Inkjet & Digital Printing
Screen Truepress Jet L350UV Expands Opportunities for Short-Run Labels and Folding Cartons at Lithotone
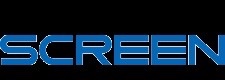
Wednesday 13. April 2016 - Three key factors in recent years have been cited as driving demand for inkjet label presses: production efficiencies, especially for short and medium run lengths; the power of digital inkjet presses to enable variable data printing; and advances in jetting assemblies that have significantly improved print quality and reliability.
Lithotone Inc. in Elkhart, Indiana, has been ahead of this curve for a while. Lithotone became the first printing company in the world to have a Screen Truepress L350UV inkjet label press in production, installing the press in January 2014.
The Truepress L350UV is able to provide pressure-sensitive product labels on demand without the requirement for printing plates and offer faster turnaround times than conventional printing processes. To create a more complete digital solution, Lithotone implemented an AzTech 18-inch rotary die cutter with lamination and UV coating.
“The Truepress Jet L350UV is extremely functional in terms of what it can accomplish,” said Jim Priebe, executive vice president of Lithotone. “Digital custom printing allows us to gang run 10 to 15 labels that are a different design of the same size without stopping the press. We have printed unique non-label projects that the Truepress wasnt actually designed to do, such as small folding cartons and hang tags. Being able to print on both sides of the substrate creates additional opportunities to print letterheads, variable data bill stuffers and other interesting products.”
In an environment in which print providers have to be nimble on multiple fronts, the 54-year-old shop started acquiring digital printing equipment eight years ago to deliver short-run commercial products. Since then, Lithotone has steadily expanded its digital footprint.
Today, a diverse mix of toner-based and inkjet presses, configured for monochrome and color, cut sheets and rolls, shares the firms 45,000-square-foot manufacturing facility with commercial sheetfed and web offset presses. In addition to complex color products, catalogs, movie advertising programs and publications, Lithotone prints labels and litho-laminate.
“We have evolved into an imaging company, rather than the conventional printer we used to be,” Priebe pointed out. “We put ink on almost every substrate, whether paper, glass, plastic or wood.”
The Truepress Jet L350UV, designed for short-run and medium-run narrow-web applications, supports web widths from 4 inches to 13.7 inches and runs at a printing speed of up to 164 feet per minute. Lithotone was drawn to its precise image quality, smooth gradations and drop-on-demand grayscale printhead technology.
“The vast majority of our digital labels are printed on white BOPP and white PET,” Priebe said. “A lot of the digital label presses we looked at exhibited problems with artifacts and vertical lines being sprayed out into high-density areas. The Truepress Jet L350UV does a really good job of laying down solid coverage with process colors.”
Consistent printing and heavy coverage play a significant role in creating crisp, detailed and vibrant labels with white ink.
“White ink is almost a must-have feature,” Priebe noted. “At the moment, projects that require white ink account for about 10 percent of our label work. We can produce different effects in subtle ways or very prominent ways by controlling the density of the white ink. It allows us to print rich colors on top of a simulated white substrate. Printing colors over a white base layer on metallic substrates achieves eye-catching visual effects.”
Because its setup and makeready costs are minimal and color matching is flawless, the Truepress Jet L350UV has made the world of custom-printed packaging accessible to Lithotone.
“The Truepress Jet L350UV is capable of printing on up to 18-point carton stock,” Priebe said. “At 164 feet a minute, it produces runs of 5,000 small-sized folding cartons cost-effectively, especially when you can put 15 or 20 cartons up on the form. Then we feed the printed roll through our rotary die cutter and quickly have folding cartons ready to glue. The press excels at just about every project we do on it.”