Inkjet & Digital Printing
The craft of beer and the art of coding
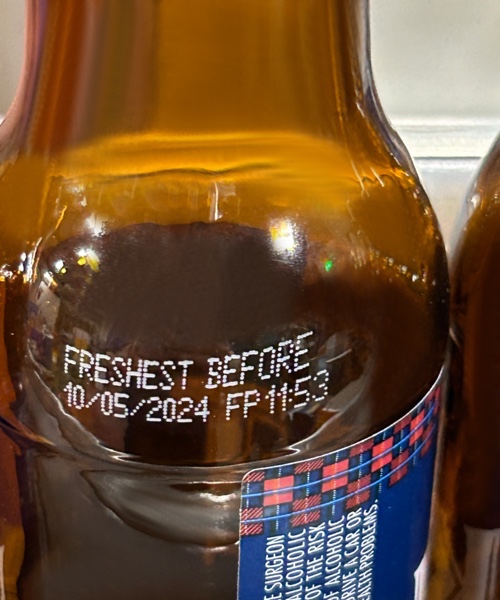
Thursday 17. October 2024 - To enjoy craft beer at its best, you need to drink it fresh. The Four Peaks brewery therefore prints expiration dates on every can or bottle, which encourage customers to consume the beer within 120 days of leaving the brewery.
Production downtime and unforeseen costs due to faulty marking systems posed significant challenges for Arizona’s largest brewery, Four Peaks. Frequent printhead clogs severely impacted production efficiency. The solution came with the switch to LEIBINGER’s innovative printing technology. Thanks to the patented nozzle seal technology in LEIBINGER printers, clogs are now a thing of the past, ensuring smooth, uninterrupted production and maximum efficiency.
At the vanguard of the craft beer industry in the US, Four Peaks is the largest brewer in Arizona and has built a loyal following since it was founded in 1996. Famous for beers such as Kilt Lifter and Wow Wheat, it was acquired in 2016 by beverage giant Anheuser Busch. Four Peaks is therefore not just the creator of awesome beers; it is a modern and highly efficient business, and the person responsible for ensuring high levels of both quality and quantity is Gary Fogg, Head of Production since 2018.
The challenge: A fresh approach to coding
This helps to ensure quality – but it can also create a headache for people like Gary because printing the expiration date can be problematic unless you have the right equipment. With LEIBINGER printers on every production line, Gary now enjoys problem-free operation, but it wasn’t always this way.
Before the LEIBINGER machines were installed, quality issues would often arise as the print heads on the other manufacturers’ printers became clogged. Every 15 minutes, the legibility of the print would be checked. If the expiration date was not perfectly clear, the production line would have to stop for up to an hour while the print head was cleaned.
Even worse, with 250 cans rolling off the line every minute, Gary might find himself with almost 4,000 mis-printed beers. That either means unnecessary time and effort washing and re-printing – or the beer gets wasted. And this happened at least once a week, sometimes even every day.
The solution: Listening to the voice of experience
This wasn’t the first time Gary had seen this problem and he had learned early that switching to LEIBINGER would solve it. Starting his career in one of the country’s largest beverage producers, Gary recalls similar problems with coding machines: “We were printing 24/7 and we would struggle with every other brand of printer. There was always one down and it had a big impact on our productivity.” The solution to that problem came from Tim Robinson of RMH Systems, a coding machine specialist, whose advice and support would prove invaluable throughout Gary’s career. Tim replaced the faulty machine with a LEIBINGER to keep production running. Gary came to trust LEIBINGER to work reliably where other brands failed: “Every time he [Tim] would come on site, we would put a LEIBINGER on and it would work straight out of the box.”
Fast forward to 2009 and his new position at Four Peaks, Gary faced the same problems with the same mix of manufacturers – and promptly replaced them with more reliable LEIBINGER printers: “When we first started we had [other printers] and I think both of those are in a dumpster out back. I don’t think I’d do that to one of my enemies.”
The impact on productivity was instant. “When I first started we were doing cleanings every week at least – sometimes every day. Now we don’t even have to do it every month.” Gary admits that the cleaning schedule they follow may even be unnecessary: “Sometimes I think we just clean the heads for fun.”
The sustainability advantage
There were other benefits apart from saving time. Cleaning print heads requires solvent, which can have a harmful impact on the environment. If the print head doesn’t need to be cleaned, you don’t need so much solvent – improving the environmental impact of the plant while also saving money.
Gary also points out the environmental advantage of LEIBINGER cartridges/ bottles: “They’re designed to empty completely – so no hazardous waste. With other cartridges, I had to empty residual solvent and ink into a tank and have it pumped out every month by specialists for proper disposal. That takes time and money.”
If you can’t stand the heat…
Breweries can be busy, hot, humid places, which makes coding difficult for some printers – but not LEIBINGER: “I’ve seen LEIBINGER machines working perfectly in possibly the most difficult environment you could find, such as above the pasteurization funnel where the air is damp, hot and dirty. But it still worked fine.”
Another problem arose with the condensation on the outside of pre-filled bottles. This meant that the soft-pigmented yellow ink Gary was using was flaking off instead of sticking to the glass surface. Tim suggested changing to a hard-pigmented silver, which adhered better. He also noted how the choice of LEIBINGER over competitive coders was important: “Once you put a certain ink in there, some machines are not big on changing. You have to change the nozzles, the oscillators, and we would never recommend it. With LEIBINGER you can just flush it out and start again with a different ink.”
The result: A focus on quality
The relationship between Gary and Tim is typical of the personal, local support that LEIBINGER’s partner network brings to customers around the world. LEIBINGER works closely with regional partners who are not only knowledgeable but also highly responsive, usually able to come to the site at short notice and advise on every situation. The craft of beer and the art of coding
Production downtime and unforeseen costs due to faulty marking systems posed significant challenges for Arizona’s largest brewery, Four Peaks. Frequent printhead clogs severely impacted production efficiency. The solution came with the switch to LEIBINGER’s innovative printing technology. Thanks to the patented nozzle seal technology in LEIBINGER printers, clogs are now a thing of the past, ensuring smooth, uninterrupted production and maximum efficiency.
At the vanguard of the craft beer industry in the US, Four Peaks is the largest brewer in Arizona and has built a loyal following since it was founded in 1996. Famous for beers such as Kilt Lifter and Wow Wheat, it was acquired in 2016 by beverage giant Anheuser Busch. Four Peaks is therefore not just the creator of awesome beers; it is a modern and highly efficient business, and the person responsible for ensuring high levels of both quality and quantity is Gary Fogg, Head of Production since 2018.
The challenge: A fresh approach to coding
To enjoy craft beer at its best, you need to drink it fresh. The brewery therefore prints expiration dates on every can or bottle, which encourage customers to consume the beer within 120 days of leaving the brewery. This helps to ensure quality – but it can also create a headache for people like Gary because printing the expiration date can be problematic unless you have the right equipment. With LEIBINGER printers on every production line, Gary now enjoys problem-free operation, but it wasn’t always this way.
Before the LEIBINGER machines were installed, quality issues would often arise as the print heads on the other manufacturers’ printers became clogged. Every 15 minutes, the legibility of the print would be checked. If the expiration date was not perfectly clear, the production line would have to stop for up to an hour while the print head was cleaned.
Even worse, with 250 cans rolling off the line every minute, Gary might find himself with almost 4,000 mis-printed beers. That either means unnecessary time and effort washing and re-printing – or the beer gets wasted. And this happened at least once a week, sometimes even every day.
The solution: Listening to the voice of experience
This wasn’t the first time Gary had seen this problem and he had learned early that switching to LEIBINGER would solve it. Starting his career in one of the country’s largest beverage producers, Gary recalls similar problems with coding machines: “We were printing 24/7 and we would struggle with every other brand of printer. There was always one down and it had a big impact on our productivity.” The solution to that problem came from Tim Robinson of RMH Systems, a coding machine specialist, whose advice and support would prove invaluable throughout Gary’s career. Tim replaced the faulty machine with a LEIBINGER to keep production running. Gary came to trust LEIBINGER to work reliably where other brands failed: “Every time he [Tim] would come on site, we would put a LEIBINGER on and it would work straight out of the box.”
Fast forward to 2009 and his new position at Four Peaks, Gary faced the same problems with the same mix of manufacturers – and promptly replaced them with more reliable LEIBINGER printers: “When we first started we had [other printers] and I think both of those are in a dumpster out back. I don’t think I’d do that to one of my enemies.”
The impact on productivity was instant. “When I first started we were doing cleanings every week at least – sometimes every day. Now we don’t even have to do it every month.” Gary admits that the cleaning schedule they follow may even be unnecessary: “Sometimes I think we just clean the heads for fun.”
The sustainability advantage
There were other benefits apart from saving time. Cleaning print heads requires solvent, which can have a harmful impact on the environment. If the print head doesn’t need to be cleaned, you don’t need so much solvent – improving the environmental impact of the plant while also saving money.
Gary also points out the environmental advantage of LEIBINGER cartridges/ bottles: “They’re designed to empty completely – so no hazardous waste. With other cartridges, I had to empty residual solvent and ink into a tank and have it pumped out every month by specialists for proper disposal. That takes time and money.”
If you can’t stand the heat…
Breweries can be busy, hot, humid places, which makes coding difficult for some printers – but not LEIBINGER: “I’ve seen LEIBINGER machines working perfectly in possibly the most difficult environment you could find, such as above the pasteurization funnel where the air is damp, hot and dirty. But it still worked fine.”
Another problem arose with the condensation on the outside of pre-filled bottles. This meant that the soft-pigmented yellow ink Gary was using was flaking off instead of sticking to the glass surface. Tim suggested changing to a hard-pigmented silver, which adhered better. He also noted how the choice of LEIBINGER over competitive coders was important: “Once you put a certain ink in there, some machines are not big on changing. You have to change the nozzles, the oscillators, and we would never recommend it. With LEIBINGER you can just flush it out and start again with a different ink.”
The result: A focus on quality
The relationship between Gary and Tim is typical of the personal, local support that LEIBINGER’s partner network brings to customers around the world. LEIBINGER works closely with regional partners who are not only knowledgeable but also highly responsive, usually able to come to the site at short notice and advise on every situation.
Tim also believes that LEIBINGER has a different approach to other coding manufacturers: “It seems like the other manufacturers are always pushing for annual maintenance charges. There’s always something that needs to be changed every year, regardless of use. But LEIBINGER is there to sell printers, not to try and make money on spare parts”
Four Peaks and LEIBINGER make good partners since both companies believe that success comes from quality, a point that Gary summarizes neatly: “At the end of the day, our job is to brew great beer and get it out there to thirsty customers. And coding should be such a simple task. If it’s legible and repeatable and we don’t have downtime, that’s all we need. And that’s what we’ve had for years now with LEIBINGER.”
www.leibinger-group.com
Tim also believes that LEIBINGER has a different approach to other coding manufacturers: “It seems like the other manufacturers are always pushing for annual maintenance charges. There’s always something that needs to be changed every year, regardless of use. But LEIBINGER is there to sell printers, not to try and make money on spare parts”
Four Peaks and LEIBINGER make good partners since both companies believe that success comes from quality, a point that Gary summarizes neatly: “At the end of the day, our job is to brew great beer and get it out there to thirsty customers. And coding should be such a simple task. If it’s legible and repeatable and we don’t have downtime, that’s all we need. And that’s what we’ve had for years now with LEIBINGER.”