Inkjet & Digital Printing
Inkcups introduces the revolution: New high-speed digital printing machine for cylindrical objects
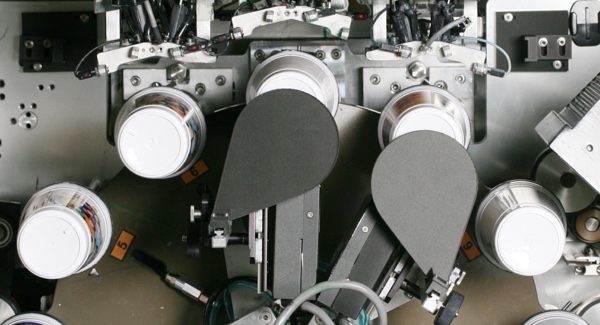
Wednesday 27. November 2019 - Inkcups, a leading global supplier to the printing industry, has announced its latest innovation and its most sophisticated system to date - the Revolution high-performance cylinder press. The Revolution is a fully automatic machine capable of printing around 600 parts per hour in full colour and high quality.
The system offers automatic loading and unloading, integrated pre-treatment of the items to be printed and patented spiral printing technology. Common applications include sports cups, beer and other drinking glasses, stainless steel and plastic drinking cups, cosmetic jars, glass and plastic bottles, beverage cans, oil filters and much more.
“We are excited to introduce the revolution,” said Ben Adner, founder and CEO of Inkcups. “The new machine offers everything we wanted to achieve when we launched the project more than two and a half years ago. We wanted to develop an industrial printing system for the optimal market area – a machine that is fast enough to produce real volume; that is flexible enough to allow fast job changes; that offers the excellent print quality our customers are used to; and that has a competitive price. The Revolution offers strong value for money – it is a production machine capable of printing large quantities at one-third the cost of comparable machines on the market. We are also proud that our new system is being developed, designed and built in the USA and supported by our team of experienced service technicians around the world”.
High speed for efficient production
The Revolution is the most technically advanced offering in Inkcup’s portfolio of digital printing solutions for cylindrical objects and represents an enormous increase in production volume over the company’s successful Helix model. Jobs that exceed the practical production limits of the Helix printer can easily be produced on the Revolution. Users can gain additional revenue from newly generated business and larger production volumes.
The inline feed path of the printing system can be loaded with the objects to be printed either manually by an operator or automatically by a robotic system to achieve a more streamlined process. The parts are automatically loaded onto twelve vacuum mandrels, deionized, subjected to a corona or plasma surface pre-treatment, printed and, after passing through the machine, unloaded onto a conveyor belt.
The Revolution seamlessly prints 360 degree circumferential images with a maximum resolution of 1,200 dpi onto a wide range of cylindrical objects and open conical vessels. The machine can print up to 220 mm high images on parts between 76 and 305 mm high and between 65.5 and 111 mm in diameter. The printing stations use Inkcups’ patented helical technology, which applies the inkjet droplets in a spiral pattern nested inside each other. The system’s printhead technology is capable of covering the entire length of an object up to 220 mm without additional printhead requirements. This allows better image quality to be achieved without stitching (joining print image parts together).
The Revolution is delivered as a turnkey package that also includes the premium InkcupCare warranty and service coverage. The machine is now available in North America and will be launched worldwide next year.