Packaging
Bruns Kartonagen has further strengthened its market position with top technology from BOBST
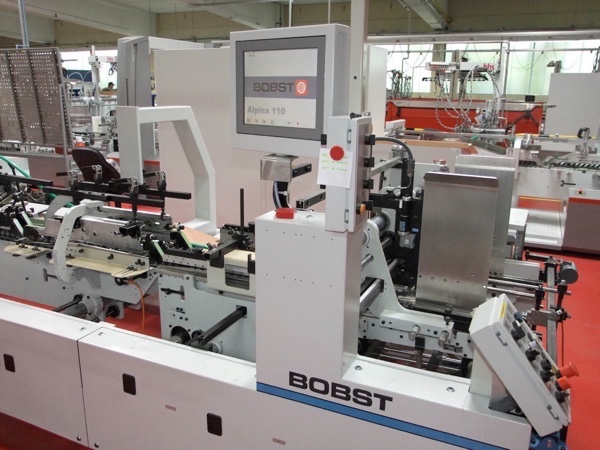
Friday 27. March 2020 - With 25 employees, four folding box gluers and three flatbed die-cutters from BOBST - among packaging manufacturers of this size, Bruns Kartonagen GmbH from GöttingenGermany stands out with its technical equipment. With a new MASTERFOLD 110 and upgrades to two of its three ALPINA machines, the company has further increased its attractiveness in folding box gluing at the beginning of 2019.
“One of our customers asked if we could give him a video on the high flexibility and production reliability of our MASTERFOLD 110. This alone shows how much this machine strengthens our market position,” says Karsten Hunger, one of the company’s three managing directors. With the same goal in mind, Bruns had one of his two ALPINA 110 folder gluers and his ALPINA 130 converted to the latest version of BOBST’s MATIC controller, new drive controllers and new motors.
Matchboxes, cushion packaging, presentation and bottle/glass boxes, six-packs, book slipcases, counter displays and many other packaging for customers in countless industries – the Bruns product range is extremely broad. Most of the orders come from industry, including the food and pharmaceutical sectors. In addition, agencies and packaging manufacturers, whose technical possibilities are limited, make use of Bruns’ services. “In folding box gluing, die cutting and laminating, we also work as a contract manufacturer. In extreme cases even overnight,” explains Hunger. Above all, the extensive possibilities of gluing are in demand in the market. Customers from all over Germany send pallets with printed sheets or already die-cut blanks to be processed into folding boxes in Göttingen. Hunger: “With our new technology we can react even more flexibly and quickly to market requirements.
New work feeling
The new MASTERFOLD 110 and the upgrades of the ALPINA machines have significantly increased the working comfort for the machine operators. The set-up process is considerably simplified. The MASTERFOLD 110 is set up about 30% faster for standard boxes and repeat jobs compared to the past. If the machine is completely set up for other nesting variants, Bruns saves 10 minutes of the previous set-up time. With up to ten production changeovers per shift, this is a considerable benefit.
The MASTERFOLD 110 is equipped with individual drives. These allow the design of the open frame platforms and give the operators direct access to all machine areas. This facilitates the installation of special tools and maintenance work. In addition, the design of the machine stands for a particularly high level of work safety. The closed floor areas of the frame platforms minimize the probability of blanks remaining in the machine during job changes and the possibility of mixing. The machine operators would see these at a glance. Finally, the individual drives guarantee quiet machine operation even at high running speeds. And they contribute to its particular energy efficiency.
A highlight for the machine operators is the central operation via the new HMI user interface attached to the feeder and the MATIC control system. The entire operation of the machine is integrated in it. Machine operators can switch between views at the simple touch of a button. The MASTERFOLD 110 from Bruns is equipped with four camera systems for monitoring “critical” machine areas. “Via the touch screen we make most of the settings and have the entire technology under control. This saves us many trips,” says one machine operator, citing the main advantage of centralized operation. “If, for example, the ACCUEJECT ejects faultily glued boxes, we can see from here what the cause is. If there are any technical difficulties in the machine, the causes can usually be located quickly via the touch monitor. “Especially in contract manufacturing, it is important to be able to guarantee customers the highest level of production reliability,” explains Hunger. “The MASTERFOLD 110 makes this much easier for us.
Many work steps automated
Depending on the type of folding carton, manual work during job changes is largely reduced to replacing and adjusting the tools. Easy access to all machine parts, centralized operation, and automatic settings thanks to the MATIC control system – all these features support the short set-up times of the MASTERFOLD 110.
The tools are compatible between the four folder-gluers, so they can be used on both the MASTERFOLD 110 and the three ALPINAs. Since the upgrades to the latest version of the MATIC control system, the ease of operation has also been significantly increased on two of these machines. Their intuitive menu navigation is largely identical to that of the MASTERFOLD 110, so operators can work with all machines without any problems. The third ALPINA was originally intended to be sold, but remains in operation as a back-up and for peak periods.
“BOBST provided us with perfect support during project planning and commissioning,” says Hunger looking back. With Helpline Plus, Bruns uses BOBST’s remote maintenance service. In order to be able to use machine data for process optimization in the future, BOBST’s three flatbed die cutters and the folder gluers are to be linked to BOBST’s Connected Services. This will allow an even better overview of production and access to the data while on the move – for example, to check whether orders can be realized in the event of short-term customer inquiries.
Bruns cardboard boxes
Today’s Bruns Kartonagen GmbH was founded in 1946 by Friedrich Bruns as a bookbindery. Today, the company offers its customers a complete range of services from folding box design and production to nationwide delivery with its own trucks.