Offset Printing
Lithrone GXG advance EX Edition: New benchmarks for productivity and sustainability
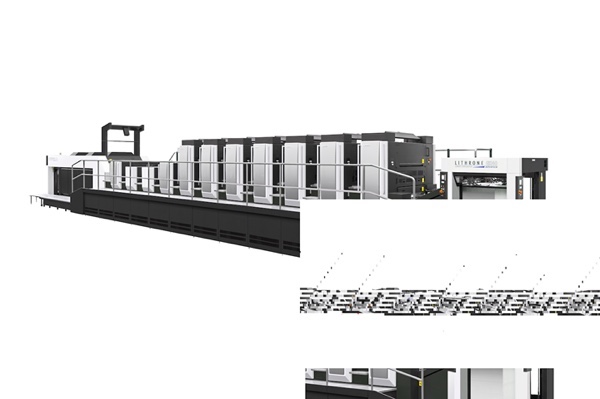
Tuesday 30. April 2024 - An optimized roller arrangement backed by state-of-the-art analysis, not only ensures enhanced print quality through stable density control but reduces exhaust heat and energy consumption by alleviating the load on the rotary drive.
Komori Corporation (Sumida-ku, Tokyo; President and CEO: Satoshi Mochida) is pleased to announce the development of the Lithrone GX/G advance EX. This press will be unveiled at drupa 2024.
Lithrone GX/G advance EX Edition:
New benchmarks for productivity and sustainability
Boasting world-class return on investment, the Lithrone GX/G advance Series is being introduced globally. Its ever-evolving productivity adapts to the times, addressing major challenges such as escalating energy costs and a shortage of operators that suppress the profits of printing companies. To tackle these issues and achieve further productivity growth and sustainable management, Komori has developed the Lithrone GX/G advance Series equipped with revolutionary new functions. Leveraging the latest printing technology, this latest development from Komori reduces energy costs and enhances operator efficiency, propelling businesses to new heights.
Three essential developments achieve sustainable printing
Komori has pioneered an eco-friendly offset printing press designed to support printers while reducing greenhouse gas (GHG) emissions. By means of three eco-conscious functions, the press reduces power consumption by up to 18%* while printing and realizes stable feeder and delivery operation to cut wastepaper usage, thus both achieving reduced GHG emissions and high productivity.
*Effect of Smart Inking Flow and DC blower together
1. Smart Inking Flow
An optimized roller arrangement backed by state-of-the-art analysis, not only ensures enhanced print quality through stable density control but reduces exhaust heat and energy consumption by alleviating the load on the rotary drive.
2. DC blower
Komori’s DC blower achieves both economic and eco-friendly operation while maintaining the high-level airflow needed to properly stabilize the sheet. It significantly reduces power consumption through low-energy operation and minimal heat generation, all in a compact and lightweight design.
3. e-Mist
Komori’s revolutionary micro-mist system directly controls the humidity of the paper to combat the effects of static electricity. By controlling the humidification time, power consumption and water usage, the system keeps energy usage to a minimum. An added advantage is its enhancement of sheet alignment during delivery.
Updated KID (Komori Information Display)
Improved operator efficiency through an improved interface
All necessary printing information is available on a single screen
The KID screen layout has been redesigned for enhanced operational efficiency. Now, all vital printing information is conveniently consolidated onto a single screen. Operators have visibility to inline quality inspections, density control, next job data, register, presets and more. There is no need to unnecessarily toggle between screens—our intuitive interface ensures that all essential data is easily accessible, optimizing operator workflow and productivity.
Operators on all levels can easily switch between jobs
All necessary data for a job including current job progress, estimated time remaining and timing of operator actions, can be visualized. Even inexperienced operators can easily and efficiently navigate between jobs.