Inkjet & Digital Printing
Terenzi hits all the right notes following co-innovation with Ricoh
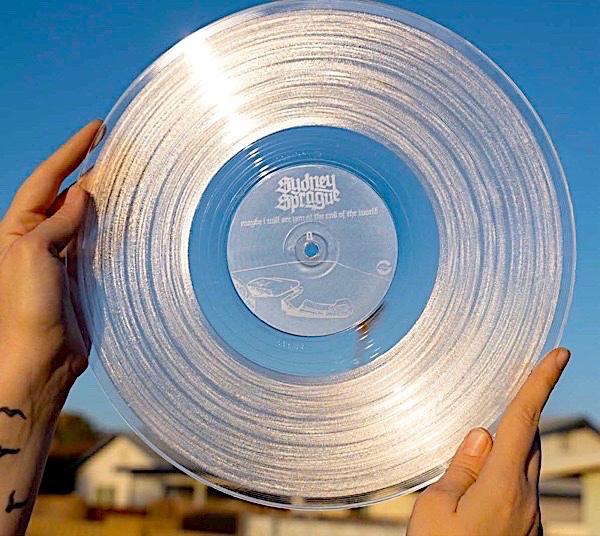
Friday 22. March 2024 - Instead of working with traditional, environmentally damaging, polyvinyl chloride (PVC) we collaborated with Rude Records on Greenyl a completely eco-friendly PET (polyethylene terephthalate) material made from recycled plastics, using sustainable production processes.
Guest blog by Luca Terenzi, CEO of Terenzi
When vinyl records began making their incredible comeback, we knew there was a huge opportunity to adopt a fresh approach to disc production that was both creative and sustainable.
We began with trials on a small printer, using standard inks, and printed the name of the artist, songs, album, and graphics, directly onto both sides of the record, eliminating the need for a separate paper label. We managed one Greenyl record at a time. When this attracted interest from music labels, we knew it was time to scale up production. That is when we asked Ricoh for help. We also wanted a solution that would reduce costs, streamline label printing, maximise digital innovation, and drive sustainability.
First Ricoh looked at the end to end process and workflow, to identify which products and services would be most applicable for our needs. They evaluated our requirements in terms of speed, quality, sustainability, and costs, before running tests using UV flatbed devices. The RICOH Pro TF6251 UV flatbed printer was identified as the most suitable device and we ran rigorous tests to ensure the technology and ink were suitable for the Greenyl material.
One key assessment criterion was the performance of Ricoh’s eco-friendly Ricoh’s Pro UV Ink GP120. When printed directly onto the face of the Greenyl records it provides strong adhesion and colour consistency and we can use CMYK colours, plus white and clear inks to create more vibrant and unique graphics for different artists. The precision and quality are excellent, allowing us to print very small text onto both sides of the record that remains completely legible. The instant cure UV inks also enable us to start printing immediately onto the reverse of the record once the first side is finished. And when the second side is completed, we can place the record straight into a sleeve ready for packing and dispatch.
Equally important, was the ability to ensure Greenyl record production is fully sustainable and environmentally friendly: for example, printing directly onto the disc removes the need to produce a separate paper label. We also liked the fact that Ricoh’s UV inks carry a Greenguard Gold certification that demonstrates they have minimal environmental impact and low chemical emissions while the use of long life LED lamps in the Pro TF6251 helps to optimise energy efficiency and reduce power consumption.
Next, Ricoh reviewed our processes, to see if we could help reduce production lead times and increase maximum print volumes. To achieve that they introduced us to RICOH ColorGATE Productionserver software, which creates print queues, manages print volumes, and manages workflows.
Finally, we co-innovated on the development of a jig tool to enable operators to place multiple discs in the right position on the Pro TF6251 UV flatbed printer’s table during production. We can print onto 16 Greenyl records simultaneously. When printing on one side is complete, we can flip the discs over to print onto the reverse.
Working with Ricoh has helped us take the innovative Greenyl concept from small scale testing to full industrial production. The combination of high print speeds, fast curing Ricoh UV inks, and the ability to print on multiple records simultaneously ensures exceptional productivity. And as production volumes increase, we will be able to deliver Greenyl records to music labels rapidly.
Ricoh provided excellent guidance during the initial consultation, including a detailed Total Cost of Ownership analysis. As we aim to produce well over one million Greenyl records annually, cost efficiency is an extremely important consideration. Ricoh gave us the confidence to make the investment.
Ricoh helped us create a production environment, not just a solution. Together we’ve been able to maximise value by integrating offerings from across Ricoh’s portfolio to meet our needs. We have been able to create an energy efficient and eco-friendly workflow in line with our sustainability goals.
But the work doesn’t stop there. We continue to have regular meetings to understand progress and identify where improvements can be made. We are now working on ways to expand our end to end solution and eventually hope to resell the concept and environment to other disc production companies.