Packaging
Ranpak Unveils Automated and Sustainable Packaging Solution for Fulfillment Centers in Japan
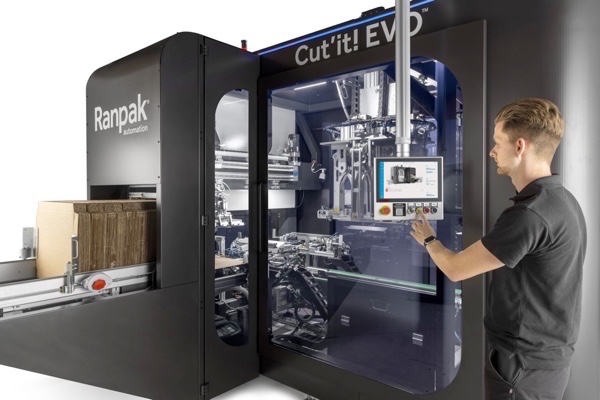
Monday 25. September 2023 - Ranpaks end-of-line packaging solutions deliver optimized fulfillment processes starting when e-commerce orders are placed and received for picking, to packing and shipping when the order is ready, thereby combining depalletization, picking and packing capabilities
Innovative paper-based packaging solutions, and integrated and highly automated packing lines, are just the beginning for this forward-looking company
Ranpak Holdings Corp. (“Ranpak”) (NYSE: PACK), a global leader of environmentally sustainable, paper-based packaging solutions for e-commerce and industrial supply chains, today reported that its next generation of the Cut’it! EVOTM in-line packaging machine, a more automated and sustainable future for packing and shipping of goods, is now available for distribution and fulfillment centers in Japan.
This improvement in end-of-line packaging is made possible by an increased use of technology, including vision systems, robotics and more.
“Ranpak has increased its focus on delivering integrated, automated end-of-line packaging solutions for distributors, packers and fulfillment centers that not only eliminate the need for plastics, but also speed the end-of-line packaging process, optimize labor requirements, eliminate unnecessary voids to reduce shipping volume and present the end recipient with a tamper-proof package that offers a much more pleasant unboxing experience,” said Masashi Nakamura, Ranpak Japan Country Manager. “For example, our Automation division enables inline scanning of boxes to enable the systems to take appropriate action such as minimizing unnecessary voids to reduce the size of boxes being shipped. We continue to look for ways to increase packing automation, with internal development, partnerships and close collaboration with our customers and their integrators. This is the future of the industry, and Ranpak is well positioned to continue in its role as the preeminent end-of-line expert for distribution centers. We are delighted to now be making these advanced packing solutions available to distribution and fulfillment centers in Japan.”
“Cut’it! EVO processes up to 15 boxes per minute,” said Nakamura. “It is a flexible solution that enables companies to follow the packing needs evolution, which includes the ability to pack an average of 25% more boxes per truckload, thereby reducing the number of trucks needed by up to 25%. Cut’it! EVO is easy to integrate into any packing operation with minimum impact on floor space, runs at high speed and reduces the need for labor and/or temporary staff, increasingly important in today’s difficult hiring and retention environment. The system can be configured for a wide variety of box sizes, ranging from 150x230mm up to 450x650mm. For larger boxes, Cut’it! XXL, up to 1,000x600mm, is available.”
Ranpak’s end-of-line packaging solutions deliver optimized fulfillment processes starting when e-commerce orders are placed and received for picking, to packing and shipping when the order is ready, thereby combining depalletization, picking and packing capabilities.
These complementary solutions, together with Ranpak’s extensive end-of-line packing solutions, provide automation of inbound, picking, packing and outbound processes and can be configured for packing operations of all types and sizes. Ranpak end-of-line solutions include:
Form’it!TM Case and Form’it!TM Tray, carton and tray erectors in preparation for packing ordered products;
A fully redesigned Cut’it! EVOTM to optimize carton size based on the highest level to which they are filled in order to reduce unnecessary voids; and
AccuFill and AutoFill for streamlining the preparation and insertion of exactly the right amount of paper void fill where that is required for extra protection during shipping.
“Our vision of the automation of end-of-line packaging is based upon our 50 years of experience in packaging ogether with ongoing feedback from customers using our equipment in the field,” Nakamura said. “This information enables our engineering team to ensure ongoing improvements to performance and to be able to adapt each machine exactly to customer requirements, always with sustainability in mind. This often includes recommendations about third-party components to be integrated for improved performance, including a variety of conveyors, robotics solutions and more.”
In addition, Ranpak continues its focus on delivering sustainable, paper-based packaging solutions that eliminate the need for plastics in the packing process. In support of this strategic focus, the company has announced targets to reduce its absolute greenhouse gas emissions by at least 46%; to source an aggregate paper supply consisting of at least 75% recycled pulp, including at least 25% from post-consumer waste or alternative pulp; and to sell 100% of their paper products as FSC-certified, all by 2030, just a few short years away. These targets are ambitious, but achievable and, more importantly, necessary.
Nakamura added, “Equally important, however, by announcing these targets, we hope to demonstrate our greater responsibility to our stakeholders, to the communities in which we live, to our employees and our families, and to our collective future as fellow members of a shared global vision.”
Nakamura points out that Ranpak is also taking advantage of additional technology developments, including cloud-based services, predictive maintenance, machine learning and artificial intelligence, to ensure these integrated systems deliver the best possible return on investment for customers, and position them to meet the ever-accelerating time to market requirements demanded by today’s consumers.
“This wide range of paper-based, automated packaging solutions is totally unique in terms of the seamless, streamlined and sustainable operation it powers,” Nakamura concluded. “We are looking forward to working with distribution and fulfillment centers in Japan to learn more about their existing and emerging requirements so we can help them move forward into a more sustainable future.”