Offset Printing
Fifth Rapida sheetfed offset press in only ten years
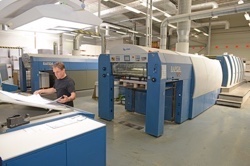
Tuesday 26. May 2015 - Druckerei Rindt continues to grow with KBA medium format
Many a major packaging group invests less frequently than Fulda-based Druckerei Rindt: A new medium-format Rapida press was installed in each of the years 2004, 2005, 2006, 2010 and 2014. Three of those five presses are still in production in the modern Rindt printshop today: Two five-colour models and a four-colour coater with extended delivery. Despite the differences in age, they all have one thing in common – the plate cylinder direct drive technology DriveTronic SPC. The latest addition to the line-up was a five-colour Rapida 106, which was configured, among other options, with QualiTronic ColorControl for inline ink density measurements, LogoTronic networking and a “High Speed” package for production outputs of up to 20,000 sheets per hour.
Is Rindt a commercial or packaging printer? Or rather a company which serves niche markets? The truth lies somewhere between. “Business as usual” is a practically unknown concept at Druckerei Rindt. Every job is different and calls for individually adapted processes. “For us, there is no such thing as ‘technically too demanding’ and even the fastest imaginable delivery times are realised,” says plant manager Sebastian Jerabeck. That could mean short-run packaging jobs, just the same as highly complex print products with essentially inline refinement and finishing, for example transparent papers which are printed first with opaque white through a coating unit and then four standard colours, before being passed on for register-true cutting and final processing. Mention can also be made of the sophisticated covers which are printed in up to five colours for parent company Parzeller, as well as further conventional products. Or jobs which Internet printers are unable to offer, e.g. for format reasons, because they break the business model of production with gang formes.
The range of substrates handled is correspondingly broad – from 50 g/m2 sandwich paper through to 500 g/m2 boards. Jerabeck sees the company’s strengths in the overall scope of services offered, from advice and planning through to actual production and reliable on-time delivery.
Convincing package
)When it was decided to build new premises in 2004, the print specialists at Rindt began a comprehensive evaluation of the various press technologies available on the market. The decision fell in favour of KBA, not least thanks to the convincing all-round package, which Sebastian Jerabeck characterises as the blending of press performance data with the human component of trustful cooperation. The latter aspect is reflected in a comparable, solution-oriented corporate philosophy. Over the past ten years, the business relationship has developed into a true partnership. The cooperation has already covered numerous fields and both sides are fully aware of the demands placed on equipment and technologies. That all makes life so much easier for everyone concerned.
For Rindt, the key performance parameters are all those which make production even more efficient and profitable. Current highlights include ultrafast makeready thanks to simultaneous plate changing, inline measurements to safeguard quality, and the frequently practised maximum production speed of 20,000 sheets per hour. On the one hand, this forms the basis for short-run book production at a level of cost efficiency which shies no comparison with digital print, but at the same time also enables high-volume jobs to be turned around with a minimum of delay.
Latest technologies from pre-press to post-press
It is not only in the printshop that Druckerei Rindt implements the latest technology solutions. The same philosophy is followed along the whole production chain from the chemistry-free pre-press (Agfa) through to post-press finishing with its diversity of automatic cutting and folding machines, saddle-stitchers and naturally also offline finishing systems. A further fully automatic saddle-stitcher from Horizon was commissioned only recently. Like the Rapidas in the printshop, the post-press equipment receives the necessary preset data in CIP3/JDF format.
The opening of new premises 11 years ago was also an opportunity to optimise material flows and production sequences. Since a further expansion in 2012, the company has floor space totalling 4,500 m2 at its disposal. The production departments occupy an upper level, with the administrative offices below. Thanks to the hillside location, however, both levels can be accessed directly from outside. Approx. 3,500 tonnes of paper and board are printed and processed every year – with an increasing tendency. Annual growth remains constantly high, which is today something special in the otherwise rather turbulent print industry.
Rindt currently counts 70 employees. The local print business founded by Bernhard Rindt in the 1930s has in the meantime developed into a nationally recognised supplier of high-quality print products. Particular importance is attached to good vocational training and the company usually offers regular employment to all successful trainees who wish to stay. Sound specialist knowledge, after all, is prerequisite for the positive future of the print industry in general and Druckerei Rindt in particular. Indeed, the combination of specialist knowledge and a modern quality management concept is especially appreciated by the company’s customers. The facilities for inline inking control with QualiTronic ColorControl on all three Rapidas here play a significant role. Furthermore, up-to-the-minute data on every job can be called up through the LogoTronic production management system. In this way, customers are able to check the production data for their jobs and monitor the quality-compliant execution.
Sebastian Jerabeck is well conscious of the fact that the print market remains a tense arena. The decisive question, however, is how companies tackle the challenges. There is nothing to be gained from waiting and moaning. At Druckerei Rindt, therefore, special attention is paid to analyses of the market. Jerabeck: “The findings help us to plan better for the future, though that is by no means a simple matter, and there is always a certain element of risk.” After all, even new technologies bring no overall benefit if others are already using them. “The only way to improve is to move ahead and not look back” – that is the motto for Rindt. “And we can be thankful for the exceptional foresight of our shareholders, who are continuing to invest even in a time of shrinking markets,” Jerabeck adds. The print market is sure to experience further consolidation and some of today’s print companies will probably disappear from the market with time. But concentration will also offer companies like Rindt sufficient opportunities to grow further in the future.