Offset Printing
Komori exceeds expectations in the print quality for Gebrüder Güttler GmbH
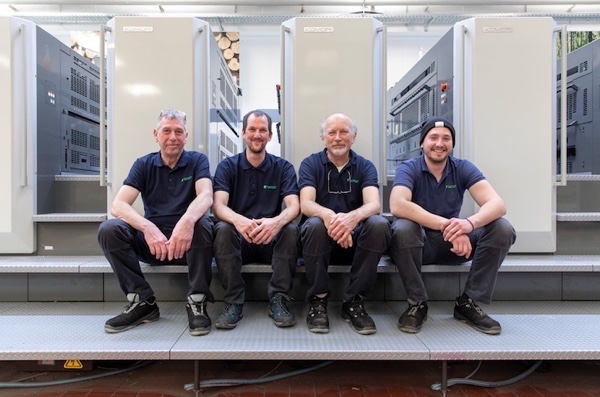
Tuesday 19. April 2022 - The production area of Gebrüder Güttler GmbH in Dietzenbach is around 1800 square meters. Six employees, including the management, work there in administration and sales. Four more work in printing and four in prepress, as well as 17 other employees in highly specialized postpress.
The company’s annual turnover is divided equally between label printing and flat bag production, mainly for plant seeds. This is a niche market in which Güttler with its highly specialized production processes is one of the few remaining European suppliers. In autumn 2021, the company invested in a new printing press.
The Komori seven-color Lithrone GL740+Coater is equipped with a PQA-S system, a camera-based inline color measurement and control system with inline quality inspection, and all the new features of the Komori Advanced series in a 40-inch format.
This includes new, state-of-the-art systems for smooth sheet transport in the feeder and delivery, a maximum sheet format of 750 x 1050 mm, a maximum print area of ??740 x 1040 mm, a print speed of 15,000 sheets per hour, both for very light and very heavy substrates and asynchronous, fully automatic plate change without plate bending (F-APC). This high-performance Komori press replaced an older KBA six-color+coater press.
Petra Güttler on the history of the company, and her own background
“Our family business was founded in 1907. We are now the fourth generation to run today’s print shop as cousins. I chose to study biology and I didn’t have any great ambitions to get into this trade. However, research work as a biologist was difficult to reconcile with the needs of my family and children, so after finishing my degree, I decided to do further training in typesetting and work in my parents’ company. After the birth of our second son, we relocated to the USA for two years. Upon our return to Germany, I first worked in a Würzburg typesetting studio and later in a printing shop there.
Eventually, my father wanted to know who would take over the company when he retired, and so I returned came to Dietzenbach in 2000 to support him in his business. In 2007, I became Managing Director. At the end of 2009, I completed a part-time master’s degree in business administration in order to get the necessary background for management. From that time on, my father began to withdraw from the day to day processes for health reasons. After his death in 2014, I was in charge of finances, something that had still been his responsibility as member of the supervisory board of our house bank. Ever since, I have managed the company together with my great-uncle Hagen Güttler and, as of 2011, his son Alexander Güttler.”
Founded in Zittau, Saxony
“Our company was originally located in the small town of Zittau in the border triangle in Saxony – founded in 1907 by my great grandfather Adolph Güttler and his brother Hermann Güttler. Our family has regained ownership of the historic company building in Zittau. In the late 1950s, it was expropriated and my grandfather and my father had to flee to West Germany and leave it behind. In the 1990s, my father negotiated with the Treuhand to get the family inheritance in Zittau back. Since that time, we have been running our subsidiary “Zittauer Offsetdruck” on this site. We first had to renovate and refurbish the factory with new technology.
Unfortunately, the production site in Zittau was never able to meet our expectations. We stopped the production in 2010, when, once more, major investments would have been necessary. We still use the building for sales. In addition to a caretaker, three further employees look after our numerous label customers, many of whom are based in former East Germany, and take care of print jobs. I myself am in charge of our major customers in the food sector. The labels are used for fruit juices, beer, baby food, pickled preserves, stock extracts, tomato sauces and spices. A growing proportion is used for products from the booming organic food sector. We print the labels here in Dietzenbach on gang forms and process them further by cutting and punching. My cousin Alexander Güttler takes care of the business with the seed bags, our second, important mainstay.”
Alexander Güttler on his production area
“As the youngest of three siblings, I was the only possible successor to my father, as both my sisters made it clear early on that they had no interest in joining the company. So at quite a young age, I decided to study business administration, and also got into commercial law. Prior to joining the company, I did not have too much to do with printing before I joined the company, so I had to pick up my printing knowhow as I went along. My father helped me greatly until he left the company. To this day, despite his advanced age, he is willing to help out whenever necessary. Our specialty has always been the production of seed bags and the production of catalogues and brochures for the garden sector.
We distribute those products across Europe, with customers from the Mediterranean all the way to Scandinavia. In fact, there are only very few producers in this market worldwide. It is not the press technology that matters here, but rather the special machines used in our postpress department. We have had the necessary know-how and technology for many decades and so we have found our niche in the competitive printing market.
We deliver the seed bags glued with an open flap as empty bags to the producers of plant seeds or to specialized filling companies. The production and sale of plant seeds has so far remained a stable market despite the corona pandemic. Seed procurement is now becoming increasingly difficult. The supply is limited and it actually happens frequently that seed quantities of certain production years are lower than expected. The demand for seed bags has been increasing again for some time. This has a lot to do with the increased ecological awareness in our society. For example, sowing wildflower meadows to protect bees has become enormously popular. Numerous municipalities and companies from all kinds of industries are riding this ecological wave and are giving away bags with flower seed mixtures to interested citizens or customers. “Save the bees” is the motto.
In addition to this, there is a growing interest of younger people in gardening. There is the “urban gardening” movement where people garden in the smallest of areas and in planters and other devices. A lot is grown there, from herbs to vegetables to a wide variety of flowers. And seeds are needed for everything. There are numerous suppliers in this “green industry”, many of which are among our customers.”
Petra and Alexander Güttler explain the details of the production
“Products trimmed to a high gloss with UV varnish and coated paper used to be in greater demand, but are now the exception for us. On the other hand, natural and recycled papers without any coatings or varnish are in vogue. Special colors are also in trend. In the past, we only had a four-color and a five-color press with coater from ManRoland for many years. That was enough. Today, products with at least two special colors are almost standard. The ManRoland presses were replaced in 2007 by a four-color and a six-color press with coater from KBA.
Our fathers always took the position that our company needed two presses in order to be able to limit the loss of production when repairs were necessary. Of course, that didn’t make economic sense. That was one of the reasons why we sold the four-color press in 2011. We only printed seed bags on it, because it was practically useless for our label printing without special colors. It was difficult to fill a full day’s shift with both presses and the postpress department couldn’t keep up either.
We could have increased postpress capacity, but selling the four-color press and moving all production to the six-color press made more sense to us. That soon proved right. The KBA press was followed last autumn by our new Komori seven-colour press plus coater. The press is linked to prepress via a state-of-the-art Fuji XMF workflow, which also includes a Konica Minolta digital printing system. We primarily use it to produce short runs of labels and seed bags.”
A well-considered choice for Komori
“With the Komori press, our company has now entered new territory. Our fathers were very conservative when it came to technical issues and always relied on German manufacturers. Buying a Japanese printing press would probably never have crossed their minds. But in today’s globalized world, one cannot really afford that mind set, because excellent technology is being developed everywhere in the world. We first found out about a press from KBA and had already tested it in Radebeul. At the same time, we also contacted the Heinrich Baumann company about a Komori press. Baumann’s offer for a comparable press was somewhat cheaper than that of KBA. Unfortunately, the planned date for a print presentation in March 2020 at Komori Europe in Utrecht was canceled due to the corona restrictions and could only be made up for in September.
In the meantime, we were a little unsure whether we should even make such an investment in view of the pandemic. Back then nobody knew how the whole thing would affect our market. Fortunately, the Corona situation has given our business both food labels and seed bags a boost. People were spending a lot more time at home, cooking instead of going out to eat, and maybe some rediscovered gardening. Rather, the pandemic has given us an unexpected increase in sales.”
Top print quality as benchmark
“One reason why we finally chose the Komori press was the truly convincing print presentation in Utrecht. We brought four of our own jobs for testing, with which we had had some printing issues in the past. These were, for example, a job on very thin paper, with a difficult register on the outside front, or a job on cardboard with a large area in the special color grey, which we almost never got printed without stripes. In addition, a job on embossed paper and finally a very demanding label job.
The tests in Utrecht were run on a five-colour Lithrone G40 with coater, which, in terms of technology, was almost identical to our new seven-colour Lithrone G40. During the tests, the focus was primarily on the print quality, which is at the top of our company’s requirements. Two of our printers attended the tests and were very impressed with the quality and also with how quickly and efficiently our four jobs in a row were processed. Before that, our master printer had been singing a different tune – he wished to stay with KBA. Nevertheless, we insisted on seeing the Komori press in Utrecht and afterwards he was really impressed. We have had the Lithrone G40 up and running since last October and our printers are still learning every day to get the most out of the press.”
Decades of trust
“Our business relationship with Komori sales partner Heinrich Baumann, which has existed for decades, also played an important role in our purchase decision. We know and trust each other. The branch is close by and they are there for us immediately when we need help. Without the support from Baumann, we would probably not have dared to switch to a Japanese manufacturer. Having sales nearby is an important criterion for us.
The Komori brand also has a reputation for offering a particularly dedicated service. In the past, we hadn’t always had the best experiences with other manufacturers. The press has now been in operation for half a year and fortunately no serious service cases have arisen so far. And that’s how it can stay for a while, as far as we’re concerned.”