Consumables
Siegwerk and Komori set new quality standards with cooperatively developed K-Supply UV inks
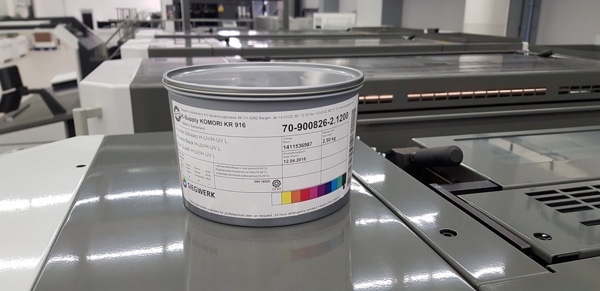
Tuesday 18. December 2018 - Komori Corporation and Siegwerk launched their revolutionary high sensitivity K-Supply UV inks, setting new standards for consistent color print quality, versatility, hardness and eco-friendly performance.
Komori Europe and Siegwerk have successfully partnered since 2016, when the international manufacturer of printing presses selected Siegwerk, one of the leading global providers of printing inks for packaging applications and labels, as its European partner to manufacture high sensitivity “K-Supply UV inks” exclusively designed for Komoris innovative H-UV/ LED system. Together both are now successfully marketing the new inks in Europe, the Middle East and Africa (EMEA) and have already built up a strong market position across the region with a continuously growing customer base.
“We cooperatively developed a brand new, revolutionary high sensitivity UV ink exclusively for Komoris energy saving H-UV/ LED curing system offering best-in-class print results. These novel K-Supply UV inks provide consistent colour print quality, high-level versatility and hardness as well as an eco-friendly performance,” says Bruno Delanoë, Regional Sales manager EMEA at Siegwerk. “They are characterized by top-level definition and press stability and match all Lithrone H-UV press requirements.” The newly- developed inks were designed and thoroughly tested in Siegwerks Center of Excellence in Aarberg, Switzerland, the companys Center of Excellence for UV inks and varnishes.
The alliance has built upon Komoris H-UV/ LED technology with more than 880 installations worldwide including 218 installed presses in Europe. The presses in production range from 26 to 40 sheetfed and up to 38 web printing. Today, Komori is one of the leading experts in low energy curing, offering its customers an innovative UV curing system that uses one H-UV lamp and runs with high-sensitivity H-UV/ LED inks from selected suppliers. In comparison to conventional UV curing, the amount of CO2 emissions from Komoris H-UV/ LED system is approximately one quarter. This exclusive Komori instant drying system doesnt produce ozone, ensures very low heat generation and offers superior print quality, reliability as well as an excellent economic and eco-friendly performance.
“At Komori, we design our printing presses to deliver the optimum print result with unrivalled quality, reliable performance, and superior colour intensity,” says Peter Minis, Marketing Manager at Komori Europe. “Teaming up with Siegwerk proved to be essential in Komoris endeavor to strengthen and broaden the K-Supply brand and product range. This partnership enables us to fully exploit all possibilities of our H-UV/ LED technology, and make them available, directly to our customers.” Under the “K-Supply” brand, Komori offers its customers a lineup of special consumables and materials that are officially approved for the companys printing presses.
Siegwerk has a standardized and reliable process when it comes to implementing carefully-selected raw materials and intermediate products. It is closely monitored by the companys quality control team, and fully compliant with the most stringent safety and environmental standards. This also includes compliance with changing regulations and reclassifications in the EuPIA (European Printing Ink Association) Exclusion Policy. Just recently the commonly used photoinitiators Omnirad-369, Ethyl-4- dimethylaminobenzoat (EDB), 2-Ethylhexyl-4-dimethyl-aminobenzoat (EHA) and 4-Phenylbenzophenon (4-PBZ) have been reclassified to CMR (carcinogenic, mutagenic or toxic to reproduction) Category 1B and therefore are voluntarily banned in the printing industry. In compliance with the European regulations, all inks still containing these photoinitiators have to be labelled as toxic for reproduction and, according to the EUPIA rules, have to be reformulated usually within six months. As a leader in product safety, Siegwerk promptly reacted and replaced these materials with substitutes equivalent in terms of performance and conformity for food packaging but without harmful properties. The company has always been on the forefront of ink innovation and performance while always complying with highest safety standards. All its inks and varnishes are formulated and manufactured in accordance with Good Manufacturing Practice, taking into consideration many individual and varying parameters relating to substrate, application and end use, enabling fully tailored solutions that meet all individual customer needs.