Consumables
Sappis Topliner has aesthetic appeal
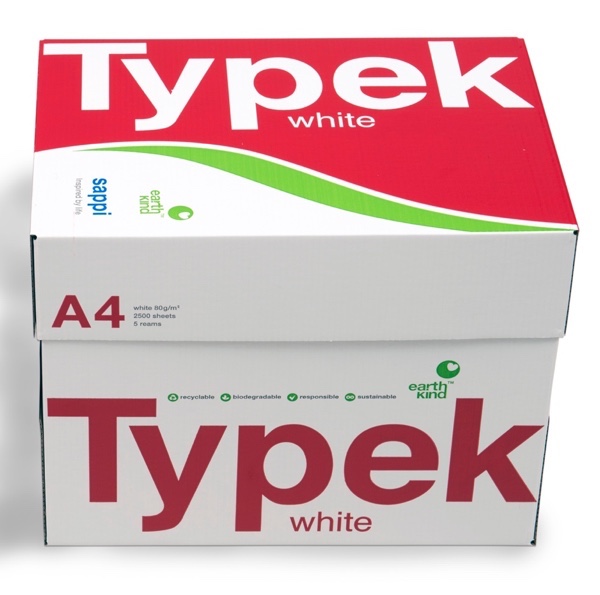
Tuesday 13. March 2018 - The aesthetic appeal and superior print quality results achieved with Sappis Fusion Topliner are enabling innovative brand owners to refresh their market impact.
Sappis Fusion Topliner is empowering brand owners to reinvent their print production approach for a wide variety of end uses from shelf-ready packaging, point-of-sale, pre-printed litho, flexo and fashion bags. A few years ago, the coated white corrugated board liner market was comprised of two possible applications: kraftliner, made from high quality raw materials with only a very small proportion of recycled paper; and testliner, made almost exclusively from recycled paper.
Sappi developed Fusion Topliner as an alternative to testliner – the most widely used liner for corrugated board. The double-coated bright white 100% virgin fibre liner is distinguished by its surface quality and strength while its brilliant white colour provides extraordinary colour reproduction for greater shelf impact and brand differentiation. As well as meeting food safety requirements, the use of bleached virgin fibres enables the grade to achieve the same material strength as testliners with a lower weight per unit surface area. The more enhanced fibre structure also means that folded edges do not crack.
Converters can enjoy a host of cost and time savings, too. Thanks to the functional reverse side coating of Fusion Topliner the absorption of glue is consistent and reduces consumption. This saves on costs, reduces drying times and ensures excellent flatness.
The grade also offers improved energy efficiency and a greater grammage yield advantage supporting lighter weights. Food safety, especially when combined with functional barriers, is another advantage of using virgin fibres.
One company that recently discovered the grades advantages is Corruseal Corrugated. The South African converter produced the box packaging for Sappis Typek consumer facing grade using its flexo post print process. This is where the liner is first printed and then laminated onto the corrugated board. As a result, small runs can be produced more economically and with greater flexibility.
It switched to Fusion Topliner to elevate the print quality for the outer packaging. Roland Cook, Corruseals General Manager, comments: “We tried Fusion Topliner to compare differences from a previous material used and were impressed with the results. With the outstanding quality Fusion Topliner delivers, we are now looking to add it to our retail and point-of-sale portfolio and recommend it to our existing brand owners.”
Bernd Gelder, Sappi Product Group Manager for Containerboard adds: “If total cost of ownership (TCO) are considered, Fusion Topliner is an attractive alternative to testliner and provides a significant competitive advantage to both the producer and the buyer of corrugated products. Cost savings achieved thanks to the lower weight, lower glue consumption, more efficient production and lower transport costs all add up.”
Fusion Topliner is available in grammages of 135g/m2, 160g/m2 and 180g/m2. It provides impressive strength properties (SCT, compression strength, for instance), which are comparable to those of kraftliners. A compelling advantage is its weight benefits, thanks to the lower grammage that can effectively be used: for a grammage of 115g/m2, Fusion Topliner achieves the same strength values as a 145g/m2 testliner. Also, the gain in terms of strength properties comes to about 25 to 30 percent.
With post-print, liners need to display as little rippling as possible after lamination. Tests have also shown that, above a grammage of 115g/m2, Fusion Topliner delivers very good results in the post-print process regardless of the printing method selected. Especially impressive too, is the materials capacity for printing without streaks.
Sappis Fusion Topliner is recommended for applications such as premium quality consumer goods packaging where high visual quality is required and when lightweight packaging and finer fluting are desired, using flexographic post-printing in addition to offset and digital printing technologies.