Offset Printing
Stepping into the future has never looked this promising
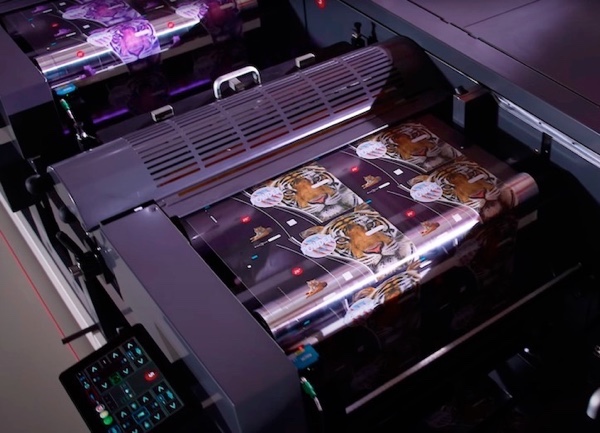
Tuesday 21. June 2022 - The Nilpeter FA-26 is the result of merging new technology with a user-friendly design, creating an effective machine center that yields minimal downtime and scrap, while offering maximum performance. A clear sustainable solution.
By Walt Mesik, Senior Sales Consultant, Nilpeter Inc.
As technology advances, machine manufacturers are obligated to integrate the latest and greatest offerings into their products to remain competitive in the world of inline web printing. As a general direction as to what technology our customers desired, Nilpeter listened. We learned our customers largest challenges were increased SKUs and reduced run lengths, as well as challenges to shift from pressure sensitive and paper substrates to unsupported films.
Already aware of the fact that the fastest growing market segment was flexible packaging, Nilpeter went to work creating the ultimate inline flexible packaging solution while addressing the customer needs. The Nilpeter FA-26 is the result of merging new technology with a user-friendly design, creating an effective machine center that yields minimal downtime and scrap, while offering maximum performance. A clear sustainable solution.
The FA-26 offers something for everyone – flexible packaging and value-added labels. All inline, sleeve-based anilox and plate roll. The robust unit construction, compact footprint, landscape design guarantee optimum register and consistent high print quality at all speeds. Designed to print with water-based and solvent inks, with UV, LED, and E-beam processes, the FA-26 is a winning combination for short and long run flexible package printing.
At a glance
A successful build relies on a solid foundation. The rigid one-piece steel frame guarantees our customers investment is long-term. The landscape style printhead offers superb printing quality & fast changeovers.
Temperature controlled ink chambers maintain ink temperatures throughout long runs at high speed – resulting in constant print density. Furthermore, the FA-26 features proven drying solutions for water base, solvent, UV, LED and E-beam inks, coatings & adhesives.
The ergonomics of the FA-26 offer a safe environment with every feature of the press designed to be accessed with “waist high” movements, and inline lamination utilizes floor level loading of heavy laminate rolls. Double-sided web printing (front/back) is exclusively accomplished with reversing printing stations eliminating the need for turn-bars. Multiple die-cutting solutions are available. Continuous operation-friendly design allows automatic unwind & rewind solutions as well as the standard Nilpeter roll-to-roll features.
Since introduction
Since the introduction, the FA-26 has exceeded customer expectations. With fast run speeds, industry leading Quick-Change features & job save/recall technology, the press uptime is maximized, and scrap amounts are minimized. Nilpeter customers have discovered In-The-Round sleeve technology (ITR) that allows them to run at speeds of 820 fpm (250 m/min), eliminating plate lift on smaller repeat sizes. ITR sleeves also reduce scrap significantly – when changing between jobs waste is regularly limited to 1 – 1-1/2 web lengths of the press regardless of the substrate webbed throughout the machine.
One of the tools Nilpeter has been using to help overcome the global labor shortage is using 100% inspection systems – every FA-26 to date has been delivered with such a quality control system.
Nilpeter understands your finished product needs will change to grow into new markets. As long as you have the floor space, the FA-26 can easily grow into whatever configuration is required to meet your needs. The modular construction allows for expanding the equipments abilities as new opportunities surface.
Nilpeters inline print finishing supports a wide range of substrates such as PP, PE, PET, and aluminum foil.
Die-cutting unit for quick job changes
Gravure unit for metallic inks, covering surfaces and coatings
Nilscreen system for special effects, braille, and opaque white
“Speaking as a Nilpeter representative, the most rewarding comment I have heard from an FA-26 customer is that “the FA-26 has proven itself to overproduce daily based on our ROI calculations. This has allowed us to investigate purchasing the next FA-26 for similar products in different locations that are currently struggling with competitors equipment,”” says Walt Mesik, Senior Sales Consultant, Nilpeter USA.
Working the press
For the FA-26, Nilpeter has taken into consideration that the operator can work the printing press without unnecessary handles. All functions on the press can be controlled via a touch panel on each printing unit. Nilpeter calls this intuitive concept “Clean-Hand” operation. Jobs can be saved logically and repeat jobs can be called up quickly. The entire operating concept is connected to Nilpeter’s Power Link System. It meets the industry standard 4.0 and can be integrated into all common MIS-systems.
To conclude
Simply stated, the Nilpeter FA-26 has only begun to impress with its amazing performance results. Nilpeter delivered a press built with advanced automation, state-of-the-art quick-change features, industry leading ergonomics & user-friendly operator controls. Stepping into the future has never looked this promising