Finishing & Screen Printing
Streamlined in Four Weeks
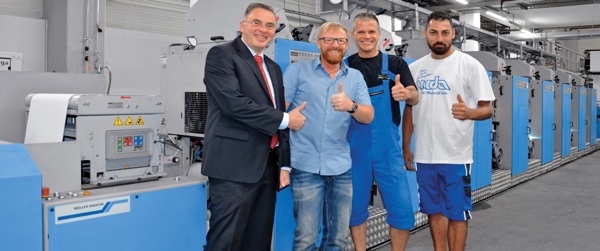
Tuesday 20. March 2018 - By relocating to a production hall that is less than half the size of its previous one, the Wailandtsche Druckerei printing plant has made its production more compact, more efficient and more environmentally friendly.
The company in the German town of Aschaffenburg makes products, including calendars, using two Muller Martini A52 printing presses. On just such a calendar, all the managers had to do was mark the four weeks in which its machine line-up would be relocated to the new site a few streets away. Thorough project planning and excellent cooperation with MMServices.Print technicians enabled the whole machine line-up to be relocated, reconditioned and given software updates during that short period.
Jürgen Zapf and Markus Sigusch, who were highly impressed with the relocation, explained that since each of the two printing presses was only offline for two weeks due to the relocation and reconditioning, they were able to keep on producing using the press that wasnt being relocated and reconditioned at any given time. The two Managing Directors of the Wailandtsche Druckerei printing plant can expect improved machine availability, stable printing quality over the long term and reduced downtime following the relocation from the old, expensive production hall. The use of LED lights and efficient exhaust air heat recovery have also made the companys operations more environmentally friendly.
The company, which was established in 1965 and has a streamlined staff of 19 people, specializes in the production of mailshots, advertising materials, large laser rolls, carbon-copy sets and commercial documents, as well as printing on special textile products. Special products that are produced using the two A52 printing presses include football passes, which are printed on a waterproof synthetic fiber substrate called pretex.