Offset Printing
Researching the optimum production process
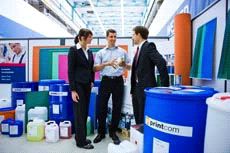
Thursday 17. September 2009 - Stable conditions for the development of system components
In the new Print Technology Center (PTC) in Augsburg, Germany, printcom is conducting detailed tests on pressroom products for newspaper and commercial printing. The newest products, which have passed the testing process and carry the printcom seal of quality are a silicone H 119N and, from the end of 2009, a new dampening solution.
For over 15 years, manrolands printcom brand provides its customers with high-quality, process-compliant products that are perfectly coordinated. printcom products ensure a stable printing process, which guarantees performance and protects press components. In the past twelve months alone, printcom conducted eight large research projects for web offset printing. The development focus is on materials crucial to the results of the printing process: blankets, blanket plates, dampening solutions and washing agents, as well as silicones. printcoms overall objective is to improve the quality, avoid unnecessary costs, such as waste, increase the service life of products, and to create materials that have less impact on the environment.
Together for more know-how
At printcom, only high-quality brand products that meet the requirements of the FOGRA Graphic Technology Research Association or other official inspection authorities of the printing industry are accepted for testing. Depending on the research project, up to 400 individual chemical, mechanical, and dynamic tests are performed on a product. Since July 2009, the testing departments with their testing presses, which include a heatset web offset press as well as the printing tower of a COLORMAN, XXL, are integrated in the new Print Technology Center (PTC) in Augsburg. Here, it is possible to reproduce all production-relevant printing processes as well as printing environments. These unusually diverse, workflow-oriented tests are not only used by the manroland researchers, including chemists, physicists, mechatronics engineers, electricians, and printing engineers, but also manufacturers of consumables and customers use the unique test opportunities for their own developments and to research product combinations.
New addition to the family: silicone H 119N and new dampening solution
Almost three years of development went into the new dampening solution for heatset printing. As version DP503Q it is currently in the last beta test phase at customers and will be market-ready by the end of 2009. Its special feature: it reduces the ink and paper deposits on the rollers. It thus not only stabilizes the printing quality; fewer washing cycles are required, as well. The low start-up waste saves time and costs.
The new printcom silicone H 119N stands for exemplary, fast development. It received the printcom quality seal in only nine months. In production, the H 119N is distinguished by homogenous application on the paper. This is achieved by the special combination of high-viscosity silicone oils and anionic emulsifiers, so that no deposits occur on the former and the guide rollers – even at high color imposition.
Development never stops
For printcom products, to be market-ready does not mean that their development is completed. All products are subject to a continuous improvement process, based on feedback from customers worldwide. Reports from printing instructors and service staff, who experience production work on site on a daily basis, as well as new market requirements, provide key information. Quality fluctuations are detected, as well. If the manufacturer cannot remedy the faults in a timely manner, the product will no longer be granted the printcom quality seal.
Well-equipped and well-advised – from the very beginning
All together, the seven product ranges contain approximately 300 products, and printcom adds 30 to 50 new products to its portfolio each year. Not all of these are manrolands own developments: Many are developed in cooperation with manufacturers, or are purely by-products such as cleaning cloths or rubber gloves. However, each product comes with a clear recommendation for each press and application. In part, these specifications vary due to regional and national production processes. Nonetheless, the objective is to offer two to three alternatives per product group. So customers are not dependent on a specific manufacturer. In addition, printing instructors provide individual consultation on site at the printing companies. Thanks to the instructors experience and expertise, customers can find the accessories best suited to their applications. To ensure that presses start up with optimally coordinated pressroom products, manroland has developed proven start-up sets for commercial and sheetfed printing. These sets usually include 40 products for pressroom and pre-press: from volume products, such as dampening solution additive and washing agents, to buckets and sponges. The optimum start-up set newspaper printing is currently under final preparation.