Offset Printing
ROLAND 50 – XXL Press Technology in Format 36/52
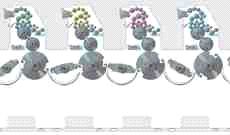
Wednesday 28. May 2008 - Big press features come to the A3 press market
The new ROLAND 50 consciously strives to set itself apart from existing format 36/52 presses. For the first time, the technology of “large” format highperformance presses will be used in the small format class. manroland is going to present a five-color ROLAND 50 on its drupa stand in PrintCity Hall 6 of the Düsseldorf trade show site.
Being able to quickly and economically offer and produce the most varied jobs is essential for smaller printing companies. If a printing company can add the extra dimension of product value to production efficiency, it improves its competitive position further. manroland’s strategy of Value Added Printing is designed to help printing companies do just that – every printing company, whether family-operated or corporation. The new ROLAND 50 in the 36/52 format was developed with this groundbreaking claim in mind.
Flexibility for success
The technology of the ROLAND 50 ensures efficient production while offering distinctive quality features. Double-size printing cylinders and transferters enable perfect sheet travel and thus excellent printing quality. This results in sheets free of marks and scratches. When it comes to printing substrates, manroland opens up new perspectives. The technology enables printing on 0.04 millimeters light-weight papers as well as on board up to a thickness of 0.8 millimeters – that is a substrate with up to 600 gsm. New customer groups can be developed with printed products that increase profit margins.
Lucrative short and large runs
Every run is a lucrative run. To ensure that this is also true for short runs, the ROLAND 50 in 36/52 format offers truly comprehensive automation settings that include automatic remote adjustment of substrate thickness as well as axial and radial register via the plate cylinders and – like with XXL presses – diagonal register works via the transferter. Another plus: ink presetting data is taken over all the way to the remote ink key control by JobCard. The QuickChange surface ink fountains, with specially coated surfaces for easy cleaning, support quick job change-over. An ink feed program leads to even shorter makeready times and less waste. Features such as automated plate change with EPL (ErgonomicPlateLoading), blanket washing devices, or online color control with ColorPilot smart additionally boost production efficiency. The maximum production speed of 13,000 sheet/h is more than sufficient for occasional higher runs of more than 10,000 sheets.
Inking unit technology in the “big” leagues
The ROLAND 50’s inking unit technology has been derived from the medium and large format and enables true manroland printing quality. Adjustment of the timing of the ink vibrator roller and connectable axial play of the four ink form rollers prevent potential ghosting. The three oscillating rollers in the 5-roller dampening unit are a further measure against such printing faults. The ROLAND 50 is the only press in this segment where you can choose between different characteristic
curves for the speed compensator in the dampening unit. That means that the dampening solution film is always constant, allowing the ROLAND 50 to offer stability and consistency in the production process.
Optimized special format
The press design is at the core of the ROLAND 50’s quality. Its massive base frame represents stability and robustness. With the RCI remote ink key control, the operator panel (integrated within the delivery) enables “one-man ease of use.” The ROLAND 50 is offered with two, four, five, or six printing units. The maximum sheet format of the standard version is 360 x 520 millimeters, and the minimum is 148 x 180 millimeters. The ROLAND 50 is the youngest member of the manroland
Plus family – the optional 38 x 53 centimeters format is unique on the market.
Ink presetting with CIP3 data
PressManager smart is capable of generating CIP3 data from the prepress stage, thus allowing ink slide presetting in the ROLAND 50. Ink presetting is an excellent starting position for the ColorPilot smart, optional available, which takes over control of the ink in the makeready and production run phases.
printnet networking for more efficiency
Increasing efficiency through networking is not only valid for large companies. printnet networking with the optional PressManager smart contributes significantly to shorter makeready times and more efficient production cycles. manroland offers two networking variants:
PressManager smart offline: relevant printing data can be written on a JobCard during the prepress stage and read out directly in the press using the JobCard reader. JobCard archiving allows repeat jobs to be completed quickly.
PressManager smart online: here the printing press is connected directly to the prepress. Data can be transferred from the prepress stage to the press without an intermediate medium. Printing data can also be processed, modified, and stored again on the ColorPilot smart PC.