Offset Printing
KOMORI OPEN HOUSE in Utrecht
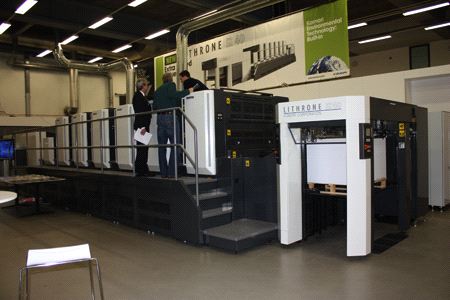
Friday 12. November 2010 - At the Komori European Open House in Utrecht, in November, Komori featured demonstrations on four Komori presses, the highlight being a detailed demonstration and description of the benefits of the Komori H-UV drying system, operating on the eight colour Komori Lithrone S840 P perfector.
H-UV is a new drying system which uses just one special ozone-free metal halide UV lamp in combination with a specially developed high-sensitivity UV ink. As well as being ozone-free, the H-UV lamp also generates far less IR radiation so the press will stay cool and can easily handle heat sensitive substrates.
The Lithrone S840P perfector at Komori’s Open House is fitted with two H-UV lamps, one after the first four colours and another before the delivery.
After the first four printing units there is one 160W H-UV lamp which is positioned over the perfecting vacuum cylinder. This dries the ink on the first side before the sheet is turned over in the perfecting unit. A second lamp is positioned after the second four units and is located over the upper delivery cylinder. This dries the second side before the sheet reaches the delivery pile.
Using H-UV drying on the Lithrone S840P, both sides of the sheet are dried instantly so there is no lost time when transferring the finished job to the cutting, folding and stitching process.
Unlike a perfecting press running conventional inks, the printing quality is identical on both sides of the sheet. The dry sheets can run easily into the delivery without any scratching and there is no need to allow non-printed gaps for the vacuum slowdown belts because the back of the sheet is dry. There is also no spray powder so the press and its environment can stay considerably cleaner.
The H-UV ink used by Komori has been specially developed to provide a combination of high gloss with maximum drying capacity.
The same high gloss ink can be used for all our different types of paper with no problems with ink curing, even when running at maximum speed.
The printing quality of H-UV inks is very close to that of conventional ink and when plate making for the H-UV process, the same dot gain compensation curve is used as for conventional inks.
Komori also announced other new technology at the Open House, including: Komori Lithrone SX40 RP, a new addition to the Lithrone S40 perfecting range. The RP suffix stands for Reverse Printer, the reverse printing mechanism enabling the press to perfect without the need to turn the sheet. This is likely to be especially beneficial when running heavyweight and rigid materials, such as heavy cover and carton boards. As there is no perfecting action necessary on the RP, makereadies can be performed with little or no adjustment to air settings, and another major benefit is that both sides of the sheet have the same front lay edge, so that imposition is simplified and the printable areas can be maximised.
The Lithrone S40 RP uses the same highly regarded double size cylinder configurations as all Komori Lithrone presses, this double size principle being maintained throughout the press, to ensure that even the heaviest materials are transferred mark-free and with the same precision at the highest running speeds.
A-APC asynchronous plate changing system.
This uses a motor to drive each plate cylinder independently during the plate changing sequence, and reduces plate changing time to just over 70 seconds, regardless of the number of press units. By using independent motors, the gear drives can be de-clutched so that all the plates change at the same time. When the plate changing sequence has finished, the cylinders automatically re-clutch and return to gear drive to ensure the highest quality print.
PDC-SX – Komori’s new spectrodensitometer – the next generation of the company’s well known PDC system. The PDC-SX is an X-Y spectrophotometer which can automatically locate and scan a printed colour bar in any position on the sheet. It will then automatically control the colour on the press throughout the run. The new PDC-SX also automatically controls the register by scanning strategically positioned micro register marks on the sheet. It will automatically control the register laterally, circumferentially and diagonally and it can also control any paper fan-out problems. When in use on a perfecting press, the SX will ensure that the upper and lower sides are in register with each other.
PQA-S – an extension of Komori’s online quality checking camera system already used very effectively on commercial carton and paper presses, high security currency presses and high speed web machines. This now includes closed-loop control of the colour, in-line on- the-run, from the very first sheet until the end of the job. It can use a standard colour bar at almost any position on the sheet to control any colour including Pantone. It can also control a four colour process image by scanning the full sheet with its high definition RGB camera and comparing it to an accepted standard.
20 Matching system, a combination of sophisticated software and specially developed press hardware which reduces the start-up waste to just 20 sheets per job. At the Open House, Komori demonstrated 20 Matching on the Lithrone S 840P, the 20th sheet not only matching a previously printed proof, but also being a perfect match to international colour standards.