Textile Printing
Why you should have designs on the hottest trend in garment decoration
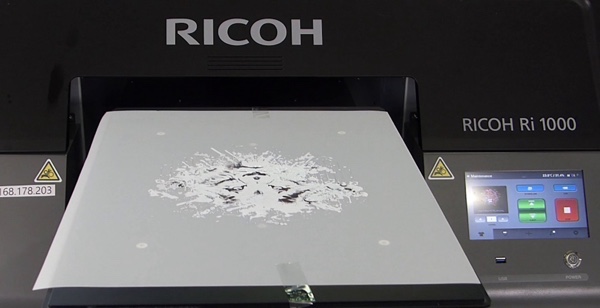
Tuesday 26. April 2022 - Direct To Film (DTF) printing technology has been described by Keypoint Intelligence as the newest and hottest decorated apparel trend. In just over two years it has emerged as an all-for-one technology. This is because it has a number of attractions.
By Axel Stuhlreiter, Head of Textile Solutions, Graphic Communications Group, Ricoh Europe
They include the ability to work with Direct to Garment (DTG) printing technology to produce a wide range of high quality sportswear and workwear, as well as corporate and promotional items, on a broader range of substrates like polyester and nylon.
DTF cost effectively delivers on demand, or short run print, as there is a shallower learning curve for printing DTF transfers and there is no need to pre-treat the fabric.
The transfer technology works by printing designs onto Polyethylene Terephthalate (PET) film using water-based pigment inks. The design is printed with CMYK ink first and then white ink. This is a reversal of the standard DTG approach of white ink first, followed by CMYK. At the same time the image is reversed so that its orientation is mirrored.
The wet ink is powdered with a hot-melt adhesive and then cured. The final cured image is transferred to the textile application using a heat press.
Among the benefits of the technology are:
Increased opportunities for customised, short run, on demand garment production by enabling printing on a wider range of fabrics.
Material versatility and suitability for fabrics not ideal for other production methods, such as water repelling surfaces like leather and nylon. Polyester can be used as well.
Durability and high fastness that makes it particularly suitable for applications such as synthetic sport jerseys. It is also ideal for workwear, promotional items and corporate branding.
Greater elasticity and stretchability for high quality results on a wider range of applications.
Very soft and flexible results.
Extensive colour options.
The ability to produce full colour, photorealistic images, and no limitations on complex designs.
The ability to prepare images in advance and apply to fabric at a later date. This prevents over production for a more sustainable approach.
Another benefit offered by Ricohs recently launched DTF solution is cost effective and fast production for low volumes.
The retrofittable technology can easily be combined with the capabilities of Ricohs existing Ri 1000 and Ri 2000 Direct to Garment printers to provide a broader portfolio of business winning applications. It also allows operations to maximise the utilisation of their Ricoh DTG printers and achieve a greater Return on Investment.
Designs can be pre-produced and stored as ready-to-go transfer film for quick application. High quality production is supported by ColorGATE Textile Productionserver V21.10. It accurately processes rich graphics from creative applications. Ricohs DTF technology also achieves very soft and flexible results and meets Oeko Tex standards.