Finishing & Screen Printing
Investing for pharma packaging success at MPS Leicester
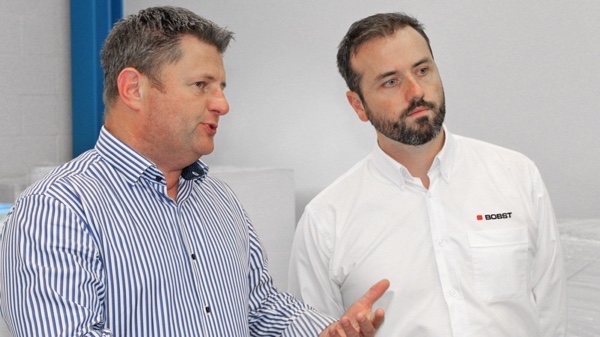
Tuesday 23. January 2018 - Consistent business success is rooted in designing the complete operational mindset around the needs of the target market, according to Operations Director, Mark White of Multi Packaging Solutions (MPS) Leicester.
Recently acquired by US packaging giant WestRock, Multi Packaging Solutions is a leader in the design and printing of folded cartons, labels, inserts and rigid packaging for the branded and healthcare market sectors (MPS is global and not just UK).
With a 220 strong workforce led by White, the team at MPS Leicester understands the importance of focus and commitment when it comes to supplying the often complex and fast moving healthcare sector, which has been the mainstay market for the site for many years.
“Packaging converters often believe they can tick boxes in a manual to supply the pharmaceutical market but the risk of getting it wrong can be high. At MPS we have a depth of understanding and expertise around our customers needs, from security to traceability to specific pack data and information requirements they seek. We strive continuously to invest in the latest technology and processes to de-risk our production and ensure 100% compliance at all times and our level of repeat work is testament to that commitment,” says White.
As part of its efficiency strategy, MPS Leicester has recently invested in a BOBST NOVACUT 106 ER Autoplaten die-cutter for in-line blank separation. The machine drives flatter, more consistent blanks straight into the finishing process and removes the need for hand stripping, for all but the smallest jobs.
Craig McGowan, BOBST Area Sales Manager, commented: “Its been really interesting watching the process MPS has adopted in investing in automated blanking. Historically, many companies have believed that the cost of automating far outweighs the savings made, compared with hand stripping, and that it can only be used for long run, large format work to be cost effective.
“This simply isnt true anymore. With the developments being made in blanking tools, ensuring they are more cost competitive, converters can now utilize blanking technology for short run, small format jobs. And when blanking isnt required, a full sheet delivery system is available which allows MPS production avoiding any bottlenecks.
“At MPS we see a machine running at the speeds promised, being used for large format as well as short run jobs down to less than 1000 sheets, and still achieving set up times of around 30 minutes. This means the NOVACUT is in continuous use and adding 5-10,000 additional cartons per hour to the gluing lines enabling great service for the shorter run, higher frequency demands from customers. A great result for the site.”
With UK packaging sales of over £10 Billion, according to The Packaging Federation, and pharmaceutical sales representing circa 10% of the market, there is a large-scale opportunity for business growth. MPS is the market leader in the sector and is strategically investing at the Leicester site to ensure continuity of its success.
White says: “Pharmaceuticals is a highly sensitive market place – we cant afford mistakes and having highly committed and educated staff who are loyal to the company with a good work ethos is key. The number of jobs we can run at full speed has now significantly increased and were setting the benchmark for quality in our industry.
“Investing in technology is not about removing labour at MPS. We have a very strong training and education ethos at the site. In fact, a very high percentage of our number two cut and crease employees, printers or finishers can step up and lead in the number one role, whenever required. We are continually training and retraining staff as we invest in technology to ensure we close skill gaps, provide optimum employee skill availability and minimize the risks to our business when staff changes occur.”
“Pharmaceutical work, like many other packaging sectors, is becoming more complex and yet increasingly consists of shorter runs. The pharmaceutical brands are demanding new security features to stay ahead of the counterfeiting market and additional functionality from their packs, for example integral fittings, tagging or RFID. Packs often require inserts, as well as new graphic or tactile effects,” adds White.
“Were also seeing more legislative requirements as well, so the printers job is becoming more challenging. We need our technology investments to meet these emerging needs and with the size of jobs reducing, but order frequency increasing, machines like the NOVACUT become critical to our operation to minimize make readies and drive efficiency.”
The MPS Leicester site serves customers direct or via its Swadlincote distribution centre, which has over 20,000-pallet capacity. Customer ordering flexibility is maximised to meet the variable needs of the market – whether it’s the hay fever or flu season – and lead-times are kept short as a result of the investment strategy at the company, thus giving the sites the ability to deliver on a consistent basis.
“Fast turnaround supply has always been key to MPS success in Leicester,” says White. “However, our unparalleled focus on quality, traceability and accountability, with respect to pharmaceutical and healthcare procedures, has ensured our continued growth in the market.
“The systems and technology we have in place at Leicester, with scanning capability on every station, ensures we are going the extra mile to de-risk our business and ensure we eliminate the risk of seeing admix occurring (the supply of one pack design continuing on to the next order) for example; a nightmare scenario for any brand is to find the incorrect packaging on their product.
“We work continuously to ensure our people are focused on minimizing errors, our systems are fully controlled and our technology is delivering the next generation of efficiency and compliance in order that we can be the best suppliers possible, in what is an ever-changing market.”
With many cut & crease and gluing lines, now including the new BOBST NOVACUT 106 ER, working across all formats, the MPS Leicester team has the ability to grow; yet more importantly, has the technical skills and technology to over-deliver and secure a successful future under its new WestRock ownership.