Inkjet & Digital Printing
Think out of the Box – Heidelberg shows packaging solutions for the digitized future
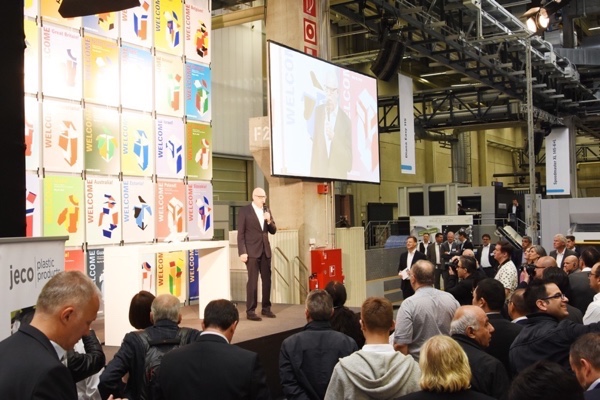
Monday 28. May 2018 - In the middle of May, more than 400 guests from all over the world attended the Packaging Day hosted by Heidelberger Druckmaschinen AG (Heidelberg) at the Wiesloch-Walldorf site.
Under the slogan “Think out of the Box”, they witnessed the premiere of the Primefire 106 – what up until then was only available to see in customers print shops and in the laboratory environment is now also installed in the Print Media Center Packaging, and thus completes the extensive demo range in the worlds biggest demo center for packaging solutions. Heidelberg is the only manufacturer to integrate offset and digital printing including finishing via the Prinect workflow, and is opening up new business models for packaging printing.
“With this range, Heidelberg cements its position as the leader in packaging printing and provides answers to current and future requirements in the age of digitization. We make our customers more productive and therefore also more profitable,” explained Rainer Hundsdörfer, Chief Executive Officer of Heidelberg, in his welcome. This was impressively confirmed by the two Managing Directors Thomas Pfefferle and Martin Bruttel from colordruck Baiersbronn. colordruck is a decade-long customer of Heidelberg and has seen its business models go through many successful evolutions. The Primefire 106 has been installed at colordruck since the end of last year and has been undergoing field testing since mid-January 2018. The Primefire offers colordruck the advantage of high-quality digital printing in combination with sheet finishing using existing die-cutting tools in 3b format. The packaging service provider, which operates throughout Europe, has been producing packagings using digital printing since 2017. In its new “Packaging Digital” division, colordruck offers customized and personalized packagings through to mass customization via its online shop “designyourpackaging.de”. In this way colordruck is opening up new customer groups. In its offset printing arm, colordruck continues to produce premium packagings using four highly automated Speedmaster machines from the latest generation.
Information tours provide answers to the trends in the packaging industry
The Packaging Day offered the visitors a platform for getting new ideas and inspiration for their current and future business models. Three information tours – “Packaging as you like”, “Operational Excellence”, and “Special Applications” – addressed the trends in the industry and provided a comprehensive presentation of the corresponding solution from Heidelberg.
In addition to demonstrating overall solutions, special highlight shows enlarged upon topics such as navigated printing in large format with the Speedmaster XL 145 six-color press with coating unit. The topic of postpress packaging showed economical solutions for postpress requirements. The Primefire 106 also had its own exhibit on the topic of industrial digital printing.
Lifecycle Solutions with the components Saphira consumables and service are an essential part of Heidelbergs solution offering for achieving top quality, productivity, and production reliability. Saphira has established itself as a quality brand in ten years
Trend towards customized packagings is growing
The answer to the trend towards declining run lengths and mass customization through personalization and individualization is the seamless integration of digital processes into existing offset landscapes. The information tour “Packaging as you like” showed how the Primefire 106 and the Speedmaster XL 106 are perfect complements for developing new customers and new areas of business. Using two identical folding carton jobs, Heidelberg showed how digital and offset printing offer economically viable product developments. For example, customers can now be supplied with long runs as well as personalized runs or short preliminary runs, and Heidelberg ensures end-to-end color consistency. In postpress, machines like the Promatrix 106 CSB diecutter with blanking function and the new Diana Easy 115 folder gluer can be used both for offset and for digital printing.
The information tour “Operational Excellence” showed how growing cost pressure and falling margins can be addressed successfully. An alternative for the profitable production of short runs with shorter delivery times was presented to this end. Productivity analyses show that the overall equipment effectiveness is currently at 20 to 25%, but that values of over 50% are absolutely achievable in the long term. This is made possible by lean, intelligently controlled processes that systematically minimize the influence of the operator on productivity and deliver real-time, transparent, and accurate performance data. What is important here is maximum integration without system breaks – starting from the customer all the way to the delivered product. The Prinect modules offer a variety of coordinated solutions here.
To increase productivity and reduce process interventions, Heidelberg has been developing the innovative Push to Stop operating concept since drupa 2016, clearing the way for autonomous printing. In packaging printing with its high complexity and many spot colors, navigated printing helps the operator to achieve the best possible result within the shortest time. This is achieved using the Intellistart 2 operating software in the Prinect Press Center XL 2 machine control station. This was demonstrated on a Speedmaster XL 106 six-color press with coating unit and logistics equipment – the makeready time can be shortened by up to 60% here and the paper waste is significantly reduced. In packaging printing, repetition accuracy and color consistency are important topics. The innovative Hycolor Multidrive drive technology for the Speedmaster XL 106 is used here. This system makes it possible to operate the inking and dampening units independently from the main drive. The inking units can be washed while the coating plates are being changed via the main drive – or the rubber blankets and impression cylinders can be washed at the same time as the makeready process. The system reduces makeready times easily, reliably, and highly effectively with the aim of improving consistency and increasing availability. A new feature is that Hycolor Multidrive now makes it possible to prepare printing units that are not currently in use for the next print job while the current one is still in progress. In this way, for example, the time for a color change can be saved by washing and changing the color at the same time as printing is underway.
Brand owners want maximum attention for their products at the point of sale through differentiation and embellishments. The information tour “Special Applications” inspired the visitors with Heidelbergs application know-how and economical ways of achieving embellishments. For example, the Speedmaster XL 75 Anicolor UV with twelve units produces premium cosmetic packagings including inline embossing within the shortest time. This delivers maximum productivity. Thanks to fully automatic, simultaneous plate changes, the large Wallscreen XL 2, and navigated printing, job changes can be performed very quickly even with highly complex embellishments.
The Speedmaster XL 106-8-P+LYYL showcased the full range of embellishments by effectively producing premium folding cartons with matt, gloss, and UV coatings. Cost-effective embellishments with hot foil, holograms, and embossing were on display on the versatile Promatrix 106 FC which is now available with the optical sheet registration system, MasterSet to ensure perfect alignment between image and embellishment. The Diana Eye 55 demonstrated how effective offline inspection can be used to check highly embellished products meet the highest quality standards and avoid expensive follow-up costs.