Offset Printing
An investment in a fully automated product from Q.I. Press Controls provides quick returns
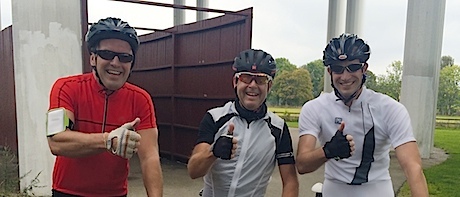
Thursday 06. August 2015 - In January 2014, Karlskrona-based Sydostpressarna in Sweden opted to install a fully automated system from Q.I. Press Controls. One year later, Q.I. Press Controls went back to find out what happened next. The organisation, it seems, is more than happy with the results.
Sydostpressarna forms part of Gota-Media AB, the owner of eleven national dailies and some weeklies with a strongly regional focus. In the first instance, the printing company was interested in a register system, but after a fact-finding visit to a satisfied client they soon became enthusiastic about a fully automated solution. In January 2014, Sydostpressarna became the first company in Sweden to invest in the mRC-3D for colour register, IDS for colour control (including humidity control) and the IQM reporting tool. The system was installed on a manroland GEOMAN press and the company had two clear objectives in mind: cost savings and improved quality. Jan-Åke Lundgren, Sydostpressarnas Plant Manager explained why Q.I. Press Controls had been chosen: “Weve known about Q.I. Press Controls for years. We were looking for a system whose primary objective would be to cut down on labour. After painstaking research, it became clear that Q.I Press Controls had the solution we were looking for and was really able to cut back on staffing costs. Because the image-based functionalities of the system match the very same tasks carried out by an operator, the system is able to repeat these operations in full.”
In September 2014, Erwin van Rossem, Area Sales Manager at Q.I. Press Controls, visited the Karlskrona-based plant together with Jarl Söderqvist, agent for Q.I. Press Controls in Sweden. Like Lundgren, they too are avid sports cyclists. The deal was, that if the system delivered on its promises, Lundgren would take them on a bike tour in the wonderful countryside around Växjö. The system had only been in place for a couple of months and “in this short space of time, the product had already proved its quality in this short space of time, in a way that the company had never experienced before,” according to Van Rossem. Not only that, waste had been reduced by almost a 1/3 and it had already saved on one full-time job.
According to Lundgren, one year on and it is expected the following economies will have been achieved: “We continue to make savings in terms of materials used, staffing levels have been curbed and quality has improved markedly.” From the very outset, the mRC-3D performed in line with expectations and at the current moment, density control is operating according to plan. Although ink levels are now stable, savings have not yet been achieved. Lundgren believes that this can be put down to the much improved resolution of the images they are now working with and ink reductions will soon follow. System reliability is exceptional Lundgren explains: “So reliable in fact that the operator is standing around for much of the time. One push of the button is all it takes!” The printers agree with this comment: They have mounted a golden medal onto the reporting screens because to them, the system is the best printer we have ever seen!
Over time, the system is improving in line with expectations. The customer is extremely happy in having opted for the Q.I. Press Controls solution and that results are in keeping with those that were forecast. When this continues, the target will certainly be met and the investment will end up in extremely attractive payback times to say the least. “Q.I. Press Controls is now putting the finishing touches to the fine-tuning of the water control,” explains Lundgren. “I therefore expect that we can achieve even greater savings in the future so that we can improve on quality even more.”