Consumables
Partnership development in cold glue application and sensor technology
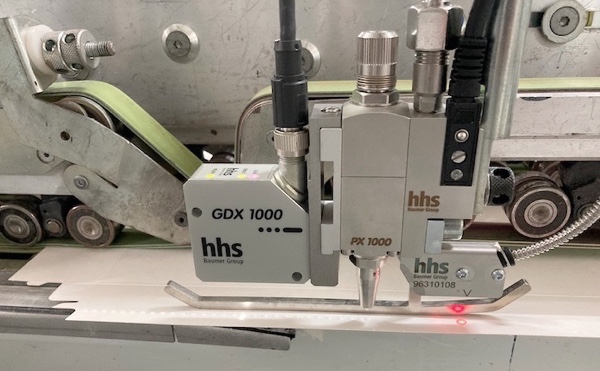
Monday 14. February 2022 - As a manufacturer of high-end folding cartons, WestRock plant in Düren is an ideal partner for Baumer hhs for practical tests of the latest technology. Only recently, the new PX 1000 cold glue valve and new GDX 1000 cold glue monitoring sensor were brought to market maturity here.
How the WestRock plant in Düren and Baumer hhs have jointly raised glue application and quality assurance in folding carton production to a unprecedented level
As a manufacturer of high-end folding cartons, the WestRock plant in Düren is an ideal partner for Baumer hhs for practical tests of the latest technology. Only recently, the new PX 1000 cold glue valve and the new GDX 1000 cold glue monitoring sensor were brought to market maturity here. The powerful combination of glue application with the PX 1000 and glue monitoring with the GDX 1000 sets a new standard, reduces quality costs in folding carton production and makes it easier for the plant to produce packaging of the highest quality.
“We always have the latest, best-in-market technology from Baumer hhs in our machines for adhesive application and the associated quality control. This allows us to explore their advantages for our customers at an early stage. At the same time, we influence the development with our high demands on the performance, ease of operation and reliability of our production technology,” says Giuliano Terracciano, Finishing Manager and Gluing Department Manager, explaining why Multi Packaging Solutions Düren GmbH, a member of the WestRock Group, is happy to assist Baumer hhs as a sparring partner.
The three-shift plant in Kreuzau-Stockheim specialises in the production of high-quality paper and board packaging for confectionery. Plant manager Dirk Matzke: “For our customers, the best quality is just good enough. Baumer hhs can put its innovations through their paces at our plant under the most demanding practical conditions – both for simpler, very fast-running and complex packaging. Our two companies have been working together very closely and trustingly at a high level for many years.”
The first prototypes of the new PX 1000 cold glue valve and the new GDX 1000 cold glue monitoring sensor were installed at the plant at the end of 2020. “Baumer hhs had approached us in the autumn about testing a new cold glue valve in one of our folding box gluers, which was also developed in particular for the production of complex packaging at high speeds. In the laboratory, the new valve had shown excellent results. Among other things, in start-up behaviour, in the precision of adhesive application and in its flexibility in the face of fluctuating adhesive viscosity. Baumer hhs now wanted to ensure that these advantages were confirmed in practice under demanding production conditions over a longer period of time,” Terracciano looks back.
Unique precision in adhesive application
Already after the first test runs in the equipped folder-gluer, the machine operators were enthusiastic about the new technology – it simplifies their work significantly. “The PX 1000 has to be cleaned less often. Therefore, there are significantly fewer cleaning-related production interruptions, which benefits productivity in packaging production. In addition, the new valve applies the adhesive precisely and filigree in a way that we have never seen before. This is a particular advantage for packaging products with small flaps and at very high machine speeds. It is easier than ever for us to avoid internal gluing and to ensure the functionality of our packaging,” Terracciano emphasises important changes that the PX 1000 has brought.
For example, in the production of folding telescope cartons with long-side gluing for chocolates, the PX 1000 applies the glue lines precisely from the defined starting points to the specified end points. Terracciano: “In general, the new valve once again significantly increases the reliability of the glue application and thus the production reliability. Our machine operators can rely on it: The adhesive is applied exactly where it belongs – and only there.”
Another advantage of the new valve that makes the work of the machine operators easier: the PX 1000 also works perfectly and reliably when it has to switch comparatively infrequently, as is the case in the production of folding-bottom cartons, for example.
“During the practical test, we suggested some optimisations to Baumer hhs. These were implemented perfectly,” Terracciano emphasises once again that both companies can exploit a wide range of synergies in the close partnership cooperation in the further development of technology for adhesive application in folding carton production.
A perfect combination
At the same time as the PX 1000, the prototype of the new cold glue monitoring sensor GDX 1000 was also installed in the folding box gluing machine. With its high resolution and its innovative measuring principle based on the latest electronics, it guarantees even more reliable control of the adhesive application up to the highest machine speeds. Especially in demanding folding carton applications.
“Above all, the monitoring of adhesive-free areas has been significantly simplified with the GDX 1000,” Terracciano emphasises one aspect. In edge areas, machine operators no longer need to define blind areas when setting up quality control. In teach-in mode, the high-performance sensor detects these independently – during operation and even on printed glue flaps. Set-up processes are reduced to a minimum, input errors are eliminated.
Also thanks to the more reliable measurement results, there are fewer production stoppages and rejects, which increases productivity and quality. Gone are the days when, in the production of automatic bottom or 4- and 6-point cartons, adhesive-free areas at colour transitions and slanted edges were sometimes identified as defects and blanks were therefore ejected even though they were perfectly glued. The GDX 1000 only detects real defects in folding carton gluing. And it does so with unprecedented reliability.
Thus, the higher precision of adhesive application with the PX 1000 goes hand in hand with the high reliability in monitoring adhesive-free areas with the GDX 1000. “The new technology makes it easier for us to achieve the required reliability and quality of our packaging. It allows us to further reduce our quality costs – both inspection costs and defect costs. This helps us enormously in our day-to-day business,” says Matzke, summing up the benefits. And, of course, higher production reliability also benefits the sustainability of both the manufacturing process and the packaging.
Focus on user-friendliness
The convenience of the user interface of the Xtend3 control units from Baumer hhs was also optimised in close cooperation with the WestRock plant in Düren. For example, machine operators now have direct access to all important functions in Xtend3, which saves them searching in submenus. In the menu, they can directly select the individual adhesive application valves. To simplify the necessary work in the submenus, they can switch between them with simple swiping movements. In addition, the visualisations, such as the visual representation of the glue monitoring, have been made much more practice-oriented.
The level guidance of the Xtend3 control units was also worked out in the factory. In Xtend3, for example, different levels or access authorisations can be set for different users. As a result, certain functions can only be accessed with the respective access authorisations assigned. This prevents machine operators from switching off functions. In addition, certain functions can be assigned to jobs, which must then be actively used. These options are now used by many packaging manufacturers around the world to increase production reliability. “Today, we are in the fortunate situation that we have very well-trained machine operators without exception. That is why we no longer need this option today,” says Terracciano.
Industry 4.0 gains importance
The new Xtend3 control units provide comprehensive machine and process data from the adhesive application, which can be used for further optimisations of this production step. This means they fit perfectly into Industry 4.0 environments. “Xtend3 gives us many options here. In the future, we will use these options especially for error analyses and for documenting our production quality,” Terracciano looks to the future.
For example, the factory can easily generate production reports with the Xtend3 systems. These document which quality assurance was used for which orders, whether the systems indicated errors in production and how countermeasures were taken. The reports can be made available to customers in the form of PDF files.
The machine operators prefer the new technology
Meanwhile, the new PX 1000 cold glue valve and the new GDX 1000 cold glue monitoring sensor are in operation in two of the total of five folding box gluers at this WestRock plant. Three of the machines were converted from Xtend2 to Xtend3. “If it were up to the machine operators, we would have already completely converted our folding box gluers to the new technology,” says Terracciano. Once that is done, he says, process efficiency throughout the gluing plant will get another boost.
“Adhesive application is a key quality parameter in packaging production. We must be able to rely completely on our technology here. Baumer hhs is therefore a very important partner for us. The high performance of its technology and services enables us to reliably produce quality for our customers – even to the point of avoiding under-mixing. Our customers know that we consistently equip our machines with technology that virtually eliminates errors. Especially in adhesive application,” says Matzke, summarising the significance of the partnership. In general, the name Baumer hhs stands for the highest quality. The new technology provides folding carton production with new options that the plant had not previously thought possible in this form.