Finishing & Screen Printing
Heidelberg Stahlfolder PFX Feeder Technology Earns 2014 InterTech Technology Award
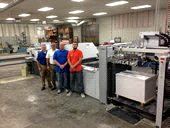
Thursday 28. August 2014 - Printing Industries of America has honored Heidelberg's Stahlfolder PFX (Pallet Feeder eXtended) Feeder Technology with a 2014 InterTech Technology Award.
“Lean manufacturing principles are more important in printing today than ever before, and the finishing department is rightfully acknowledged as a full participant in the drive to reduce costs, minimize waste and generate higher profits,” said Dr. Frank Schaum, Head of HeidelbergPostpress Commercial. “This is the 33rd time a Heidelberg innovation has received an InterTech Technology Award, and we are very happy and proud of it.”
Seamless Transfer from Press to Folder
The Stahlfolder PFX Feeder was recognized for its success in extending the proven benefits of the stream feeder technology used in Heidelberg offset presses to the folding department. Heidelberg’s Stahlfolder PFX Feeder Technology promotes lean production, reduces overhead labor costs, and increases net output up to 50 percent, compared with conventional production. The PFX also yields a 50 percent reduction in feeder faults, even on wavy or curled stocks. The feeder also makes the machine much more ergonomically operator friendly and allows users to achieve the highest run speeds without adding a helper to the operation.
Customers that have installed a high-speed folder with PFX feeder typically replace two or three existing machines, freeing up floor/intermediate paper storage space and reducing the overhead labor cost per shift, including costs associated with injuries due to the repetitive stress and strain of lifting sheets of paper onto a feed table. In addition to boosting efficiency with lower capital investment, the Stahlfolder PFX feeder also drives down the total cost of manufacturing while driving up profits.
“Heidelberg’s Stahlfolder PFX Feeder Technology enables postpress operations – often considered an unavoidable bottleneck – to keep pace with today’s supercharged pressrooms,” said Mark Bohan, vice president, technology and research, Printing Industries of America. “Our judges were impressed with the cost savings, productivity improvements, and enhanced profit potential flowing from the ability to drive sheets more efficiently through the shop.”
Unconventional Stability
The new feeder separates sheets on the pallet and transports them onto the vacuum feed table in a shingled stream, a prerequisite for processing more sheets in the same amount of time. This improves the consistency of feeding, requires fewer stops, and increases the total number of sheets that can be folded during an eight-hour shift. It is impossible to achieve ultra-high-speed, stable production like this with a conventional feed table. The new PFX feeder can be run in single mode or in shingled mode on the infeed. Heidelberg’s traditional Stahlfolder TH parallel folder and KH knife folder typically run in single mode. Heidelberg’s high-performance Stahlfolder TX parallel folder with twin pneumatic side lay employ the shingled mode.
J.S. McCarthy Printers (Augusta, Maine) became the first U.S. company to install a Stahlfolder KH 82 folder with PFX feeder last year. Said Vice President Jon Tardiff, “We’re doing 32-page signatures at 10,000 cycles per hour, and 16-page signatures at 14,000 cycles per hour, compared with 4,500 to 5,000 signatures per hour on the manual folder we replaced.” At this rate, he calculated, “We expect to do 20 to 25 million signatures a year on the new machine.”
“Modern Litho (Jefferson City, Mo.) has been a Heidelberg customer for many years, and we are pleased to say we are extremely satisfied with the PFX feeder on our Stahlfolder KH 82,” said Director of Operations Jim Tomblinson. “Heidelberg has greatly enhanced our productivity by supplying us with a machine that can operate at the highest possible speeds while maintaining the high quality standards our customers demand. This cutting-edge folding technology enables Modern Litho to be extremely competitive nationwide.”
“The new PFX system takes pallets directly from the press so operators can focus on count accuracy and the quality of the fold,” added Todd Bone, Director of Production. “It has greatly increased our folding capacity, providing more stability and predictability during the folding process.”