Offset Printing
Flexo evolution supports sustainable progress in packaging
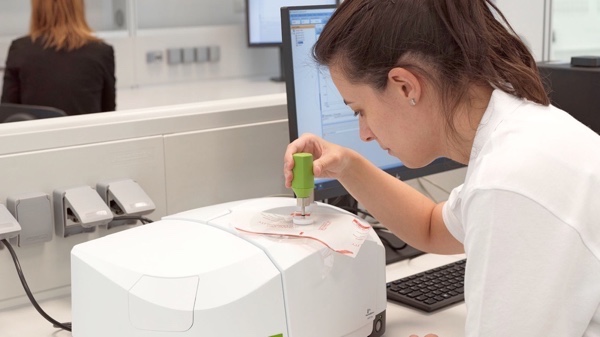
Thursday 09. June 2022 - The pivotal point of all packaging industry innovation is sustainability. All stakeholders from across the whole of the packaging supply chain understand that the only way to future-proof our industry is to embrace integrating responsibility at every stage.
But sustainability is not just about protecting the livelihoods of people in packaging; everyone relies on packaging whether they know it or not. Consumers, medical applications, ecommerce
plus myriad other uses need packaging to keep products safe, people healthy and purchases delivered intact. So really sustainability in packaging is about people. People doing the right thing with the skills, experience and knowledge that they have developed through working with packaging, from R&D to sales to logistics.
The role of machinery in the packaging industry is a great illustration of that pivotal role. By creating reliable, sophisticated machinery that can maximise the potential of the sustainable progress made with progressive substrates, water-based inks and fewer resources to deliver impressive results.
Results are crucial in this journey too, as brand owners are not willing to compromise on their expected quality, and understandably so. Consumers can be a tricky bunch to please, and brand owners are the closest link to the vote-with-your-feet public that most of us in the packaging industry need to keep happy.
But while consumers can be experts in their own spheres of influence, experts in the packaging industry need to be able to harness our knowledge in order to help direct those consumers into making smart decisions. Marco Carrara, Technology Sales Director at BOBST, understands how being an expert in the flexo packaging industry is its own responsibility when it comes to sustainability. He says, “Sustainability touches on so many subjects in packaging; the general focus on reducing gets a lot of publicity, so reducing waste, reducing water, reducing plastic
these are all certainly important. But we cant just keep using less of everything. We need to be smarter with what we use and how we use it, as well as how much we use.”
Being smarter clearly touches on many subjects too, but it is a more accurate way to look at sustainability than simply reducing. Reducing doesnt adequately address the requirements of the packaging industry where reduction needs to go hand in hand with innovation. Sara Alexander, MarCom Manager Flexible Packaging at BOBST, appreciates that balance. She says, “When we talk about sustainability in flexible packaging, we must remember that whatever the substrate, the printing is the last step in producing that packaging. By looking at different printing speeds, different drying techniques alongside understanding the substrates themselves and the inks being used, we can contribute considerably to the overall environmental performance and footprint of the product.”
oneECG flexo printed mono-material PET pouch
Meeting demand
Sara Alexander continues to explain how the extensive BOBST CI flexo portfolio optimises that contribution. “The BOBST CI flexo presses meet whatever demanding print applications customers ask of them; our full FlexPack portfolio offers a complete flexible packaging technology solution; we can do everything from converting to vacuum to coating to printing. The accuracy and quality of central impression flexo printing is well known already but thanks to our ongoing testing and trials, usually under NDAs, were able to analyse all the elements of the converting process to maximise that process for our customers.”
Maximising the process integrates sustainability as standard, with the dedicated R&D team at the BOBST Competence Centre at San Giorgio Monferrato in Italy continually working to fast-track solutions for customers across the packaging supply chain. Carrara continues, “We are lucky that people knock on our door; customers come to us to see how our Competence Centre can support their particular stage in the packaging process. Our customers and potential customers know that 2025 is just around the corner. The changing legislation that is already impacting considerably on key players throughout the supply chain means that brands and converters have to be ready. Sustainable packaging is not in the future anymore. All packaging must be sustainable. No one company or brand or converter can achieve that alone, so we must pool our expertise to deliver the most progressive packaging.”
Positive contribution
The idea of all packaging being sustainable in the not-too-distant future is an exciting prospect. Packaging, particularly plastic, going from being demonised to praised is welcome, especially when so many highly skilled experts – who are all consumers, parents and people too – are inspired to contribute to its positive development. Alexander adds, “BOBST is in the luxury position of being close to customers at all stages of the conversion process, so we can analyse what can be done better, where we can add value with going beyond standard configuration, how decks can be arranged differently, how we can help retain the packaging barrier properties. All the development in our portfolio is in the direction of sustainability; were building on our deep understanding of quality and accuracy and integrating responsibility wherever possible.”
Operator viewing platform on catwalk for web monitoring of the print result on a VISION CI flexo printing press
Understanding every stage of the converting process by listening to and learning from the challenges and requirements of customers means that the BOBST Competence Centre is privileged to be able to target the areas of the flexo packaging process that matter. Taking the already-known benefits of reducing ink, working with extended colour gamut, quick drying technology that uses less energy, understanding the performance of water-based ink and delivering accurate amounts of ink all certainly compound to provide advantages from a CSR perspective. But when all these – and more – are combined with technologically-advanced CI flexo printing presses, designed to work in tune with the most progressive substrates, then brand owners and converters can be assured that print performance is matched with sustainability.
Long-term BOBST customer AMB, a leading international company that delivers a unique difference to the food and food packaging industry, is happy to share its appreciation for how its investment in switching to 100% water-based technology in 2014 is allowing it to continue to compete effectively on the international market. As a company that is proudly active on a broad range of sustainability topics, its in-mind values highlight how everything we do is designed and considered to meet and exceed the needs of our customers. AMB is Designed to be different.
AMB has a complete product offering for the food packaging market that is totally environmentally friendly thanks to water-based inks, utilising several BOBST lamination and printing line machines that directly support its corporate social responsibilities actions. Its excellent results due to water-based technology include high quality flexo colour, printing on both top and bottom materials with rich, crisp, colour tone printing, and improved production times on a range of rigid and flexible films. The company also highlighted how this switch has positively contributed to its changed mindset, which is a desirable goal for the industry as a whole.
For the end consumer to be able to freely choose products because all packaging decisions have been made responsibly earlier on in the supply chain will mean that the upcoming legislation has encouraged key players in the packaging industry to act as they wish others to act. Sara Alexander concludes, “Were proud to be integral to the sustainable future of the flexo packaging industry. BOBST can work with different technologies, different substrates, different inks
but what never changes is our focus on sustainability.”