Packaging
New in the USA: electric Allrounder processes solid silicone rubber
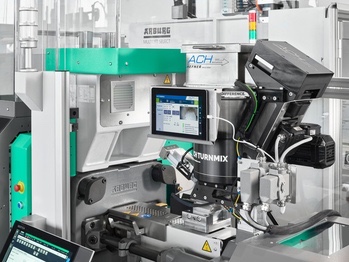
Wednesday 18. December 2024 - Arburg demonstrates the automated processing of solid silicone rubber on the stand. The electric Allrounder 470 A Comfort with a clamping force of 1,000 kN is equipped with an ACH Turnmix for a continuous material feed free of bubbles.
• Spotlight: reliable processing of solid silicone rubber (HCR) on electric Allrounder 470 A
• Focus: target groups are the medical, automotive and aerospace industries
• On trend: surging demand for digital products and services
At Plastec West in Anaheim, California/USA, taking place from 4 to 6 February 2025, Arburg as a solution and system partner will showcase exciting topics such as silicone injection moulding, digitalisation and automation. On stand 4229 in Hall B, the processing of solid silicone rubber (HCR) with continuous material feed by a Turnmix dosing system will be demonstrated live for the first time in the USA. The exhibit, an electric Allrounder 470 A, is automated with a linear robotic system Multilift Select 6.
Medical technology is one of the trade fair’s key areas. This sector relies on the use of silicones, particularly in applications involving HCR (High Consistency Rubber). Alongside NPE, held every three years, Martin Baumann, Managing Director of Arburg Inc. in the United States, sees Plastec West as one of the most significant trade fairs in the United States: “We are delighted to be demonstrating the processing of solid silicone rubber with a continuous Turnmix dosing system for the first time in the North American market. We will also be showcasing numerous digital products and services. Our arburgXworld customer portal and the Arburg ALS host computer system give us an excellent position here.”
Automated processing of solid silicone rubber (HCR)
The dosing system, available in three sizes (S, M and L), can be used to produce silicone parts with a wide range of Shore hardnesses based on small to large shot capacities. Consistently uniform, high-quality feeding conditions can be ensured by pressure measurement. In addition, a second flow volume can be used to add colour or other additives. The Turnmix offers optimal control of the gas release when mixing silicone and dyes. Other advantages are the easier application than liquid silicone (LSR), the processing of a pre-mixed compound that can be stored without a problem, as well as ongoing production even when material is being replenished. The energy- and production-efficient injection moulding of cable ties will be demonstrated at Plastec West.
The equipment, precisely matched to HCR processing, makes the electric Allrounder 470 A “Comfort” an economical injection moulding solution. The silicone equipment package includes an injection unit with adapted screw geometry, cylinder temperature control and nozzle technology. The material to be processed is Addisil from Momentive. A 2+2-cavity mould from company ACH Solution will be used; the cycle time is around 30 seconds. A Multilift Select 6 linear robot system performs the handling tasks.
“Soft-touch” products and additive manufacturing
“We believe our target groups for HCR applications are increasingly in the medical, automotive and aerospace sectors,” says Martin Baumann. He has noticed an increasing demand in the US market for “soft-touch products” that can be used reliably even under extreme temperature conditions. HCR components are the ideal solution here, because silicone is a material with relatively good thermal and chemical resistance.
Besides visiting the Arburg stand, dropping by Samaplast stand will also prove worthwhile (Hall C, Stand 2861), where industrial additive manufacturing with the Freeformer will be presented with a focus on components for the medical technology sector.
Arburg – “more than a machine”
As a system and solution partner, Arburg well and truly supports its customers under the motto “More than a machine” – covering everything from procurement and technical equipment to process optimisation, tool testing, machine comparisons and training. It goes without saying that alongside a complete range of services provided by Arburg technicians throughout the United States, customers get comprehensive advice on application technology and digitalisation.
Digitalisation is playing an increasingly vital role in plastics processing, helping to significantly enhance the efficiency of machines and systems. The arburgXworld customer portal, for example, provides quick and easy access to service data, documentation, reports and more. Always with the goal of maximising efficiency, sustainability and quality in production.