Packaging
Compression and total quality control, the Sacmi response to the Indian market
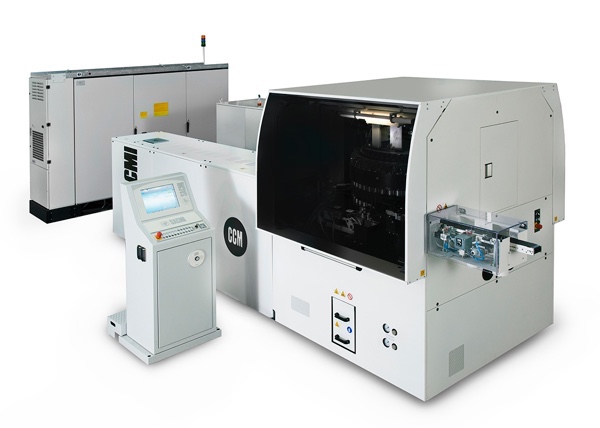
Thursday 19. January 2017 - Group soon to take part in the Plastivision fair in Mumbai (19-23 January 2017). Visitors will have a great chance to see the CCM press - the worlds most competitive solution for the production of single-piece caps for CSD, water, hot filling and cold aseptic filling - working in synergy with advanced cap and preform vision systems developed by Sacmis Automation & Inspection Systems division
A key player in the country with Sacmi Engineering – a one-stop production, business and assistance centre for the entire Indian market – the Sacmi Group will soon be at Plastivision in Mumbai (19-23 January 2017) to display advanced solutions for plastic cap production and quality control. Playing a starring role will be the innovative CCM48SC, equipped with a mould for the manufacture of HDPE caps for still water (as per the local A27W-4 standard), weighing just 1.29 grams and with a diameter of 27 mm. Already sold to a major local customer, the displayed solution will be put into service after the exhibition period.
Over 200,000 visitors are expected to attend the event, giving them an opportunity to get a close look at this cutting-edge Sacmi technology, a symbol of productivity, reliability and energy savings. Acknowledged as the worlds most competitive plastic cap production solution, the CCM has the lowest cycle times on the market, not to mention very low energy consumption (in the proposed application the CCM can manufacture up to 2,000 caps a minute with a cycle time of 1.44 seconds and energy consumption of just 0.4 kWh per kg of processed HDPE). Thanks to the outstanding characteristics of the compression process, which occurs at temperatures lower than those needed for injection, it is also possible to obtain lighter, higher performance caps.
Decades of know-how in the industry and thousands of plants worldwide have allowed Sacmi to refine this technology, which ensures extraordinary process repeatability and, therefore, the manufacture of caps with improved characteristics in terms of weight and size consistency. The CCM48SC is one of the latest developments in the range and will be on show at the fair (hall 1, stand E2-1, 156 m2) together with the advanced CVS 052 vision system, installed on the machine and perfectly integrated with the CCM press control system.
Installed downstream from the press, this solution is part of a comprehensive range of vision systems developed by Sacmis Automation & Inspection Systems division for all-round control of every single step on the bottling line, from caps to labels, up to container and preform.
Other proposals deserving of a special mention include the PVS (preform vision system) range for the inspection of PET preforms. Designed by Sacmi, these can operate both in-line with the moulding press – at effective inspection rates of up to 70,000 preforms per hour – and out-of-line before stretch-blow moulding, or in research labs.
Like all Sacmi inspection systems, the PVS range features the latest CVS 3000 2.0 64 bit software version, which lets users set parameters easily and focus control on specific areas of the preform. Thanks to its modularity, the PVS can be enhanced with a whole series of functions such as weight and body control – via an exclusive, patented “grid” method – that have been added to the standard checks (opening, finish, thread, body and bottom) and are managed via a high resolution camera system that allows all-round product analysis.
Quality, productivity, low consumption: these are the very hallmarks of Sacmi, which has had an organised presence in India since the 1980s: since 2014, this has included the “new” Sacmi Engineering company based in Ahmedabad, a flourishing industrial centre in Gujarat State. Sacmi Engineering operates as a single production, business and assistance centre for all projects on the Indian market handled by the two branches in Morbi and Mumbai. Sacmi thus combines technological excellence with service efficiency in an area that has been growing dynamically for years and is thus strategic to the growth and development prospects of all Group businesses.