Offset Printing
KOMORI LITHRONE S29
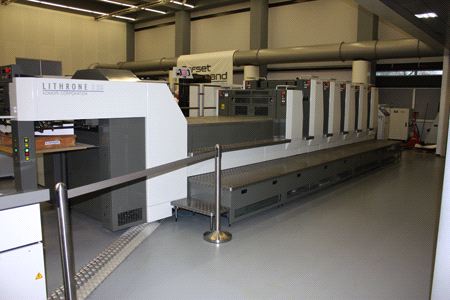
Monday 15. November 2010 - The development of the B2 Komori Lithrone S29 series was an extension of both the B1 Lithrone S40 series, and of the Lithrone 28 series.
Over many years it has been Komori’s regular practice to develop larger format presses first and then migrate the features to the smaller sheet size machines, so, having added several new features to the Lithrone 40 range to create the S models, it was a natural progression to add these features to the B2 Lithrones. These were launched in 2006, with a five colour model and a ten colour perfecting model shown at Ipex that year.
In looking at the development, Komori had also recognised that there was a growing demand for a slight but significant larger sheet size in the B2 market place to handle over-size promotional jobs and work such as folders and covers. The Lithrone 28 took sheets to 520 x 720mm, but the S29 takes sheets to the larger size of 530 x 750mm. Interestingly, though, because Komori has always maintained a significant share of the straightforward 26″ market, especially in its Asian markets – a format which is suitable for printers producing A4 sections, where a sheet size of 480 x 660mm is all that is required, Komori also incorporated the S features into its Lithrone 26″ presses, the designation being S26. That size of press is still highly popular in many countries and there are several printers in Europe content to keep to this smaller format.
Some of the many S series advancements include an initial start up speed of 12,000, which ensures that when the press speed is increased to 16,000sph, there is very little further adjustment needed for correct ink and water balance. The ink duct cheeks are of solid brass to ensure that in all conditions, there is no distortion which would prevent the ducts returning to a zero-set position when changing from job to job. The press also uses a pre-impregnated cloth for blanket washing, which reduces wash cloth consumption by some 50% and cuts blanket washing time down to a regular 60 seconds or so.
The main target for the S29 range is the general commercial field, but typical Lithrone features such as double size cylinder configuration, have also made the press popular in the smaller format, shorter run packaging market.
The Lithrone’s capability to print on heavier materials at high speed has supported this philosophy, and over the last couple of years, with commercial houses also anxious to find new markets, the Lithrone S29 has found favour with those general printers happily adding a little carton work into their production schedules .An example is Remous Ltd, based in Somerset, UK. Earlier this year, the company bought a five colour Lithrone S29 with the full automation package and Director, Alan Bunter says: “Previously we were a Heidelberg house, but we were impressed by the fast turnround speed of the Lithrone S29. We specified it with the Komori PDC-SII spectrodensitometer to maximise make ready speeds and to handle not just our general commercial work but also the comparatively short run packaging and book work we have built up.”.
As far is competition is concerned, all the leading manufacturers can offer presses of a similar size to the Lithrone, in particular Heidelberg, KBA and Ryobi, but Komori considers that the precision and
reliability of the Lithrone, along with a wide choice of options, including semi and fully automatic plate changing, puts it ahead of the competition in terms of productivity.
The Lithrone S29’s reputation has been enhanced since Drupa 2008 with the further development of its KHS high speed make ready system into KHS-AI. AI means Advanced Interface; the system progressively updates the press’s setting for ink levels, register and air control, whenever the operator makes changes, and then automatically sets to the latest suitable levels for each new job, taking the press closer and closer to immediate production quality level, and reducing waste to a minimum. In fact, Komori claims that on the majority of jobs, a press with KHS-AI is capable of producing saleable print within 20 or 30 sheets.
To emphasise the significance of KHS-AI, Komori’s demonstration procedure on the Lithrone S29 is usually to print three different short run jobs in under 12 minutes; as run lengths continue to reduce globally, this performance level is enabling the Lithrone to compete successfully with the digital presses, and with a top speed of 16,000sph, it also offers a level of versatility which continues to buoy sales in the short run marketplace.
The KHS-AI software also includes a Smart Sequence facility, which gives the operator the opportunity to pre-programme his own preferred pre-setting sequences such as wash ups and plate changing
There are now approaching 1,000 Lithrone S29 presses sold worldwide, covering all models in the range, which start with two colour machines, through 4, 5, 6 colours, and include 8 and 10 colour perfectors. Models in the Lithrone S29 range can have coating units – the 5 colour with coater being the largest seller in the UK – and drying units, as well as special packages for carton, UV and plastics application. The Perfecting models feature Komori’s unique 3 x double size perfecting mechanism, which reduces sheet distortion to a minimum and maintains precise register at the critical point of sheet turnover.
A recent addition is the Lithrone SX29, the “X” standing for extra sheet size of 610 x 750mm – popular in the US – and this X version is also available with in-line cold foiling, embossing, die-cutting and UV coating.
In Europe, Komori Lithrone buyers can call on a 24 hour parts service based at the company’s UK headquarters in Leeds which, as it is also the European spare parts centre, holds virtually every conceivable part in stock. Whilst the company does offer service contracts, the demand for these bespoke contracts is few and far between. Komori claims that the cost of ownership of its presses, including the Lithrone S29’s is probably the lowest in the industry, and points to its on-press Komori Management System as the best guide for the printer to ensure that maintenance is fulfilled correctly.” The system has a programme which reports continually on press condition and, as long as the operator keeps an eye on the feedback from this and reacts accordingly, the press should not suffer anything except standard maintenance breaks in productivity”, says European Marketing Manager, Philip Dunn.