Offset Printing
Printing company Grafotisak using Push to Stop concept from Heidelberg for book production
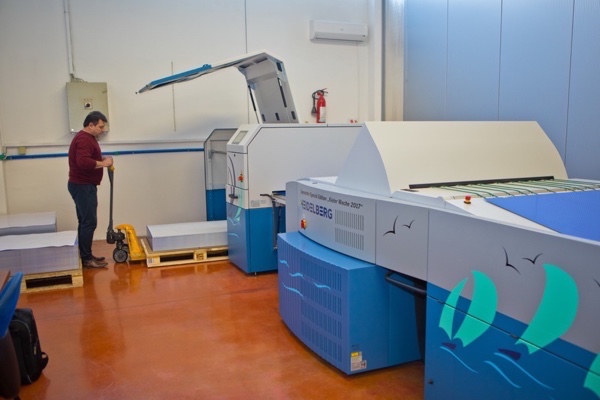
Thursday 22. February 2018 - According to Wikipedia, the town of Grude in Bosnia and Herzegovina is home to four large companies: an ice cream factory, one of the biggest toilet paper factories in Europe, a brewery, and a printing company. In fact, it may come as a surprise that Grafotisak incorporates a state-of-the-art print shop and warehouses for merchandise on a total area of over 26,000 m2.
Owner and Managing Director Stipan Vranje is from Grude, and established the company in 1983. Grafotisak has gradually developed into a Group with 600 employees and a total of ten sites in Bosnia and Herzegovina, Croatia, and Serbia. Half of its sales comes from school, office and graphics supplies, while the other half comes from print production of books and the corresponding logistics distribution.
Books account for 90 percent of the printing companys production, and are delivered to fifteen European countries. The export share is 80 percent. Grafotisak delivered 25 million books in 2017, and expects a ten percent increase this year. To cope with this, last year the company invested in a Speedmaster XL 106 from the latest drupa generation and a Suprasetter 106 CtP platesetter, as well as in Prinect modules for the integration of postpress. Heidelberger Druckmaschinen AG (Heidelberg) supplied everything from a single source, including intensive advice in advance.
Grafotisaks customers are well-known publishers like Taschen, Burda, Egmont, Disney, Harper Collins, and Gyldendal. The other ten percent of production is split between security printing of duty stamps for alcohol or cigarettes, folding cartons and lever arch file production. “Quality through time – weve achieved rapid growth in the print shop with this motto,” explains Marko Vranje, son of the owner and Technical Director. “We replace our machines every five years so that were always up to date and can deliver the best to our discerning customers.” The groups growth last year was 12 percent, and the goal for 2018 is up to seven percent.
www.grafotisak.com
Productivity and integration bring economic efficiency
To be able to handle all this, Grafotisak needs reliable and innovative partners. “Weve trusted in Heidelberg from the beginning, and know that they will listen to us and supply us,” confirms Marko Vranje. And so it is once again with the new Speedmaster XL 106 eight-color press with perfecting and a speed of 18,000 sheets per hour. This press is fully equipped with AutoPlate XL, Wallscreen, and Prinect Inpress Control 2, and works according to the Push to Stop concept in which the operator only intervenes to change plates or stop the press. “We can now have up to 30 jobs processed automatically, and in some cases are twice as fast as on the other presses,” explains Marko Vranje. Over 27 million sheets have already been printed since production started in July 2017. The pressroom now houses a total of 48 printing units from Heidelberg, including one Speedmaster XL 162 press, five Speedmaster XL 106 presses, one Speedmaster XL 75 press, and two Speedmaster SM 52 presses. The last big investment was in 2015, with a package consisting of the Speedmaster XL 162-8-P and a Suprasetter 162. This enables a book with 32 or 64 pages to be produced on one sheet.
New Suprasetter supplies three shifts
The current investment package also includes the first Suprasetter 106 worldwide, which images 55 plates per hour (pph). Up to now, the limit was 40 pph. It is a complete Suprasetter line with Auto Pallet Loader 106 K, Dual Cassette Loader with turn table, Glunz & Jensen Interplater 85 HDX, and a NELA bending line with two stacking stations and plate sorting. The Suprasetter thus fits seamlessly into the Push to Stop concept, in which the imaged plates are brought directly to the machines and each job is assigned appropriately. Around 1,200 plates in B1 format are imaged every day, which is exactly enough for three shifts. Since the software release for the capacity of 55 plates per hour and the completion of the CtP platesetter took place during Kiel Week, Heidelberg and Grafotisak came up with a novel idea: the Suprasetter 106 was painted with motifs from Kiel Week. “Were more than happy with the new Suprasetter, and its the star of our prepress setup,” confirms Marko Vranje.
Integration is the beginning and the end
With each investment, the workflow is also expanded and supplemented. For example, postpress was also recently integrated. It comprises four Stahlfolder TH 82-P machines. These work according to the shingled folding principle. This means that more sheets can be processed on the same line, resulting in a performance increase of up to 50 percent without raising the machine speed. High folding quality is thus guaranteed, even with delicate papers. Above all, it enables the high output of the five Speedmaster XL 106 to be processed and quickly delivered to the customers.
At Grafotisak, prepress, press, and postpress are integrated via the Prinect Integration Manager. The goal for the future is complete integration with the Prinect MIS system, so that offer preparation and costing are also covered. And with this transparency and access to all data from every location.