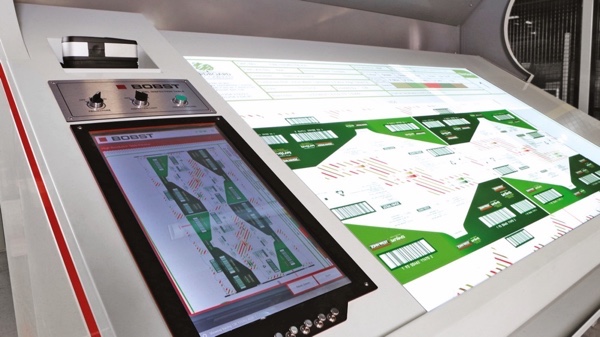
Wednesday 19. December 2018 - As we reach the end of 2018, we take a short look back at the year and some of the major trends and customer feedback on our product portfolio and look forward to our expectations for the year ahead.
A noticeable trend throughout 2018 was the consistent feedback from our clients that the role of packaging is changing. While protecting the goods is still the number one priority, it needs to be done in a more sustainable way. There is also greater demand to process thinner materials and to propose digitalized machines. With the rapid expansion of e-commerce, our customers packaging production requires more productive and more flexible machines without compromising on quality. As brand owners use packaging to stand out on the shelf and to appeal to customers, the demand for better color control, shorter production runs and repeat orders is growing, putting more pressure on converters to automate packaging production.
Sheet-fed business unit
In 2018, the sheet-fed business unit continued to benefit from leading innovations. The new MASTERFLUTE Touch inline laminators – with one single interface to pilot the whole machine delivering the highest productivity – have been a great success. The NOVACUT 106 ER and EXPERTCUT 106 PER remained in high demand as recognized heavyweights in the industry, delivering leading quality and optimal price performance. These have been a perfect fit for converters who are seeking to industrialize production. The EXPERTFOLD 50-110 has been a best seller in 2018, particularly within the pharmaceuticals and cosmetic sectors. The recently introduced SPEEDWAVE 2 was also very successful, as customers recognized its ability to enable higher productivity levels. The new PREMIUM GAP CONTROL system on FFG – recipient of the FEFCO 2017 Gold Award for Best Innovation – is receiving fantastic customer feedback as an enabler of optimal productivity.
e-commerce was a key word in 2018 and the specialty folder gluer MASTERFOLD 230, with GYROBOX XL, has been a major success enabling fast running speeds, fully automatic setting and extreme configurability. For converters aiming for zero-fault packaging production, the recently launched ACCUCHECK 2 and NOVACUT 106 E 3.0 and SAMPLING device gained significant interest.
From a printing standpoint, BOBST, with a series of industry supplier partners, has delivered a quantum leap in the flexo print process with the THQ FlexoCloud , helping corrugated box manufacturers achieve some exceptional results, not only in print quality, but security print as well.
For 2019, the Sheet-fed business unit expects zero-fault packaging to become mandatory and a continuous growth of e-commerce packaging. The demand for an extended color gamut and high quality printing for corrugated boards will further accelerate. Finally, the pressure from brand owners to reduce non-recyclable packaging will grow.
Web-fed business unit
In 2018, the Web-fed business unit continued with significant success in gravure printing, especially the RS 6003. This machine is associated with excellent performance and flexibility to adapt to multiple applications and product configurations, covering a wide range of customer needs. The RS 5002, because of its optimized price/performance ratio in the flexible packaging applications, fulfilled demand from emerging markets. We opened new facilities in China in 2018, answering the growing demand for packaging production in the region.
CI flexo printing made a major step forward in 2018 launching the new 20SEVEN CI flexo press featuring new technologies for further enhanced process consistency. The 20SEVEN is a spot-on solution for the ECG printing process.
Demand has continued to grow for substrate processing, and the K5 EXPERT is one of the best sellers in this area due to its many unique innovations, including the 700mm diameter coating drum. The K5 VISION has been selling well for the converter market due to its flexibility in handling a variety of substrates. It is also important to mention that brand owners are increasingly moving to recyclable film, creating growing demand for AluBond and AIOx. The popularity of AluBond is due to its adhesion properties and its enhanced barrier properties on BOPP and CPP films.
In terms of lamination, the CL 850 is the best seller, because of the quality of the performances of this machine when combining it with the Flexo BOBST trolley.
For printing, BOBST labels and flexible packaging solutions had a great presence at international shows such as Labelexpo Americas. The M5 was the best seller because of its flexibility and great variety of materials. Its on-boarded automation has also been widely praised. The REVO technology, which enabled the digital control of labels and packaging production, is poised for major growth as it combines key brand requirements – high quality control and high productivity, combined with the ability to manage short runs and low operation costs.
Looking ahead to 2019, the Web-fed business unit will focus on strong growth in gravure in Europe and Asia. Labels production will continue to evolve driven by the digitalization of the entire production process, including in-line color control. In Asia, we expect significant transition from gravure into flexo, especially in fast-growing markets like India and South East Asia.
Services business units
While the machines are always of great interest, the BOBST business unit for services had a great year as well, as customers increasingly emphasize the need for value-adding services.
The new Digital Inspection Table – a digitalized way to proof printed sheets and die-cut blanks – is a product that all printers and converters should consider. It streamlines the process, improves precision and reduces errors, saving time and costs.
The opening of the new Distribution Center for spare parts in Indianapolis, US, and the hiring of 100 new Field Service Technicians across the globe, will further increase the service level for our customers.
In 2019, services will play a growing role for converters and printers. They will witness an increase of connected services to support improved productivity, higher machine availability and higher production quality.
Within services, tooling is a new way to improve machine performance with the certification of diemakers. The program will gain importance and make packaging production more efficient. Finally, the development of the portfolio of expert services and consultancy will be built towards a Process Optimization program, which is required in a changing world where automation and process optimizations are key priorities.
Mouvent – BOBST digital printing
In 2018, Mouvent – the competence center for digital printing for Bobst Group – stabilized and industrialized its core cluster technology. The beta installations for textile and label printing took place and the number of installed textile machines reached six units. The first customer installations of Mouvent label machines also took place. We believe this is the start of a fundamental change in the industry in terms of how labels are produces in a fast changing world, where on-demand and customization are daily requirements
Development on further products has advanced well and additional products are about to be launched next year, which will widen the product portfolio of packaging solutions
And tomorrow
? Digitalize, automate, connect.
BOBST will continue with its “Leading Innovation” focus. In 2019, the demand for more flexibility in the supply chain and shorter turnaround times will continue to put pressure on printers and converters. The need for consistently high quality printing, not only within a batch, but across multiple reprints, will be higher on the agenda. Stronger regulations in areas of consumer safety, waste disposal, nutrition facts and many others will have a significant impact on the packaging industries. Ink formulation will accelerate its move towards water-based inks, especially for packaging production.
Finally, BOBST is dedicated to collaborating with brand owners and developing joint solutions with producers, developing and leading the packaging evolution and “shaping the future of packaging” together.